Home > Principle of Liquid Silicone Material for Injection Molding
Principle of Liquid Silicone Material for Injection Molding
Liquid Silicone Injection Molding
Details
Details:
Model
Material
Brand
Origin
Application
Booling-Injection-8
P20, 718, S136, 2738 etc
Booling
China
Automotive parts, industrial parts, medical parts, household
Liquid silicone injection molding is a special process that is different from plastic materials. Liquid silicone injection molding has environmentally friendly characteristics and can be widely used in fields such as medical devices and baby products.
Advantages of Liquid Silicone Injection Molding:
- Excellent Elongation
- High Tensile Strength
- Strong Liquidity
- Strong Stability
- High Elasticit
Related Hot Products
Liquid silicone injection molding technology uses high pressure to inject liquid silicone into the mold and solidifies it by heating it to form the desired product. Liquid silicone injection molding products have the advantages of being non-toxic, heat-resistant, and highly resilient, making them a flexible solid material with high toughness. This molding technology has a wide range of applications, including automobile manufacturing, medical devices, daily necessities, etc.
Classification of Liquid Silicone Injection Molding Raw Materials
In the liquid silicone injection molding process, liquid silicone is mainly divided into low viscosity and high viscosity, including:
Low-viscosity Liquid Silicone
Low-viscosity liquid silicone refers to a type of material with a viscosity generally below 30000CPS and good self-leveling properties. This low-viscosity liquid silicone can flow and level itself under its gravity, which is a characteristic of silicone materials in a liquid state. When using this type of silicone to make molds, manufacturers usually use it for mold filling or brushing, which is mostly done manually. The most commonly used silicone for making molds is condensation-type industrial-grade mold silicone. In addition, an environmentally friendly liquid silicone gel can also be used for addition molding, but this material is generally used to make silicone products, etc. This silicone gel is prepared in a one-to-one ratio, and the processing process is not complicated. It is very suitable for using a fully automatic filling machine for filling operations, greatly improving production efficiency and saving labor costs.
High-viscosity Liquid Silicone Gel
High-viscosity silicone refers to the silicone used in injection molding or injection molding processes. The viscosity of this type of silicone is mostly above 100000 CPS and cannot automatically level, resulting in a paste-like appearance. Most manufacturers choose this type of silicone for liquid silicone injection molding. These types of silicone molded parts mainly include silicone pacifiers, silicone phone cases, silicone button products, etc.
Silicone for high-viscosity liquid injection molding cannot be formed manually and requires the use of large silicone injection machines. Compared to low-viscosity liquid silicone, its molding is more complicated. In the production process of liquid silicone injection molding, there are two pipes inside the AB glue barrel. Under the action of high-pressure suction, the AB glue is sucked into the pipes and then mixed and injected or extruded into the high-temperature metal mold at high speed. Under the heating of high-temperature metal molds, liquid silicone will quickly solidify into a solid and become silicone injection molded parts.
