Home > TPU Injection Molding Custom Process
TPU Injection Molding Custom Process
TPU Injection Molding
Details
Details:
Model
Material
Brand
Origin
Application
Booling-Injection-13
P20, 718, S136, 2738 etc
Booling
China
Automotive parts, industrial parts, medical parts, household
TPU injection molding material has high elasticity and mechanical strength, and its wear resistance and good processing performance make it suitable for customized production of injection molded parts.
Advantages of TPU Injection Molding:
- Wear Resistant
- Chemical Resistance
- High Strength
- Hydrolysis Resistance
- Fungus Resistant
Related Hot Products
There are many ways to shape TPU plastic, among which plastic injection molding is the most widely used, which can process TPU into the required functional parts. This process involves the preparation of raw materials → design of injection molding machines and molds → injection molding → cooling and demolding → post-processing of the parts.
Design of TPU Injection Molding Machine
When TPU injection molding, due to the special nature of materials and molding methods, manufacturers need to focus on the selection and design of injection molding machines.
The TPU injection machine barrel is lined with copper aluminum alloy and the screw is chrome plated, which can prevent wear to a certain extent. The optimal length-to-diameter ratio (L/D) of the screw is around 16-20, with at least 15 maintained; A compression ratio of 2.5/1 to 3.0/1 is most suitable for parts. Compression section 0.3L, feeding section 0.5L, measuring section 0.2L. Manufacturers should install check rings near the top of the screw to prevent backflow of injection material and maintain maximum pressure within a suitable range, thereby accelerating efficiency.
When injection molding TPU, it is advisable to use a self-flowing nozzle, and the outlet can be designed in a conical shape. In addition, the nozzle should be equipped with a controllable heating belt to prevent material solidification. The nozzle diameter can be kept above 4mm, which is 0.68mm smaller than the inlet of the main channel collar.
In addition, from the perspective of economy and cost-effectiveness, manufacturers should set the injection volume at 40% to 80% of the rated amount. The screw speed is maintained at 20-50r/min.
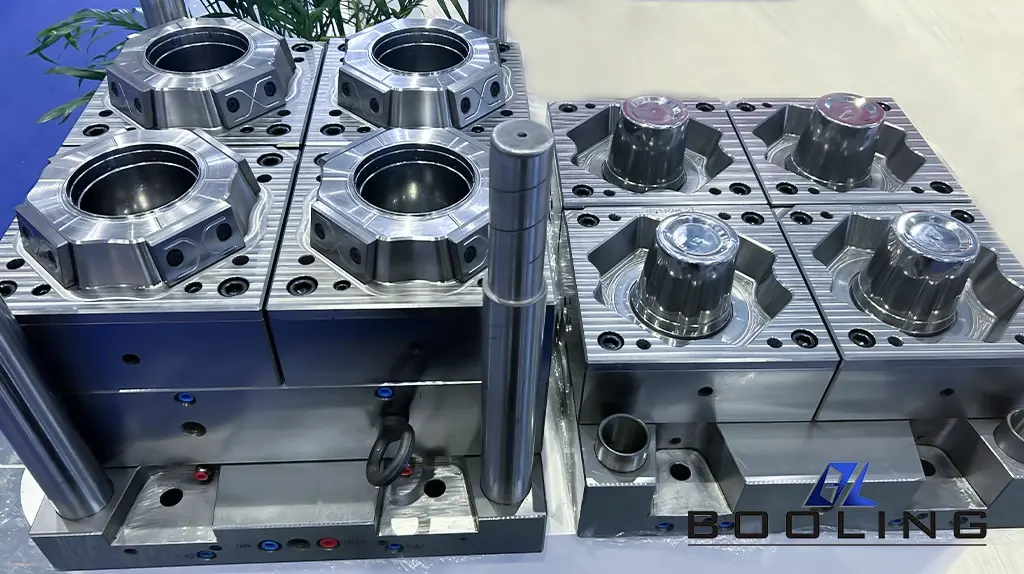
Design of TPU Injection Mold
The mold design for TPU injection molding should take into account the requirements of product shape, size, and accuracy:
- Shrinkage Rate of TPU injection Molded Parts
The shrinkage rate during TPU injection molding has a significant impact on the product, which is mainly influenced by molding conditions such as the thickness, shape, hardness of raw materials, mold temperature, and molding temperature of the product. The usual range of shrinkage is 0.005~0.020cm/cm. 2. Flow channels and cold material cavities of TPU injection molds
The main channel of the mold is a section of passage that connects the injection machine nozzle to the diversion channel or cavity, and the diameter should be enlarged inward to facilitate the demolding of the main channel material. The diversion channel of the mold is the channel that connects various cavities and the main channel in the multi-cavity mold and should be symmetrically and equally distributed and arranged on the mold.
