Home > Thin Wall Plastic Injection Molding | Production Mechanism and Key Points
In the field of plastic injection molding, thin-walled products can be easily manufactured, and their production mechanism and key points are similar to ordinary injection molding, with better performance.
Advantages of Plastic Injection Molding:
- High Precision and Repeatability
- Low Cost per Part
- Fast Production Rate
- Wide Material Choice
- Little Waste
Thin wall plastic injection molding requires raw materials with good fluidity, rigidity, and heat resistance to be better applied in fields such as automobiles and electronic appliances. At the same time, manufacturers also need to consider whether plastic raw materials have low-temperature impact rigidity, flame retardancy, mechanical assembly, and good appearance quality. The commonly used thin-walled plastic injection molding materials currently include polycarbonate (PC), acrylonitrile butadiene tea ethylene (ABS), PC/ABS blends, and PA6. As the wall thickness continues to decrease, the raw materials that need to be used also need to have better physical properties to maintain the strength of the product. In addition, it is necessary to dry in advance during the HDPE, PP, and ABS injection molding process.
The definition of thin wall injection molding can be divided into the following three types: the ratio of the flow length L to the thickness T, that is, the ratio of the flow length L to the corresponding average wall thickness T from the point where the melt enters the mold to the far point where the melt must be filled, is 100 or 150 or more for thin wall injection molding; Secondly, the injection molding method where the thickness of the formed plastic part is less than 1mm and the projected area of the plastic part is more than 50 square centimeters; Thirdly, injection molding with a wall thickness of less than 1mm (or 1.5mm) or a V/d (plastic thickness t, plastic diameter d, for circular plastic parts) below 0.05 is defined as thin wall injection molding.
Improvement Methods of Thin Wall Injection Molding Process
Although thin wall plastic injection molding has many advantages, it reduces the molding probability of plastic parts, making it impossible to shape these thin-walled plastic parts using conventional injection molding methods. When forming thin-walled plastic parts, the following common problems exist:
- Short Shot
A short shot refers to the quality defect of incomplete plastic parts caused by the incomplete filling of the mold cavity, which means that the melt has already solidified before the filling is completed.
Conventional injection molding combines the filling process with the cooling process. When the polymer melt flows, the front edge of the melt touches the surface of the relatively low-temperature core or cavity wall, causing a condensation layer to form on the surface of the mold. The melt continues to flow forward within the condensation layer, and as the thickness of the condensation layer increases, the actual cavity flow channel gradually narrows, which significantly affects the flow of the polymer. The impact of the condensation layer on the plastic parts of conventional injection molding is not significant, as the thickness of the plastic parts is relatively thick. But in thin wall injection molding, when the ratio of the thickness of the condensation layer to the thickness of the plastic part gradually increases with the thinning of the plastic part, the impact is significant. Especially when the dimensions of the two can be compared with each other, it becomes more obvious.
As the thickness of the plastic part decreases, the influence of the condensation layer on the flow of the melt will increase exponentially, which also demonstrates the crucial role of the condensation layer. If only from the perspective of injection molding, the injection molding machine must have a higher injection rate, so that the rate of plastic melt filling the cavity is faster than the rate of condensation layer growth (or the growth rate of the condensation layer is slowed down), so that the filling action can be completed before the flow section is completely solidified, and thin-walled plastic parts can be injection molded.
When the flow length is 300mm and the wall thickness of the plastic part is 3.0mm, it is easy to achieve an L/T of 100 using conventional injection molding techniques; But when the wall thickness of the plastic part drops below 1.0mm, conventional injection molding techniques are very difficult to achieve.
- Warpage Deformation
Uneven internal pressure leads to warping deformation, a plastic defect. The main reasons for warping deformation can be divided into three parts, namely uneven shrinkage, uneven orientation, and uneven cooling.
Improvement method: The defect of warping deformation in plastic parts can be improved by balancing the cooling system, adjusting the cooling time, changing the holding pressure, and controlling the holding time.
- Fusion Line
A fusion line is the boundary formed when two or more melts flow forward and fuse in a mold cavity. Pressure concentration is prone to occur at the fusion line, which weakens the mechanical strength of the plastic part, and brings adverse results to the mechanical performance of the plastic part, especially thin-walled plastic parts. Under the influence of external forces, it is easy for the plastic part to crack at the fusion line, increasing the probability of scrap.
