Home > Injection Molding > Rubber Injection Molding
Rubber injection molding uses an injection molding machine and a mold to heat the uncured rubber material under the action of screw shear force and friction, and then injects it into the mold cavity under high pressure, filling every corner of the mold, and forms a product after cooling and curing. Booling engineers have provided high-quality rapid prototyping delivery of rubber injection molding molds to manufacturers in Canada, Russia, Brazil, Argentina, South Africa, and other countries.
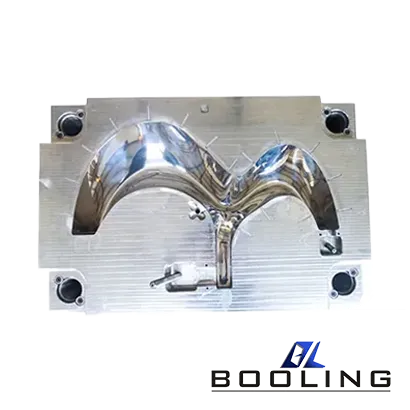
Rubber injection molding takes advantage of the easy-to-form characteristics of rubber, ensuring accurate molding dimensions and uniform quality, and meeting strict industrial processing requirements.
- Rated injection volume
- Rated injection pressure
- Rated locking force
- Mold installation dimensions
- Mold opening stroke
Rubber Injection Molding Capabilities
Rubber has good injection molding capabilities and can be customized according to user needs, turning two-dimensional designs into three-dimensional objects.
·
US
Metric
Rubber
59 in. x 51.2 in. x 17.7 in.
1500mm x 1300mm x 450mm
*Rubber injection molding provides strict tolerances and perfect part reproduction ability.
Rubber Injection Molding Material
Booling offers natural and synthetic rubber materials as well as some thermoplastic elastomers with selectivity.
Material
- Rubber
The Advantage & Disadvantage of Rubber Injection Molding
- Rubber injection molding is an automated and efficient process
- Excellent processing accuracy, ensuring consistent parts
- Good at creating complex geometric shapes
- Less waste generated during processing, saving resources
- Economical, achieving large-volume parts processing in a short time
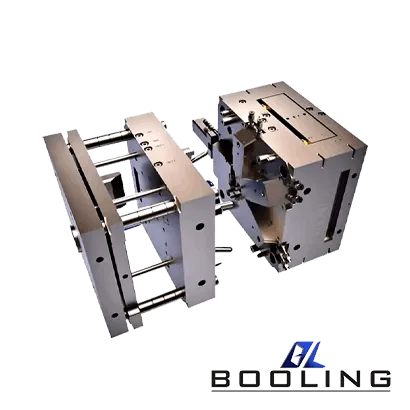
Application of Rubber Injection Molding
Rubber has a certain toughness and elasticity and is widely used in electronic products, medical devices, automobile manufacturing, industry, and other fields.
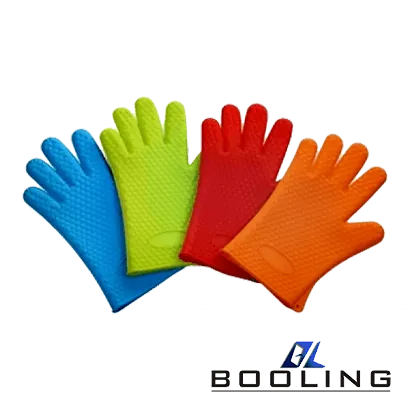
Guidelines for Rubber Injection Molding
Rubber injection molding is efficient and economical, meeting the market demand for high-quality rubber parts.
Rubber materials are elastic, anti-aging, and can withstand extreme temperatures. Combined with the injection molding process, they produce rubber parts with extraordinary dimensional accuracy and consistency. Booling took automated production into consideration when designing and processing molds, and was able to achieve more efficient production with the help of manipulators and robots.
