Home > Plastic Mold Manufacturer | Plastic Injection Molding
Plastic Mold Manufacturer | Plastic Injection Molding
Plastic Injection Molding
Details
Details:
Model
Material
Brand
Origin
Application
Booling-Injection-1
P20, 718, S136, 2738 etc
Booling
China
Automotive parts, industrial parts, medical parts, household
Plastic injection molding can process thermoplastic and thermosetting plastics, as well as certain thermoplastic elastomers. It has a wide range of applications, material choices, and flexible processing.
Advantages of Injection molding:
- High Precision and Repeatability
- Low Cost per Part
- Fast Production Rate
- Wide Material Choice
- Little Waste
Related Hot Products
The products manufactured by the plastic mold manufacturer involve many fields such as household appliances, instruments, and meters, construction equipment, the automotive industry, and daily hardware. A mold is a tool used to produce plastic products, which consists of several sets of parts, each with a molding cavity inside. During injection molding, the mold is clamped onto the custom injection molding machine, and molten plastic is injected into the mold cavity, cooled, and shaped inside the cavity. Then, the upper and lower molds are separated, and the product is ejected from the mold cavity through the ejection system. Finally, the mold is closed for the next injection molding, and the entire plastic injection molding process is cyclic.
Plastic mold manufacturers generally go through several processes such as forging, cutting, and heat treatment when manufacturing molds. In order to ensure the manufacturing quality of molds, reduce production costs, and ensure more efficient production, their materials should have good malleability, machinability, hardenability, hardenability, and grindability; They should also have antioxidant properties, decarburization sensitivity, and no tendency for quenching deformation and cracking.
Injection Manufacturers Choose Plastic Mold Raw Materials Guide
Plastic mold manufacturer needs to choose different plastic materials when creating plastic molds for different products, and they often choose based on different plastic characteristics. When selecting materials for molds, the principle of economy must be considered to minimize manufacturing costs. The following are several commonly used raw materials for plastic molds:
- Polyethylene (PE)
Polyethylene is generally in the form of white powder or granules, which have excellent water resistance and electrical insulation, low water absorption, and certain breathability (therefore, plastic mold manufacturers generally do not choose PE to make packaging shells for cigarettes or spices). But its strength is relatively low and it is prone to softening at high temperatures (above 80 degrees Celsius).
- Polyvinyl chloride (PVC)
Polyvinyl chloride is divided into rigid polyvinyl chloride and soft polyvinyl chloride based on the amount of plasticizer used. It is lightweight, chemically resistant, has good resistance to flow, has high mechanical strength, and good electrical insulation performance. However, due to its weak heat resistance, it is often necessary to add heat stabilizers during processing, which may lead to the toxicity of PVC materials. A plastic mold manufacturer usually does not choose to produce food plastic packaging.
Polypropylene (PP)
Polypropylene is a colorless and odorless semi-transparent solid with good chemical resistance, heat resistance, and electrical insulation. However, due to its poor aging resistance, it is not possible to produce plastic products that require long-term use.
Polystyrene (PS)
Polystyrene has a low water absorption rate and good optical, electrical, and radiation resistance properties. However, its strength is low, and it is easily damaged, brittle, and prone to breakage when subjected to impact. However, manufacturers often use it in the production of children’s toys.
ABS
ABS has high strength and toughness, and this material is easy to process and form and has a wide range of applications.
Polycarbonate (PC)
PC has high strength, good reusability, stable size, high-temperature resistance, and excellent electrical performance. A plastic mold manufacturer usually develops this material towards high composite, high functionality, specialization, and serialization, and it is widely used in automotive lighting systems, surgical masks, water storage bottles, LED light casings, and other products.