In addition, the flow channel can be semi-circular, circular, rectangular, etc., with a diameter of about 6-9mm. Generally speaking, the surface of the flow channel must be polished like a mold cavity to reduce flow resistance, provide faster filling speed, improve injection efficiency, and shorten molding time. In addition, the TPU material used for injection molding has a high viscosity, and the product generally adopts fine patterns for easy demolding.
The cold material hole is a cavity located at the end of the main flow channel, which can collect the cold material generated between two injections at the nozzle end, achieving the purpose of preventing blockage of the diversion channel or gate, so that there is no need to specially clean and waste processing time. Once cold material is mixed into the mold cavity, the product is very prone to internal stress, leading to defects. The diameter of the cold material hole is approximately 8-10mm and the depth is about 6mm.
2.Gate and Exhaust Port of TPU Injection Mold
The gate of the TPU injection mold is a channel that connects the main or branch channel with the mold cavity. Its cross-sectional area is usually smaller than that of the flow channel, and its length is preferably shorter, making it the smallest part of the flow channel system. The shape of the sprue is mostly rectangular or circular. The thicker the product, the larger the size of the sprue, and vice versa, the smaller it is. If the thickness of the product is less than 4mm, the gate diameter is 1mm; Thickness is 4-8mm, and the diameter is 1.4mm; If the thickness is above 8mm, the gate diameter can reach 2.0-2.7mm. Generally, the gate position of the mold is selected at the thickest part of the TPU injection molded product that does not affect its appearance and use, forming a right angle with the mold wall to prevent shrinkage, avoid defects such as spiral patterns, and improve the yield rate.
The exhaust port of the mold is a groove-shaped outlet opened by the manufacturer in TPU injection molds, which can completely exhaust the gas in the mold cavity and prevent the molten material entering the mold from being sucked into the gas. If the exhaust hole is not operated properly, it can lead to poor fusion of the product, porosity, or even insufficient filling of the mold, resulting in shrinkage, and even more serious consequences, such as burning the product due to high temperature caused by air compression, and internal stress in the product. The position of the exhaust port can be chosen as the end of the molten material flow in the mold cavity or on the parting surface of the mold, with a groove approximately 0.015mm deep and 3-6mm wide. In the manufacturing process of injection molding, manufacturers must control the temperature to maintain uniformity as much as possible to avoid defects such as warping and twisting of TPU injection molded parts.
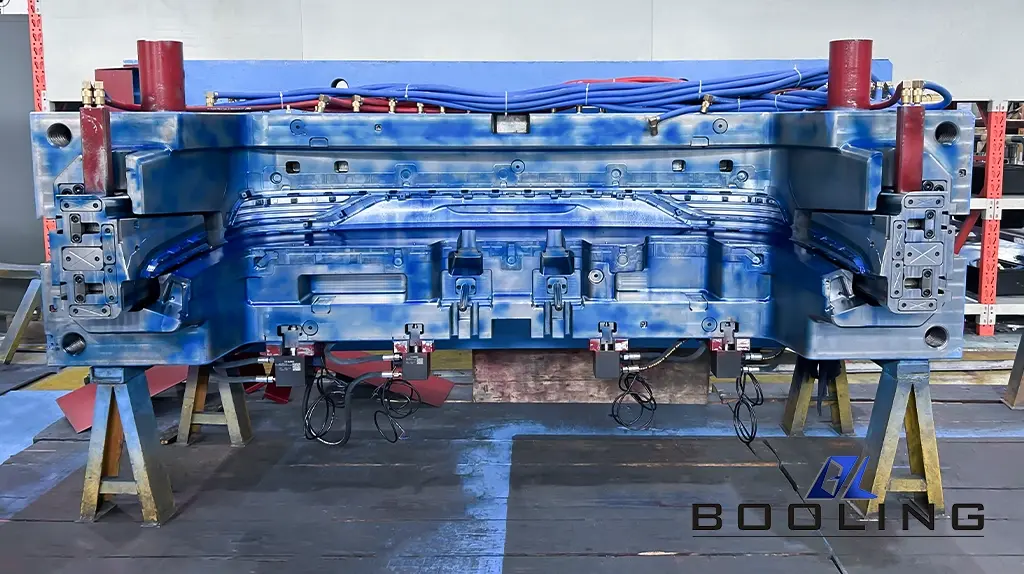
Parameter Adjustment and Control of TPU Injection Molding
During the TPU injection molding process, manufacturers need to pay attention to monitoring, adjusting, and controlling some parameters, such as injection temperature, speed, pressure, and time.