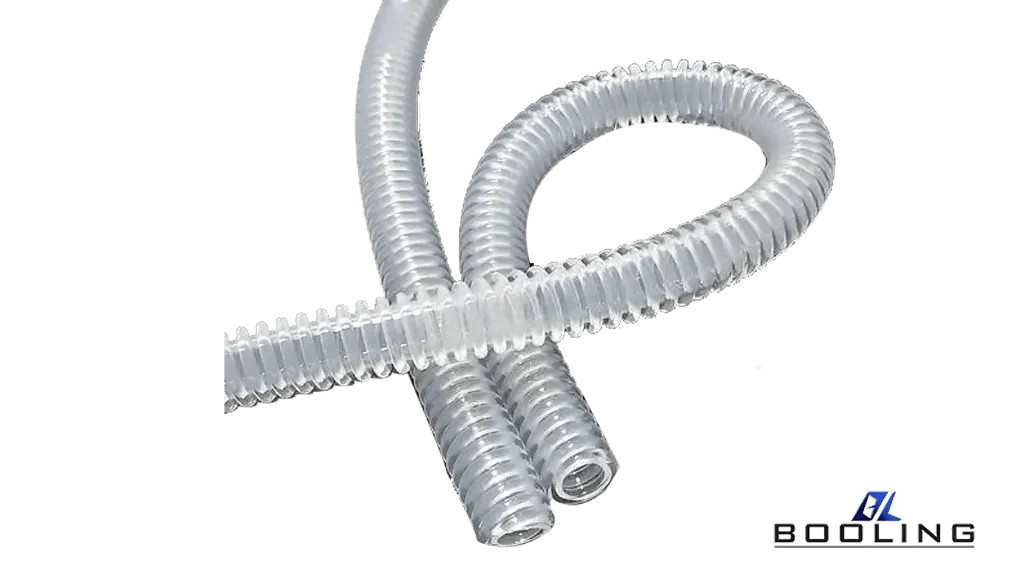
Rubber Injection Molding Material Selection
Rubber is the main component of injection molding, with high elasticity and good impact resistance. Booling provides natural rubber and synthetic rubber materials to meet different processing requirements.
- Natural rubber: Derived from the sap of rubber trees, it has excellent elasticity, resilience, and tear resistance. It is suitable for the processing of products that require high flexibility and durability, such as automobile tires, soles, seals, and gaskets.
- Synthetic rubber: Mainly includes nitrile rubber, propylene rubber, fluoro rubber, styrene-butadiene rubber, etc., which have the characteristics of wear resistance, oil resistance, and heat resistance, and can be used in the production of seals in precision fields. The synthetic rubber manufactured by Booling is carefully formulated and uses various additives and fillers to enhance its performance, and can produce customized rubber components.
Rubber Injection Molding Mold Precautions
Rubber injection molding is used to manufacture complex and precise rubber parts with high quality and high consistency. Booling has special precautions and troubleshooting solutions to ensure that rubber injection molding is always in optimal performance.
- Preventive maintenance can reduce downtime during processing and extend service life, including regular inspection, cleaning, and lubrication of mold components to prevent unexpected failures and ensure smooth operation and processing of molds.
- Balance various parameters in the injection molding process, such as temperature, pressure, and time. Engineers need to closely monitor and adjust these parameters to help achieve the best performance of the product and reduce the probability of defects.
- The mold is a key tool in the injection molding process. Booling pays attention to its maintenance and care, performs regular cleaning and polishing, checks the mold cavity, and prevents surface defects and short shots during processing.
- Properly store and pre-treat rubber materials to maintain the quality of the mixture, which is not affected by moisture and impurities and enters the injection molding process with extremely high quality.
- Combine automated processes with injection molding, and use manipulators and robots for automated picking and demolding. Booling has set up an automated detection and control system to monitor abnormal changes in parameters during processing, provide real-time data analysis, implement preventive maintenance, and ensure product quality and normal operation of equipment.
Rubber injection molding technology provides users with the best solution for manufacturing rubber parts. Its integrated functions can improve overall operational efficiency while simplifying the production process. The mass production capacity of rubber injection molding can meet the needs of customers and the market and achieve rapid product delivery.