Home > Plastic Mold Manufacturer: Process Debugging
HDPE Injection Molding
The main characteristic of Hdpe material is its plasticity under heating. Molten HDPE is injected into the mold through an injection molding machine and cooled to form a unique and advantageous molded part.
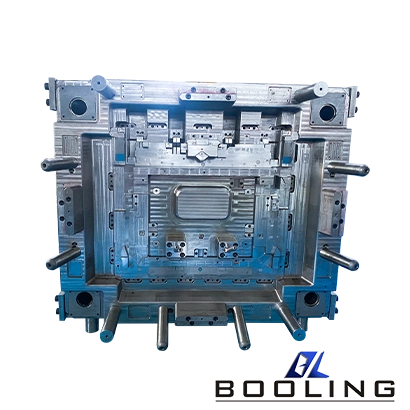
Plastic mold manufacturer needs to repeatedly adjust and set the parameters of the molds before producing or putting them into production. The goal of doing so is to obtain high-quality products that are consistent with the requirements.
Plastic mold manufacturer, with his outstanding plastic injection molding services, precise design operations, and highly automated injection molding technology, can efficiently produce plastic products with high flexibility, good strength and stiffness, high surface quality, and high aesthetics. They can be widely used in various fields, such as industry, agriculture, medicine, and so on. With ABS and HDPE injection molding technology, plastic mold manufacturers have also emerged in the automotive industry.
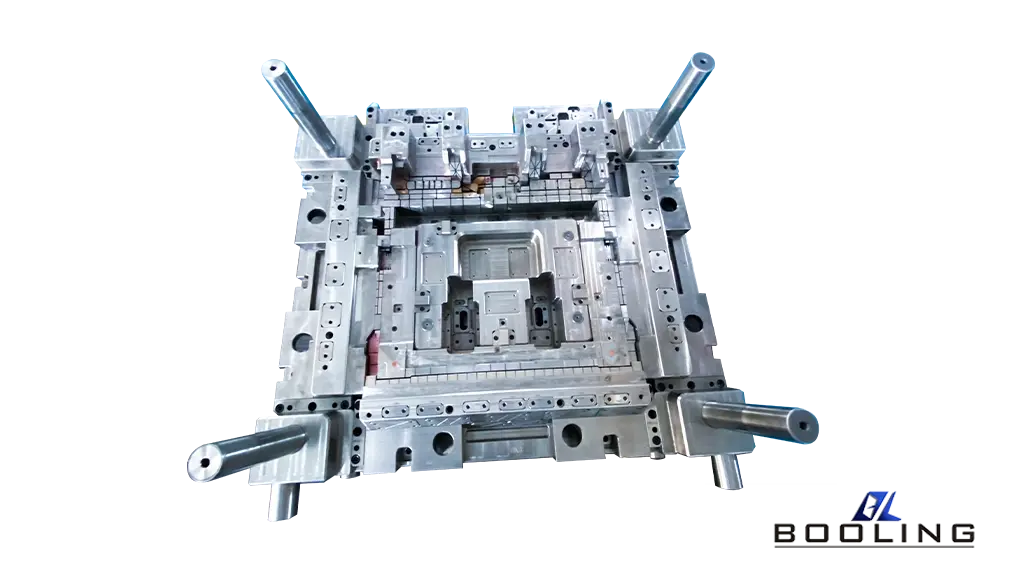
Preparation before Parameter Debugging
The mold parameter debugging process of the plastic mold manufacturer is repetitive and complex. Before debugging, certain preparations must be made to ensure that the subsequent parameter settings can proceed smoothly.
- Check the Equipment
Plastic mold manufacturer needs to inspect the oil pipes, inlet valves and water pipes, circuit wires, and mechanical transmission parts of the injection molding equipment they use, and maintain the equipment as required; Check whether the ejection method, nozzle aperture, positioning ring diameter, nozzle sphere radius, minimum and maximum mold thickness, pull rod spacing, and mold transfer stroke of the equipment meet the requirements for mold testing, and prepare for parameter debugging. The equipment used by the manufacturer during the trial mold should be consistent with the officially produced equipment. This is because the molding parameters of the product during trial molding are closely related to the equipment used, such as the amplitude of pressure changes, temperature fluctuations, air circulation time, and mechanical and hydraulic transmission stability. These all affect the quality of the product to a certain extent. If the locking force and other parameters of the trial molding equipment and formal equipment are different, other parameters also need to be readjusted, which is undoubtedly time-consuming and labor-intensive.
- Check the Design Drawings
Plastic mold manufacturers must strictly follow customer requirements and the drawings designed by the design department for mold debugging. Manufacturers need to check and calculate drawings to ensure that all dimensions and units are correct. Then, it is necessary to check the color and rounded corners of the products involved in the drawings. Finally, it is necessary to consider the dimensional tolerances and allowable defect range of the product. According to the design drawings of the mold, it is also possible to understand whether the equipment and technical parameters used for mold debugging meet the requirements of the mold, as well as whether other tools and accessories are complete. After completing this step of inspection, you can proceed to the next step of inspection and debugging.