-Temperature
The temperature that needs to be controlled during the TPU injection molding process includes the barrel temperature, mold temperature, and nozzle temperature. The temperature of the barrel and nozzle mainly affects the plasticization and flow of TPU, while the temperature of the mold affects the flow and cooling of TPU.
- Barrel Temperature
The choice of barrel temperature depends on the hardness of the TPU injection molding material. TPU with high hardness has a high melting temperature and long melting time, and the highest temperature at the end of the barrel is also high. The temperature range of the material used for processing TPU is approximately between 177~232 ℃, depending on the produced parts. The temperature distribution of the material barrel generally gradually increases from one side of the hopper (rear end) to the nozzle (front end), to make the temperature of TPU material rise steadily and make the melting and plasticizing process more uniform.
- Mold Temperature
The influence of mold temperature on the intrinsic properties and surface quality of TPU products is crucial. The influencing factors of mold temperature mainly include the crystallinity of TPU and the size of the product.
Manufacturers usually control the mold temperature through constant temperature cooling media such as tap water. TPU materials have high crystallinity and hardness, and the mold temperature should also be correspondingly increased. Low mold temperature can lead to insufficient heating time of the melt, premature freezing, and the formation of flow patterns, which is not conducive to the growth of spherulites and reduces the crystallinity of the product. This can result in later crystallization processes, causing post-shrinkage and changes in the performance of the product, leading to a decrease in appearance and usability. So the mold temperature for TPU injection molded products is generally maintained between 10 and 60 ℃.
- Nozzle Temperature
The nozzle temperature is usually set slightly lower than the maximum temperature of the barrel to prevent the possibility of molten material splashing in the straight-through nozzle. But if the casting phenomenon occurs or is more severe, a self-locking nozzle can be used, and the nozzle temperature can also be controlled within the highest temperature range of the material barrel.
-Injection Speed
The setting of injection speed is mainly determined by the specific shape and performance of TPU products. Products with thick-end faces require lower injection speeds, while products with thin-end faces require faster injection speeds. The manufacturer’s control over injection speed determines the quality and dimensional accuracy of the final product.
-Screw Speed
When processing TPU injection molded products, manufacturers usually provide lower shear rates, which means lower screw speeds need to be set. Processing TPU injection molded products usually requires low shear rates, so it is advisable to use lower screw speeds. The screw speed of TPU is generally 20~80r/min. If the actual situation allows, it is preferred to use 20~40r/min.
-Pressure
The pressure during TPU injection molding mainly includes plasticizing pressure (also known as back pressure) and injection pressure. The so-called back pressure refers to the pressure exerted on the molten material at the top of the screw when it retreats, and the magnitude of this pressure can be adjusted through an overflow valve. Increasing back pressure will reduce plasticizing speed, increase melt temperature, make the mixture of melt temperature and pigment more uniform, and discharge melt gas, but this approach will also prolong the injection molding cycle. In general, the back pressure of TPU is usually around 0.3-4MPa.
The injection pressure is the pressure applied by the top of the screw to the TPU material. The main function of this pressure is to reduce or overcome the flow resistance of TPU from the barrel to the mold cavity, increase the rate of molten material filling, and compact the molten material.
The flow resistance and filling rate of TPU are closely related to the viscosity of the melt, and the viscosity of the melt is directly related to the hardness and temperature of TPU, that is, the viscosity of the melt is not only determined by the temperature and pressure of injection molding, but also by the hardness and deformation rate of TPU material. The higher the shear rate, the lower the viscosity and the stronger the fluidity; The higher the hardness and viscosity of TPU injection molding material, the higher the shear rate remains unchanged.
Under the condition of constant shear rate, viscosity will decrease with increasing temperature, but at higher shear rates, viscosity is not as affected by temperature as at lower shear rates. Manufacturers generally set the injection pressure of TPU at around 20-110MPa. The holding pressure is about half of the injection pressure, and the back pressure should be below 1.4 MPa. This parameter-setting method can make the plasticization of TPU material more uniform and produce higher-quality injection molded products.
-Time
The time required to complete an injection molding process (from plastic plasticization to part ejection) is called the molding cycle. The injection molding cycle of TPU includes filling time, holding time, cooling time, and other times (opening, demolding, closing, etc.), which directly affect labor productivity and equipment utilization. The molding cycle of TPU is usually determined by the hardness of the material, the thickness of the workpiece, and the design of the shape. If TPU has high hardness and a short cycle, the thickness of the plastic part will be long, and the configuration of the plastic part will be complex and long. In addition, the injection molding cycle of TPU is also related to the mold temperature, generally between 20~60 seconds, and the specific time needs to be determined by considering various factors.
Related News
Applied’s expertise in modifying materials at atomic levels and on an ihdustrial scaleenables our customers to transform possibilities into reality.