Home > Injection Molding > Plastic Injection Molding
Booling plastic injection molding uses advanced production equipment including injection molding machines, dryers, feeders, mixers, and molds. It uses injection molding technology to inject the molten plasticized material into the mold cavity and core through the screw of the injection molding machine. After the pressure-holding cooling process, customized plastic parts are obtained. Booling engineers have rich experience in 2D design, 3D design, CNC programming, and CNC machining and manufacturing, and have helped manufacturers in Germany, Russia, Turkey, Argentina, Canada, and other countries to achieve customized processing and fast delivery of plastic products.
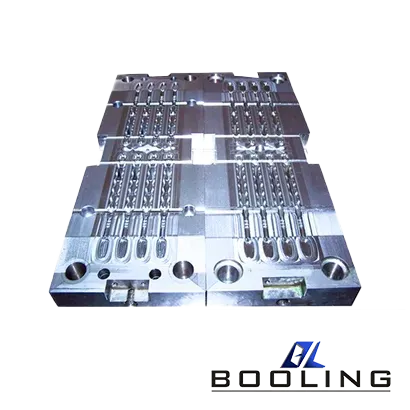
Plastic injection molding has extremely high requirements on the precision and corrosion resistance of the mold, which is usually processed using hardened steel or aluminum alloy to achieve the required number of injections.
- Single Cavity
- Multi-Cavity
- Hot Runner
- Cold Runner
- Two-Plate
- Three-Plate
Plastic Injection Molding Capabilities
Injection molding technology has brought cost-effectiveness to the field of plastic processing and can achieve mass production of products with a high pass rate.
·
US
Metric
ABS
59 in. x 51.2 in. x 17.7 in.
1500mm x 1300mm x 450mm
PE
59 in. x 51.2 in. x 17.7 in.
1500mm x 1300mm x 450mm
PP
59 in. x 51.2 in. x 17.7 in.
1500mm x 1300mm x 450mm
PS
59 in. x 51.2 in. x 17.7 in.
1500mm x 1300mm x 450mm
*Plastic injection molding provides extensive material choices, tight tolerances, complex part geometry, high production rates, value-added operations.
Plastic Injection Molding Material
Booling provides plastic injection molding material selection recommendations based on the product’s application scenario, final performance, and structural size.
Plastic Injection Molding Material Selection:
Material
- ABS
- PE
- PP
- PS
- NYLON
- EVA
- Thermoplastic
- PMMA
- Silicone
- Rubber
- LSR
- TPU
- TPV
- TPE
The Advantage of Plastic Injection Molding
Plastic injection molding requires a large initial investment, but the mold can achieve mass production of products and has a long-term return on investment.
- It can achieve mass production of products with multiple materials at a lower cost, and the parts are consistent and high-quality
- Plastic materials can achieve complex shapes and designs through injection molding
- Injection molding can produce parts with stable quality and high dimensional accuracy at a very fast speed
- Using thermoplastics, processing waste can be recycled to reduce material waste
- Booling can directly design the surface texture or logo design directly in the mold cavity, reducing subsequent processing steps
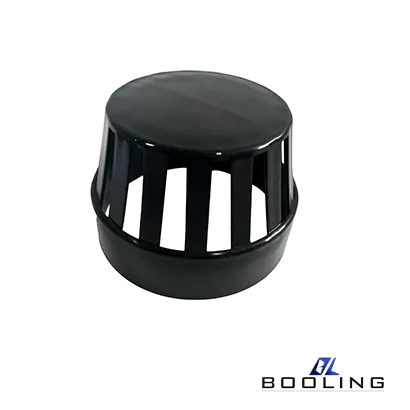
Application of Plastic Injection Molding
Plastic injection molding technology can produce products with complex structures and details, such as automobiles, consumer goods, medical devices, and electronics.
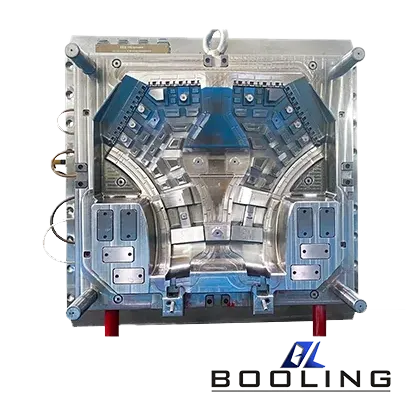
Guidelines for Plastic Injection Molding
A plastic injection mold is a valuable tool and asset in the injection molding manufacturing process.