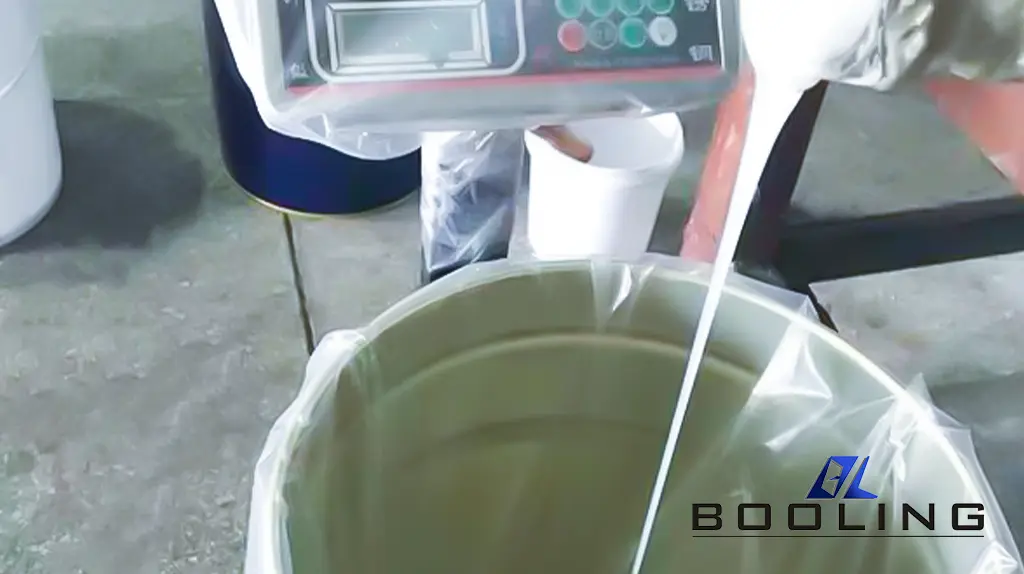
The Process of Liquid Silicone Injection Molding
The process of liquid silicone injection molding mainly includes the production of molds, selection of materials, selection of injection equipment and processes, and final quality control, including:
- Mold Making
Mold-making is a key step in liquid silicone injection molding. Manufacturers not only need to ensure the high precision of the mold during the design and production process but also consider whether it has a short production cycle and a long service life. In addition, an excellent mold needs to have high thermal conductivity, degradability, oxidation resistance, adhesion, and other characteristics. Its structure, shape, size, and production cycle time of the final product also need to meet the requirements of the product.
- Selection of Silicone Material
In the liquid silicone injection molding process, the selection of silicone material must meet the performance requirements of the final product. The silicone material used needs to have characteristics such as high-temperature resistance, good elasticity, chemical stability, and high precision. Different silicone materials can be suitable for different product requirements, and a variety of colors, transparency, hardness, and other options are available.
- Selection of Injection Molding Machines and Processes
Liquid silicone injection molding requires the use of more precise injection molding machines than conventional processing, and manufacturers generally use vertical injection molding machines for silicone molding. Due to the high fluidity and low viscosity of silicone materials, they can be rapidly injected under specific processing conditions. Manufacturers can inject silicone material into the mold, form an initial shape according to the shape of the cavity, and then enter the baking and cooling hardening process to obtain the final target product.
- Quality Control
Whether in the process of liquid silicone injection molding or product consistency inspection, manufacturers need to conduct strict quality control to improve the consistency, qualification rate, and stability of the final product. The quality control of the entire process includes quality inspection of raw materials, appearance quality inspection of final products, size and hardness testing, and other links. At the same time, manufacturers also need to conduct performance tests on finished products, such as heat resistance, chemical resistance, oil resistance, and tensile and compression resistance, to ensure that the quality of the products meets the requirements.
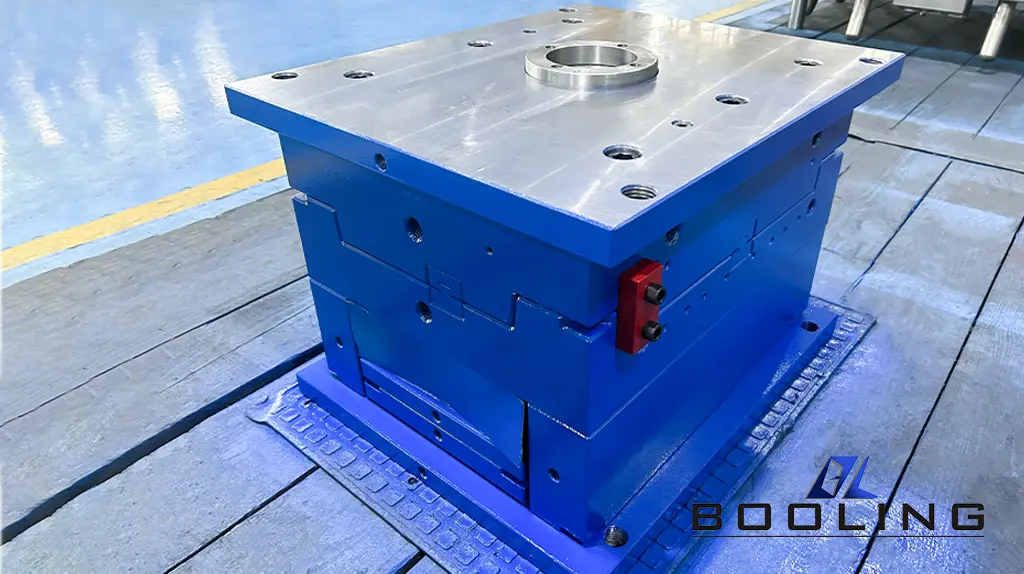
Maintenance of Liquid Silicone Injection Molding Equipment
Liquid silicone injection molding equipment requires regular maintenance and upkeep to maintain its optimal performance.