3. Check the Mold
Before installing the mold onto the injection molding equipment, the manufacturer should conduct a comprehensive inspection of the mold according to the mold drawings, to promptly identify problems and make timely adjustments to the mold. From the assembly drawing of the mold, the dimensions of the positioning ring, external dimensions, inlet and outlet dimensions of the main flow channel, inlet and outlet of cooling water, and height and width of the pressure plate pad can generally be obtained. The pouring system and cavity of the mold need to be inspected separately for the moving and fixed molds. When opening, attention should be paid to the direction markings to prevent the direction from being changed when re-closing.
- Material Selection
Whether it is processing or debugging, the plastic raw materials selected by a plastic mold manufacturer should fully consider their performance, such as the specifications, models, density, water absorption rate, etc. For plastics with high water absorption rates, drying treatment should be carried out in advance, and the ratio of plastic raw materials and additives should be determined in advance. In general, suppliers will specify the raw materials used for trial molding or production, and can also use materials with low viscosity, good fluidity, strong heat resistance, and fast curing speed. Debugging the structure of the mold to accurately reflect the distribution of rounded corners, wall thickness, and reinforcing ribs in various parts of the product, can serve as a reference for modifying the mold in the later stage.
- Mold Testing Tools
The trial mold personnel have specialized trial mold tools. The commonly used mold testing tools include mechanical wrenches, spacer blocks, mold thermometers, measuring instruments for checking mold dimensions, and inspection tools for products. They also include essential items such as copper sheets, copper bars, and sandpaper commonly used during operation. The various inserts used in the trial mold, including rubber inserts, plastic inserts, metal inserts, paper product inserts, etc., as well as the fixed parts used to ensure that the products do not deform after molding, must be strictly tested by the manufacturer to avoid damage to the mold and irreparable losses.
- Cooling Pipes SsHeating Lines
The manufacturer should inspect the cooling pipes and heating circuits of the mold. If the parting surface of the mold uses a hydraulic or motor, they should also be inspected separately.
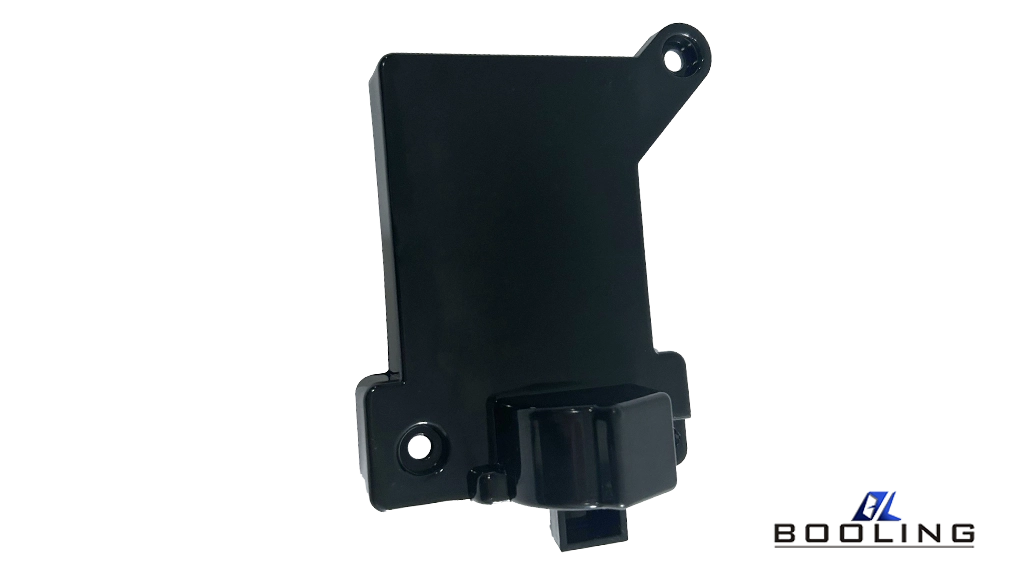
Setting of Injection Molding Process Parameters
For injection molding, the process parameters set by the plastic mold manufacturer will directly affect the final quality of plastic products, so the coordination and adjustment of various parameters are the most crucial.
Among all the process parameters, they involve parameters such as pressure, speed, and time. The pressure parameters mainly include holding pressure, injection pressure, locking pressure, etc; The time parameters mainly involve cooling time, injection time, low-pressure mold locking time, and cycle time, etc; The temperature parameters mainly involve the melting point of various plastics, the heating temperature of each heating section, the heating temperature of the nozzle, the mold temperature, and other parameter settings; The speed parameters mainly include mold opening speed, injection speed, mold locking speed, and melting speed; The position and stroke parameters mainly involve stroke changes during mold opening and locking processes, as well as stroke position control during injection processes. When setting these parameters, it is necessary to consider the technical conditions of the injection molding equipment and the actual processing process. It is also necessary to design and modify the plastic raw materials based on their performance and structure, as well as the plasticizing speed and degree of the machine melting cylinder. We also need to conduct trial molding, and after discovering defects in the product, adjust and modify the parameters promptly to avoid similar problems in the later stage of the product, and to enable the injection molding machine to run more smoothly.