The mold is a key tool in plastic injection molding technology. It is usually made of hardened steel and aluminum alloy, with a long service life and corrosion resistance.
Plastic injection molding is the most common method for mass production of plastic products, covering simple daily necessities such as bottle caps and toys and more complex products such as automobiles, aerospace, and medical. It can create more complex shapes and achieve integrated molding. Booling designers will conduct mold flow analysis and provide a feasibility analysis report before production.
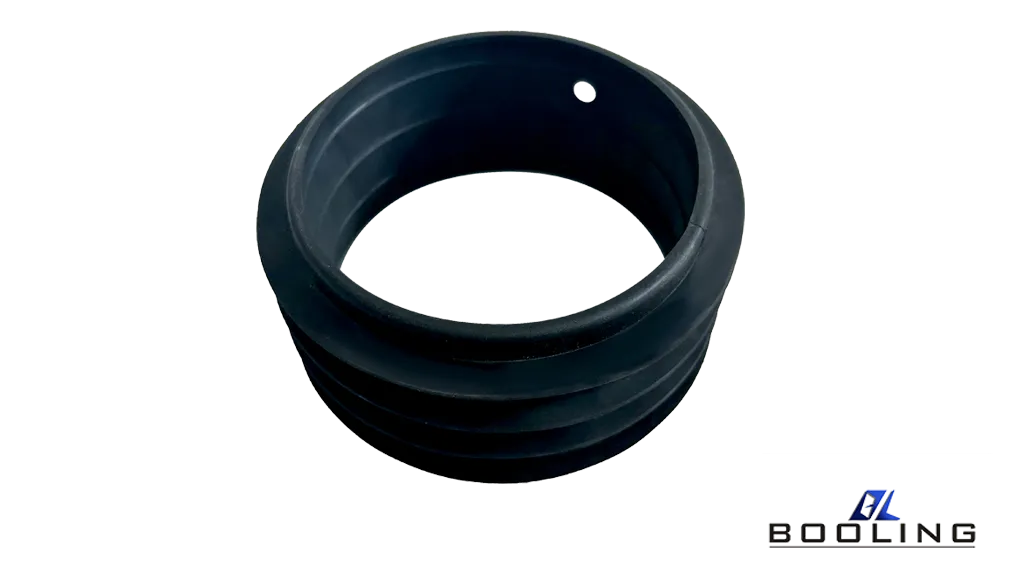
Principle of Plastic Injection Molding
Plastic injection molding is a technology that injects molten plastic into the mold cavity for molding, with a high degree of automation and versatility.
Plastics are fed into the barrel in the form of granules or powders. The plastics are processed into a molten state under the action of high temperature and pressure and are pressed into the cavity by a reciprocating screw or syringe. During the filling process, when the cavity is about to be filled, the screw movement quickly changes from flow rate control to pressure control. At this time, it is necessary to properly adjust the back pressure of the screw to compact the melt in the barrel, increase density and avoid surface defects such as bubbles.
After the plastic fills the cavity, it is cooled and solidified. The injection mold is equipped with a circulating water cooling channel to speed up the cooling speed. After the plastic part solidifies, the mold is opened and the part is ejected.
Plastic injection molding is a continuous and repetitive process that can achieve the production of large quantities of plastic parts.
Plastic Injection Molding Process Types
Booling provides single-cavity, multi-cavity, hot runner, insert, over-molding, and other types of injection molds to meet the needs of different products and application scenarios.
- Single Cavity
Single-cavity injection mold is the most basic mold type, producing one plastic part in one cycle, suitable for the production of small batches of products
- Multi-cavity Mold
There are two or more cavities in a mold. The injection molding machine can produce multiple plastic parts in one cycle, realizing precision manufacturing of large-scale products
- Insert Mold
Place prefabricated metal inserts or screws in the mold, and then inject molten material to connect with the insert to improve the overall strength and durability of the product. Insert mold avoids secondary composition and saves time and cost
- Overmolding Mold
Plastic material is injected onto another preformed substrate to reduce assembly costs and improve the overall performance of the product.