- Before using the new liquid silicone injection molding equipment, manufacturers need to check whether the cooling water is sufficient and whether it can flow smoothly. This step is to prevent damage to the silicone injection molding equipment due to insufficient cooling water, which increases processing costs. In addition, manufacturers should keep the working environment of the mold temperature machine clean, and avoid excessive dust and blockage of equipment pipelines and other components, which can greatly extend the service life of the electrical components of the mold temperature machine and increase its durability.
- When maintaining liquid silicone injection molding equipment, attention should be paid to the operating environment of the equipment. Due to the high cost of injection molding equipment and the high density of precision electronic components in control parts, manufacturers should strive to ensure a sufficiently clean working environment to avoid excessive dust-blocking precision parts. This can extend the service life of electrical components in the equipment to a certain extent and reduce the occurrence of failures. Especially for injection molding equipment that has been in dusty areas for a long time, regular maintenance must be carried out, such as blowing off dust with an air gun after power failure. In addition, wet towels should not be used for wiping to prevent endangering personal safety.
- The mold temperature machine of liquid silicone injection molding equipment is divided into two types: water type and oil type, and the maintenance methods of different equipment are also different. The main purpose of maintaining an oil-type mold temperature machine is to prevent oil leakage or carbon buildup in the heat transfer oil. For products with processing temperatures above 200 degrees Celsius, the thermal oil needs to be replaced regularly, with a cycle of approximately 1-2 months; For processing below 200 ℃, the thermal oil also needs to be replaced every 3 months. This method is mainly used to improve the heating efficiency of silicone injection molding machines, and on the other hand, to extend the life of the equipment’s heating tube. If it is a water-based mold warmer, a clean water source should be used to prevent scaling. In addition, manufacturers need to regularly inspect equipment filters and other parts for blockages, and if so, promptly clean them.
- During the operation of liquid silicone injection molding equipment, if the pressure of the equipment is unstable, the manufacturer should promptly stop the heating mode of the mold temperature machine to prevent damage to the heating tube. If the pressure of the equipment is too high, the manufacturer should consider whether there is a situation where the valve is not opened or the pipeline is blocked, and should not blindly continue heating. To protect the circulating pump of the equipment, it is necessary to turn off the circulating pump only when the temperature of the equipment drops below 80 ℃.
- In terms of pipelines, manufacturers can determine whether there is a blockage in the pipeline based on the relationship between the pump and pressure. If the pressure is too low, the heating tube can be removed and cleaned with tools, especially the filter mesh cover at the system inlet, which needs to be cleaned regularly; Clean at least once a month.
- Regularly inspect the pump of the mold temperature machine for oil or water leakage, and determine whether the pump shaft seal needs to be replaced regularly based on the actual situation.
- Manufacturers can replace electronic components promptly based on their service life and conduct regular testing to ensure safety and sustainable production.
Related News
Applied’s expertise in modifying materials at atomic levels and on an ihdustrial scaleenables our customers to transform possibilities into reality.