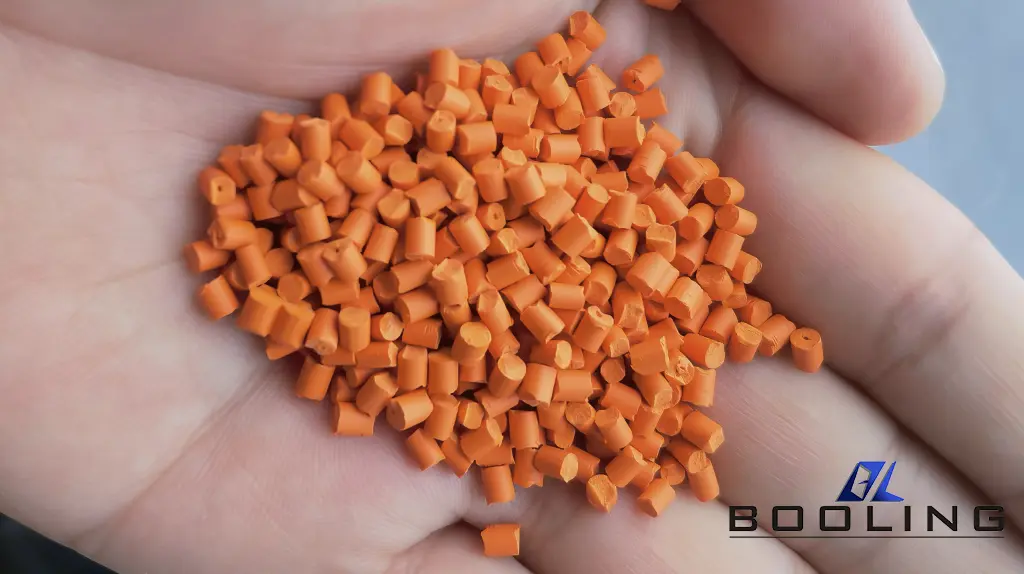
Applications of Plastic Injection Mold
The plastic products produced by plastic mold manufacturers are applied in many fields, and people are increasingly dependent on plastic products. Plastic products are mainly used in the following fields and industries:
- Packaging Materials:
- Film: Light and heavy packaging film, barrier film, heat shrink film, self-adhesive film, rust-proof film, tear film, air cushion film, etc;
- Packaging bottles: packaging bottles used for various types of food, beverages, cosmetics, drugs, and chemical reagents;
- Packaging box: Box-type packaging used for food boxes, hardware, handicrafts, cultural and educational supplies, etc;
- Packaging boxes: beer boxes, turnover boxes, toolboxes, corrugated boxes, etc;
- Cups: beverage cups, milk cups, yogurt cups, etc;
- Packaging bags: plastic bags, woven bags, etc.
- Daily Necessities
- Daily necessities: such as tables and chairs, chairs, luggage, pots, buckets, boxes, plates, etc;
- Kitchen utensils: various types of tableware, such as bowls, plates, plates, knives and forks, spoons, cutting boards, etc;
- Clothing products: such as synthetic leather, shoe soles, buttons, hair clips, zippers, raincoats, etc;
- Cultural and sports supplies: such as stationery boxes, pens, rulers, ball products, etc.
- Agriculture:
Including all kinds of agricultural land film, greenhouse film, fire and irrigation pipe, spray, fishing net, etc.
- Industry:
- Electronic and electrical: such as high, medium, and low voltage insulated cables, various connectors, connectors, relays, capacitors, switches, junction boxes, etc;
- Mechanical products: such as various casings, gears, bearings, pull rods, chains, seals, etc;
- Automotive accessories: such as instrument dials, bumpers, steering wheels, fuel tanks, fuel pipes, ashtrays, etc.
- Architecture:
- Pipe fittings: water supply pipes, drainage pipes, threading pipes, gas pipelines, ball valves, tees, etc;
- Profile: doors and windows, furniture, stair handrails, decorative strips, etc;
- Board: decorative board, ceiling, floor, aluminum-plastic composite board, sun board, insulation board, etc;
- Other: carpets, wallpapers, artificial marble, waterproof rolls, etc.
- Other Applications
- In terms of medicine: medical devices such as syringes, infusion tubes, infusion bottles, infusion bags, etc., artificial organs such as artificial bones, trachea, blood vessels, etc;
- Optics: optical lenses, reflective materials, solar materials, optical discs, etc;
- Aerospace: High temperature and corrosion-resistant materials and insulation materials used for the exterior of high-speed aircraft, as well as materials with high structural strength such as aircraft fuselage, tail wings, and vertical wings.
