Home > Polycarbonate Injection Molding
Details
Details:
Model
Material
Brand
Origin
Application
Booling-Injection Mold-1
P20, 718, S136, 2738 etc
Booling
China
Home Appliance parts
Polycarbonate injection molding uses mold processing, which makes the application of materials and processes more flexible, and realizes the processing of products with good color and appearance, meeting the needs of dimensional accuracy and quality, and realizing the rapid delivery of polycarbonate injection molding for manufacturers in industries such as industry, medical, automobile, and packaging.
Advantages of polycarbonate injection molding:
- Achieve processing of high-transparency products
- Fast production speed
- High product precision
- Rapid production with the help of molds
Related Hot Products
Polycarbonate injection molding involves multiple stages of material processing, including preheating, injection, pressure holding, cooling, and demolding. The materials used have good transparency, impact resistance, and adaptability to extreme temperatures. The products produced can withstand steam, detergents, and thermal sterilization operations, and are used in industries such as medical and food packaging.
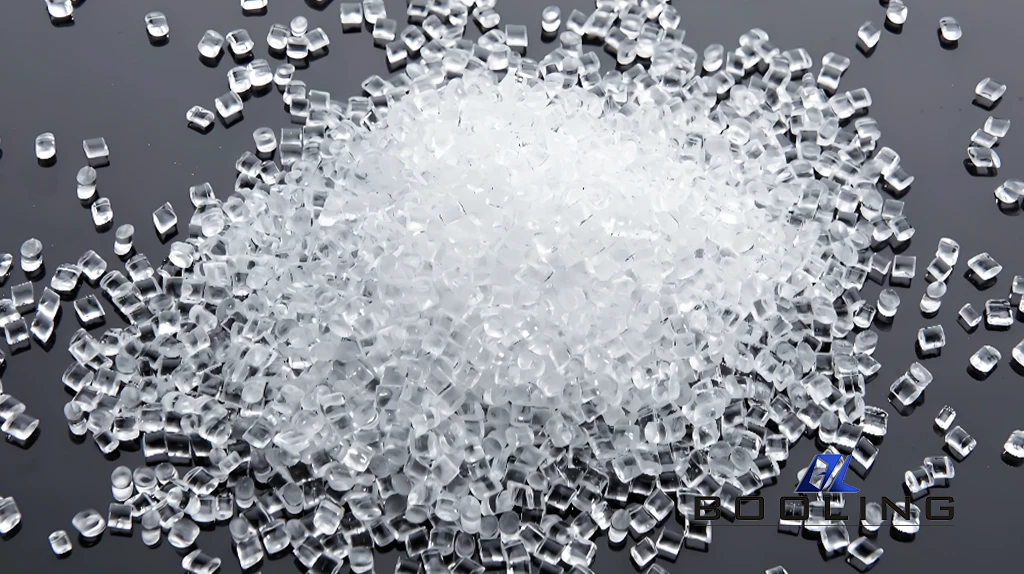
Characteristics of Polycarbonate Injection Molding Materials
Before manufacturers carry out polycarbonate injection molding, they need to fully understand the material’s characteristics and processing advantages to optimize the processing parameters.
– Characteristics
Polycarbonate (PC) is a high-molecular-weight polymer that can be divided into aromatic, aliphatic, aliphatic-aromatic, and other types according to the ester structure.
– Advantages
Polycarbonate has high transparency, impact strength, hardness, and elastic modulus, and can maintain good stability at extreme temperatures; it has excellent fatigue resistance, weather resistance, and electrical properties; it has low molding shrinkage and strong dimensional stability during processing and molding.
– Applications
The three major application areas of polycarbonate (PC) injection molding are the automotive industry, electronics, glass assembly industry, and electrical industry. In addition, it is also widely used in packaging and other office equipment, industrial machinery parts, optical disks, computers, film, health care, leisure and protective products and other fields.
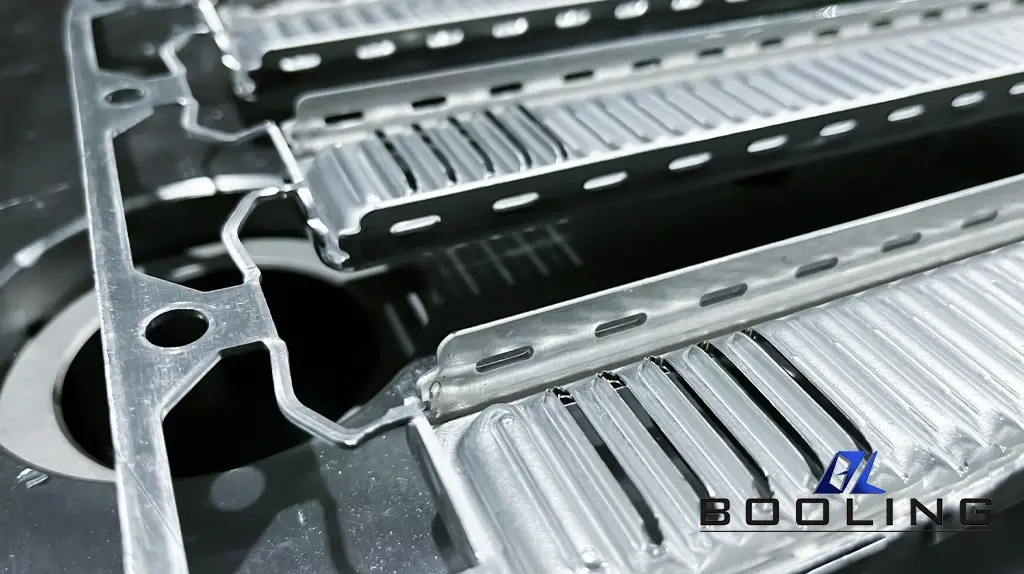
Requirements for Polycarbonate Injection Molding
During the polycarbonate injection molding process, manufacturers need to set parameters strictly according to the molding requirements and optimize the processing technology.