Improvement method: During design, the position of the fusion line can be reduced or changed by reducing the number of gates or changing the gate position to meet the design requirements of the plastic part.
- Shortage of Materials
There are certain degrees of defects in the small parts and corners of the injection molded product, mainly caused by incomplete mold processing or poor exhaust. Design defects or insufficient thickness of the plastic part are caused by insufficient injection dosage or pressure during molding.
Improvement methods: The mold technician can be entrusted to repair the missing materials in the mold, take and improve exhaust measures, increase meat thickness, improve the gate (increase the gate, increase the gate), increase injection dosage, increase injection pressure, and other measures to improve the missing materials.
- Shrinkage
This defect often occurs in areas with uneven wall or flesh thickness of formed plastic parts, and may also be caused by different degrees of cooling or curing shrinkage of hot melt plastics. If the back of the rib, the edge with sidewalls, or the back of the boss column steals meat, but at least 2/3 of the meat thickness is retained.
Improvement method: Improvements can be made by thickening the flow channel, increasing the gate, adding exhaust, increasing the material temperature, increasing the injection pressure, and prolonging the holding time.
- Airlines
Due to the low mold temperature, high injection speed and pressure, and improper setting of the gate, the plastic collided with the turbulence structure during pouring, resulting in this defect at the gate.
Improvement method: It can be solved by changing the inlet gate, polishing the runner, increasing the cold material area of the runner, increasing the inlet gate, adding bite marks on the surface (by adjusting the machine or repairing the mold rod combination line), increasing the mold temperature, reducing the injection speed, and reducing the injection pressure.
- Burr Edge
Due to poor mold closing or improper processing of mold edges and corners, insufficient locking force, high material temperature, and pressure are often present during molding. The resulting burr defect often occurs at the junction of male and female molds.
Improvement method: Can perform mold correction, re-compare and close the mold, increase mold locking pressure, reduce material temperature and injection pressure, control holding time, reduce holding pressure, etc. To address this deficiency through methods.
- Drawing Die
This defect is affected by insufficient draft angle or rough mold surface, forming conditions, and mainly manifests as poor demolding, mold damage, and drawing.
Improvement method: Increase the draft angle, polish the mold surface, add or change the pull pin when sticking to the mother mold surface, pay attention to the diameter of the bull horn when feeding, add bite marks to the male mold, reduce injection pressure, and reduce holding pressure and time.
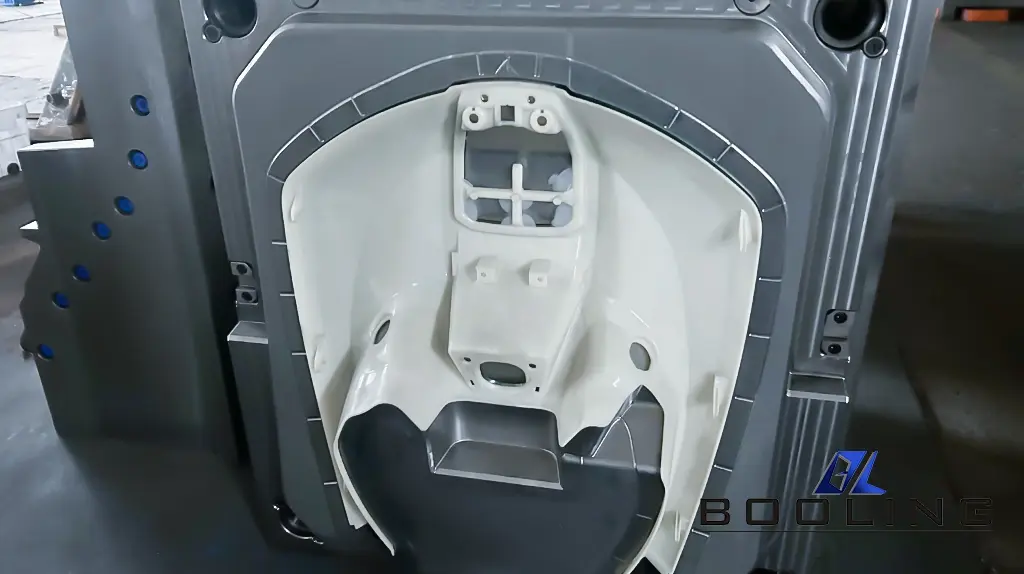
Thin Wall Plastic Injection Molding Process
Thin wall injection molding has certain requirements for the structure, material, mold structure, and injection molding process of thin-walled plastic parts. By improving the structure of thin-walled plastic parts, selecting suitable material, improving the mold structure in a targeted manner, and selecting a reasonable injection molding process, it is completely possible to solve the quality problems of thin-walled plastic products and meet the growing demand for thin-walled plastic parts. Because plastic parts can be made into various complex shapes, it poses great challenges to the structural design and manufacturing of molds. Both domestic and international efforts are being made to research and improve the application of thin-walled plastic parts technology. I believe that through the continuous accumulation of experience in the production of thin walled plastic parts, the promotion and application of thin-walled plastic technology will be rapidly popularized.