The technical parameters set by the plastic mold manufacturer should be appropriate and meet the requirements of the design and product well. When debugging and calibrating parameters, it is necessary to strictly follow the process flow and operating rules of equipment and molds. When conducting calibration and trial operations, manufacturers should avoid setting pressure parameters too low but flow parameters too high, and setting pressure holding parameters too high and flow parameters too low.
Unreasonable pressure and speed parameter settings can lead to many problems that plastic mold manufacturer finds difficult to solve, such as:
-Setting pressure or speed parameters too low can cause dents and bubbles in plastic products; Vacuum bubbles, flow lines, and water ripples appear on the surface of the formed part; The surface of the product has defects such as ripples and welding marks; The product becomes brittle and fragile, with defects such as layered gates.
-Setting pressure or speed parameters too high can cause a change in the color of the product, resulting in defects such as black spots and lines.
-Excessive pressure parameters can easily lead to plastic overflow and excessive flash in plastic molded parts, which can result in defects such as glue leakage, mold sticking, and poor demolding, leading to product breakage or cracking.
-Low-pressure parameters can easily lead to defects such as shrinkage, insufficient glue injection, rough surface, inconsistent dimensions, incomplete filling of mold cavities, and silver threads or spots on the surface of plastic parts.
-Excessive speed parameters can easily lead to defects such as burnt products, inadequate transparency, and defective plastic products.
-Low-speed parameters can easily lead to defects such as roughness, warping, and deformation on the surface of the product, greatly affecting its aesthetics.
Unreasonable time parameter settings can easily lead to:
-If the injection time is set too short, it can lead to short shots or insufficient filling of the mold cavity, resulting in defects such as dents, bubbles, and silver streaks. It can also cause inconsistent product dimensions, brittle and prone to cracking, and poor plastic performance.
-Setting the injection time too long may lead to defects such as product overflow, glue leakage, product adhesion or gate blockage, gate layering, and poor demolding of formed products.
-If the cooling time is set too long, it can lead to product defects, such as mold sticking to the gate or forming cracks or ripples in the product.
-Setting the cooling time too short can lead to product warping, unstable product dimensions, clogged or unable to form water outlets, and the fragility of plastic molded parts.
-If the holding time is set too short, it can cause the size of the injection molded product to be unstable, resulting in silver threads, spots, dents or bubbles, and even possible defects such as product brittleness.
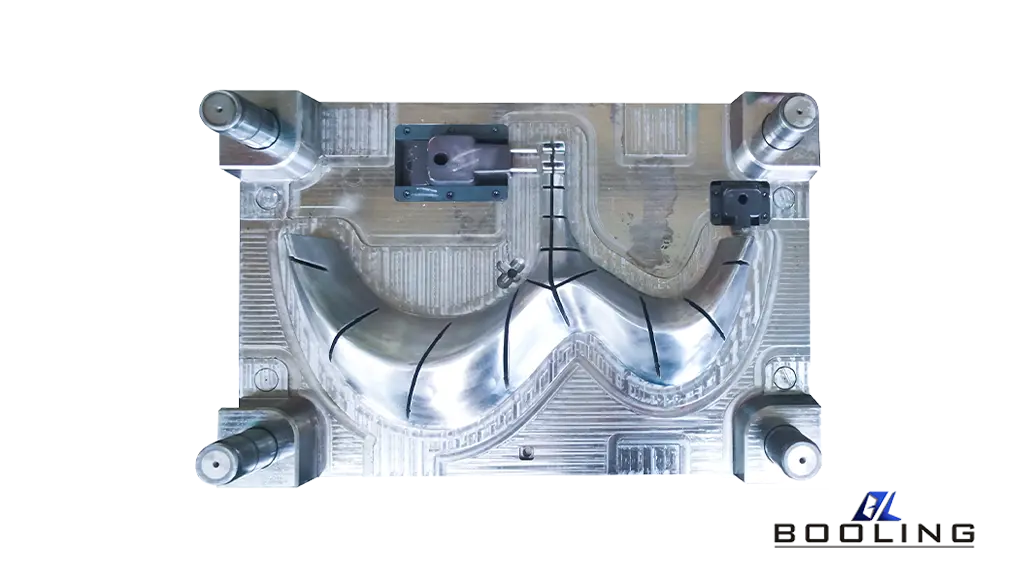
Related News
Applied’s expertise in modifying materials at atomic levels and on an ihdustrial scaleenables our customers to transform possibilities into reality.