-Molding requirements:
- Polycarbonate materials are affected by high temperatures, and the possibility of absorbing moisture in the air will increase. Manufacturers need to store them in a dry place and dry them before use. The temperature is generally kept between 110-120℃.
- During the polycarbonate injection molding process, setting the mold temperature too low can easily lead to stress concentration and cracking defects in the product; setting the mold temperature too high can cause carbonization of the material and loss of processing performance. In general, the mold temperature during the molding of polycarbonate materials should be kept between 70 and 110℃.
- The injection speed of polycarbonate is affected by the gate size. A gate that is too small will cause resistance when injecting the molten material, resulting in a decrease in the injection speed. Appropriately increase the gate size, increase the injection speed, and reduce the shear effect.
- During the polycarbonate injection molding process, to fill the mold cavity as quickly as possible, the manufacturer will set an injection pressure as high as possible to reduce the shrinkage and dimensional deviation of the product.
-Injection molding machine requirements:
Injection volume: preferably about 40%~60% of the injection molding machine capacity
Clamping force: 0.47-0.78t per square centimeter of finished product projection area (or 3-5t per square hour)
Screw: minimum length is 15 times the diameter, the best L/D is 20:1, and the compression ratio is 1.5:1~3.0:1. The specific settings are selected according to the actual processing conditions of the manufacturer.
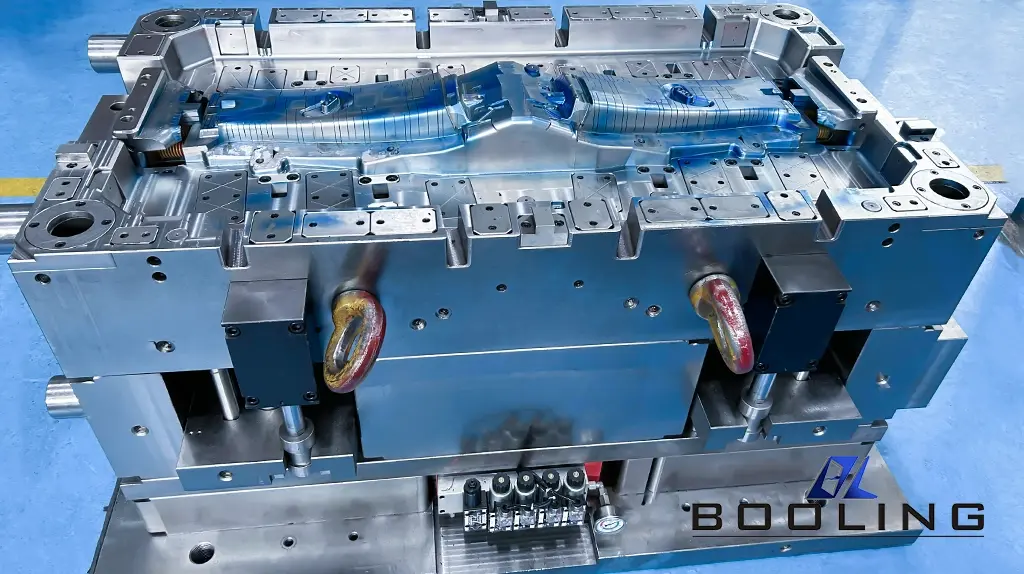
Quality Control of Polycarbonate Injection Molding
Various defects will occur during the polycarbonate injection molding process, and manufacturers optimize the quality by proposing corresponding solutions.
-Causes
The design of the mold is relatively diverse, the specific processing equipment and processing technology are also different, and the experience and familiarity of the processing personnel are also different.
-Common defects and solutions
- Bubbles appear on the surface of the product, which may be due to excessive water content in the polycarbonate raw material, improper injection temperature, and mold exhaust settings. Manufacturers can improve it by re-drying the raw material, lowering the injection temperature, and other solutions.
- The product is deformed, which may be due to product shrinkage. Manufacturers can adjust the holding pressure appropriately to compensate for the shrinkage of the product.
- Uneven cooling of the product during the molding process or excessive injection pressure may cause stress inside the product. Manufacturers can adjust it by optimizing the cooling system of the mold and reducing the injection pressure and holding pressure.
Automotive Mold Related Content
Applied’s expertise in modifying materials at atomic levels and on an ihdustrial scaleenables our customers to transform possibilities into reality.