The Filling Process of Thin-Walled Injection Molded Plastic Parts
In the production process of plastic parts, the plastic melt is filled into the mold cavity through diversion channels and gates, and the molten material attached to the mold wall becomes a solidified layer, reducing the flow channel. Thin walled plastic parts, due to their small wall thickness, have narrower flow channels and are prone to material shortages. Therefore, thin-walled plastic parts require higher injection pressure and injection speed to fill the mold cavity. In addition, faster injection speed can also increase the shear temperature and increase the flow distance of the molten material.
Thin Wall Injection Molding Process for Plastic Parts
In addition to molds, the selection of injection molding process parameters (time, pressure, temperature) is very important for the production of thin-walled plastic parts. As the injection pressure increases and the time is shortened, it will bring certain difficulties to production. Therefore, a specialized thin-walled injection machine is crucial. Thin walled plastic parts have a thin thickness, light weight per piece, and require less injection molding each time. The cylinder volume of the thin-walled injection machine is relatively small, which can avoid the decomposition of plastic raw materials due to prolonged residence time.
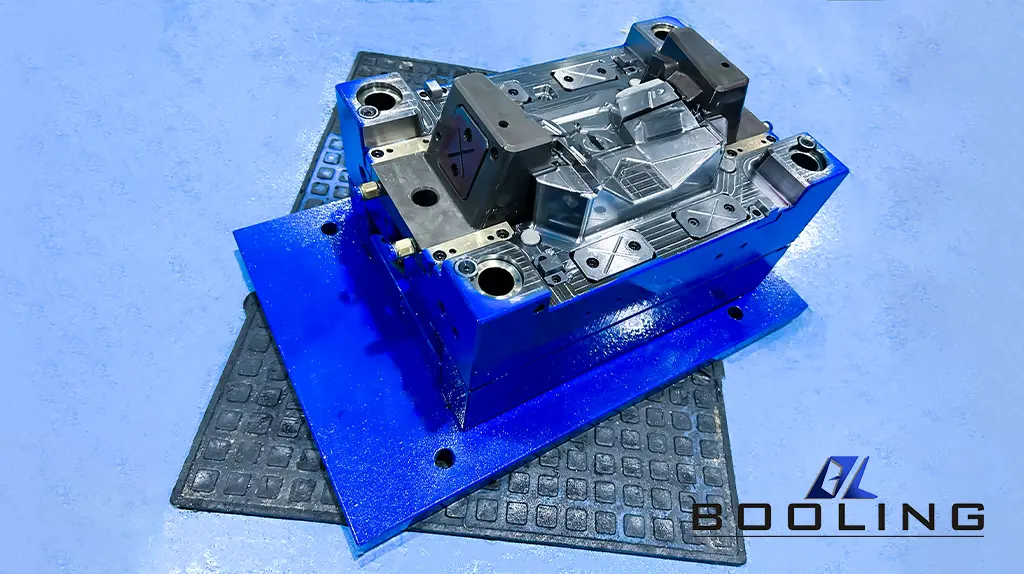
Design Points of Thin Wall Injection Molding
Thin wall injection molding has different levels of requirements in product design, machine selection, mold manufacturing, and molding process due to its unique shape characteristics, and each link is crucial, which will affect the quality of the final product. The following are the design points of thin wall injection molding:
- Selection of High Fluidity Materials for Thin Wall Injection Molding
In terms of material selection, because the thickness of packaging thin-walled products is generally below 0.6mm and the flow length ratio is generally greater than 200, the thin wall injection molding stage has a fast cycle, and the product cools and solidifies very quickly during the molding process. Therefore, it is required that the material has very high fluidity to achieve rapid injection molding and filling. At present, thin wall injection molding mainly uses polyolefin materials, such as PP and PE, as well as PET, PS, PA, ABS, PC, etc.