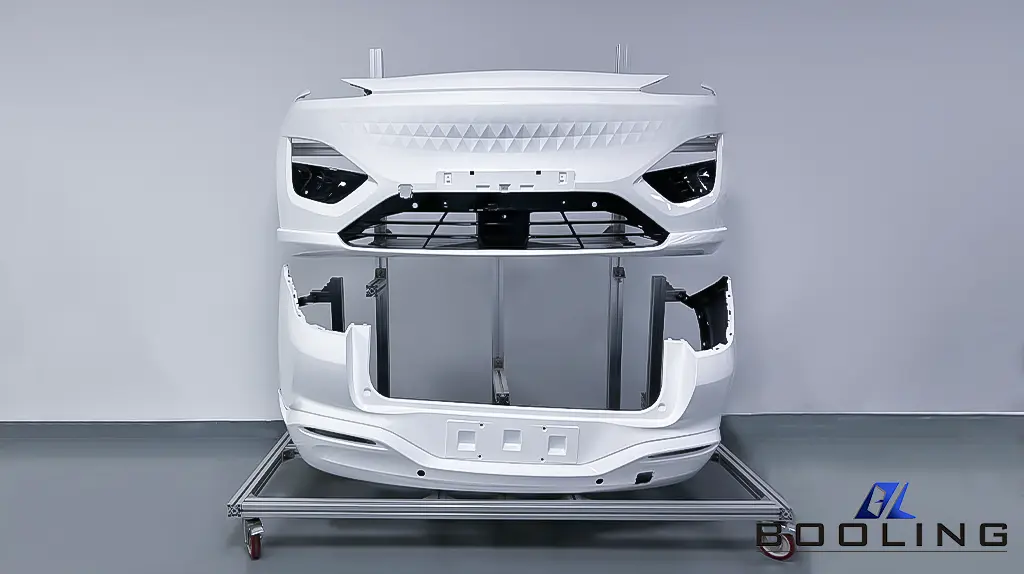
Key Points for Manufacturers to Design Plastic Mold
Plastic mold manufacturer needs to design plastic molds based on certain key points. This way, the precision of the designed plastic mold is high, which helps to improve the level and quality of the mold, shorten the mold-making cycle, and save metal resources. The design points mainly include:
- Clarify the design requirements for Plastic Parts
According to the requirements of the usage environment and working performance of plastic parts, the feasibility and economy of the design process should be considered from various aspects such as the material type, structural shape, dimensional accuracy, and surface roughness of the plastic parts. When necessary, it is necessary to discuss or inquire with the product designer about the types of materials used in the plastic parts and whether there is a possibility of structural modification.
Plastic mold manufacturer needs to design plastic molds based on certain key points. This way, the precision of the designed plastic mold is high, which helps to improve the level and quality of the mold, shorten the mold-making cycle, and save metal resources. The design points mainly include:
- Clarify the Production Batch of Plastic Parts
To reduce costs, plastic molds produced in small batches need to be as simple as possible; On the premise of ensuring the quality of plastic parts, plastic molds produced in large quantities should be produced in the initial simulation inspection as much as possible, using multi-cavity or high-speed automation to shorten the production cycle, accelerate the production cycle, and improve production efficiency. Therefore, the automatic demolding mechanism for plastic parts and flow channel components imposes stricter requirements on the ejection mechanism of the mold.
- Refer to Relevant Manuals and Record the Relevant Parameters of Plastics
For example, shrinkage rate, allowable minimum wall thickness, demolding angle, plastic molding pressure, mold cavity temperature, and related molding process (parameter) requirements.
- Overall Design of the Mold
The overall design of the plastic mold by the manufacturer includes the determination of the orientation of the plastic part in the mold, selection of the parting surface, selection of the pouring system, overall structure of the formed parts, selection of the exhaust method, structure of the ejection mechanism, structure of the side parting and core pulling mechanism, and the way the pouring system releases the condensate.
- Calculations Related to Mold Design
Including calculation of working dimensions for formed parts, determination of cavity wall thickness and bottom plate thickness; and Determination of heating and cooling systems for molds.
- Pre Selection of Plastic Molding Machines
When choosing a plastic molding machine and mold, the manufacturer needs to consider the following aspects: calculating the volume and mass of the plastic parts, and determining the relevant parameters of the injection machine through calculation; Calculate based on the number of cavities in the mold and the basic structural elements of the plastic part: injection amount, locking force, and plasticization amount; Based on the requirements of injection pressure, preliminarily determine the model of the injection machine and record the technical parameters related to the injection machine and the designed mold.
- Detailed Design of the Mold
This step requires detailed design and necessary design calculations for each part of the mold based on the overall plan and the necessary conditions of the selected plastic mold forming machine; Determine and purchase mold frames based on the overall size of the mold; Based on the above mold component design, draw a preliminary complete structural diagram of the mold.
- Parameter Verification of Plastic Molds and Plastic Molding Machines
Verification of maximum injection volume and plastic mold; Verification of injection pressure; Verification of locking force; Check the relevant dimensions of the installation and movement parts of the mold and injection machine.
Related News
Applied’s expertise in modifying materials at atomic levels and on an ihdustrial scaleenables our customers to transform possibilities into reality.