- The Design of Thin-walled Injection Molded Products Considers the Layout of the Injection Port
In the design of thin-walled injection molded products, the layout of the injection port is also a key point. Try to keep the injection balanced, so that the filling of the entire product can be evenly balanced. In addition, the design of the exhaust should also be given special consideration. For some wider products, which have thicker walls, and are thinner, exhaust plates can be used for exhaust. Pay attention to the arrangement of exhaust fins as perpendicular as possible to the final convergence line, which is very effective in increasing exhaust efficiency. For example, mobile phone battery cases, because phones on the market are no longer heavy, we also hope to make electromagnetic cases as thin as possible. So, exhaust plates are usually installed on the back of the battery shell, which can effectively discharge gas from the mold when filling air.
- High-Speed Machine Selected for Thin Wall Injection Molding
Thin walled injection molding machines can choose high-speed machines with speed-increasing mechanisms. For example, the screw plunger type is a classic thin wall injection molding machine, which can well meet the molding needs of thin wall injection molding. The injection speed is fast, and it uses screw storage and plunger injection. In addition, some equipment such as nitrogen and oil cylinder speed increase can also be selected as thin wall injection molding machines.
In addition, the clamping mechanism of thin wall injection molding machines also has higher requirements, such as precise motion and stability. In the packaging field, the in-mold labeling process is usually used. Before injection molding, labels are quickly and accurately placed in the mold cavity while the formed products are taken out. This requires close coordination with efficient mechanical arm movements, requiring precise opening and closing of the mold, fast response, and smooth movement.
- Mold Material, exhaust Groove, and Gate Design for Thin Wall Injection Molding
Many factors need to be considered for thin-walled injection molded products, such as mold material, mold exhaust, gate, etc. The material of the mold is very important because thin wall injection molding usually uses high-pressure rapid filling technology, so the impact of the material on the surface of the mold will be particularly strong. Therefore, high hardness requirements are required for the steel, and heat treatment is required for the material to effectively prevent mold wear, reduce maintenance costs, and improve cost-effectiveness.
The polishing of the mold surface is also very important. Try to polish the areas that can be polished to a certain extent, which can reduce flow resistance and prevent significant friction during plastic filling. Secondly, the exhaust of the mold also plays a very important role. As mentioned earlier, exhaust plates can be designed in the product structure, and negative pressure valves inside the mold can be used to pre-vacuum the mold and then fill it, which can reduce the resistance of air compression.
The exhaust system at the end needs to be designed according to different materials, which can effectively exhaust without running burrs. At the same time, it should be noted that all exhaust channels need to be led to the outside of the mold.
In the design of the gate, it is necessary to consider using large or multiple gates for glue injection, and even consider using needle valve timing control to effectively fill the material. At the same time, it is important to note that the cooling time of the thin-walled wall is very fast, and the thickness of the runner and gate needs to be appropriately increased to prevent cooling sealing.
- The Thin Wall Injection Molding Process Should Control Pressure and Speed
The filling time of thin wall injection molding is very short, with many filling times less than 0.5 seconds. In such a short time, it is impossible to follow the speed curve or cut off the pressure. Therefore, high-resolution microprocessors must be used to control the injection molding machine; During the entire injection molding process of thin-walled products, pressure and speed should be independently controlled simultaneously. The method of transitioning from pressure control to pressure control during the holding stage is no longer applicable to the speed-controlled filling stage of conventional injection molding machines.
Injection Molding Related Content
Applied’s expertise in modifying materials at atomic levels and on an ihdustrial scaleenables our customers to transform possibilities into reality.