Home > Double-Sided Integrated Pallet Mold Guide
Details
Details:
Model
Material
Brand
Origin
Application
Booling- Logistics Mold Mold-1
P20, 718, S136, 2738 etc
Booling
China
Logistics Mold parts
The double-sided integrated pallet mold belongs to large molds, currently mainly including 1200 * 1000mm, 1100*1100mm, 1300*1100mm, 1200*1200mm, 1400*1200mm, 1500*1200mm, 1500*1300mm, 1400*1400mm, 1600 * 1400mm, these models can meet users’ needs for different goods and load-bearing capacity, and is suitable for use in medical, fruit and vegetable, warehousing, logistics, factory and other environments. Booling’s engineers will also provide the most complete customized production solution for pallets based on your specific needs.
Advantages of double-sided integrated pallet mold processing
- High precision
- Free choice of blow molding and injection molding processes
- High efficiency
- The product has consistency
Related Hot Products
The double-sided integrated pallet mold is used for processing pallets with a consistent double-sided structure and the same function. This can achieve standardization of logistics and warehousing, save logistics and warehousing space, and achieve efficient transportation. Manufacturers can obtain higher-quality double-sided integrated pallets and products by continuously optimizing their processing and manufacturing processes.
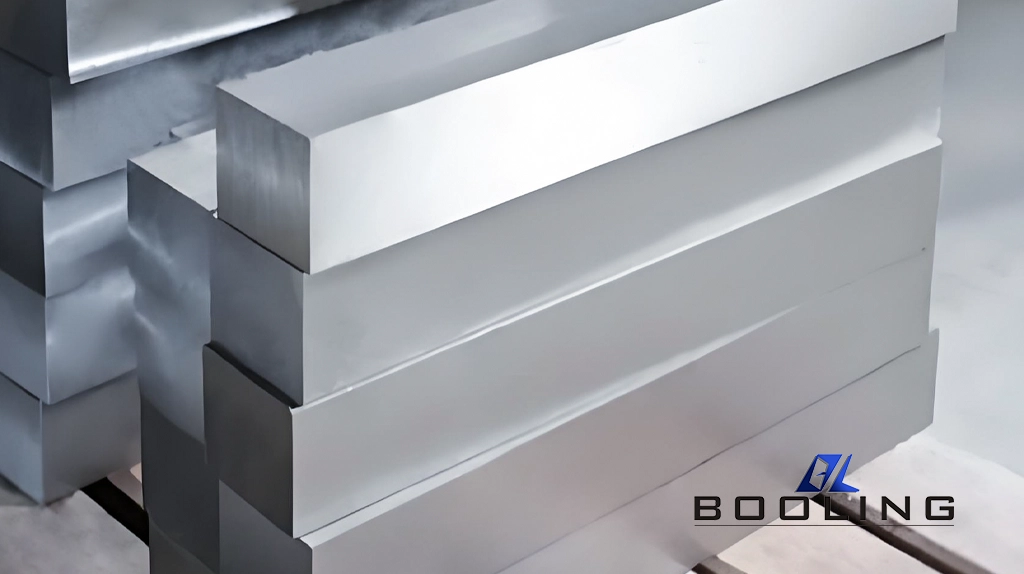
Material for Double-Sided Integrated Pallet Mold
The steel for the double-sided integrated pallet mold needs to be selected according to the production batch and production volume to ensure smooth mold processing during its service life.
P20: Has good processing performance, uniform hardness, and can maintain good accuracy and surface quality during cutting processes. Has good toughness and strength, and can withstand external forces such as high pressure and high temperature during injection molding.
718: It has high strength, hardness, and toughness, and can maintain deformation under long-term high temperature and high-pressure use, extending the service life of the mold. Has certain corrosion resistance to damp environments and plastics containing chemicals.
NAK80: It has high hardness and strength, excellent mirror polishing performance, and can achieve lower surface roughness after polishing treatment, resulting in products with higher surface quality.
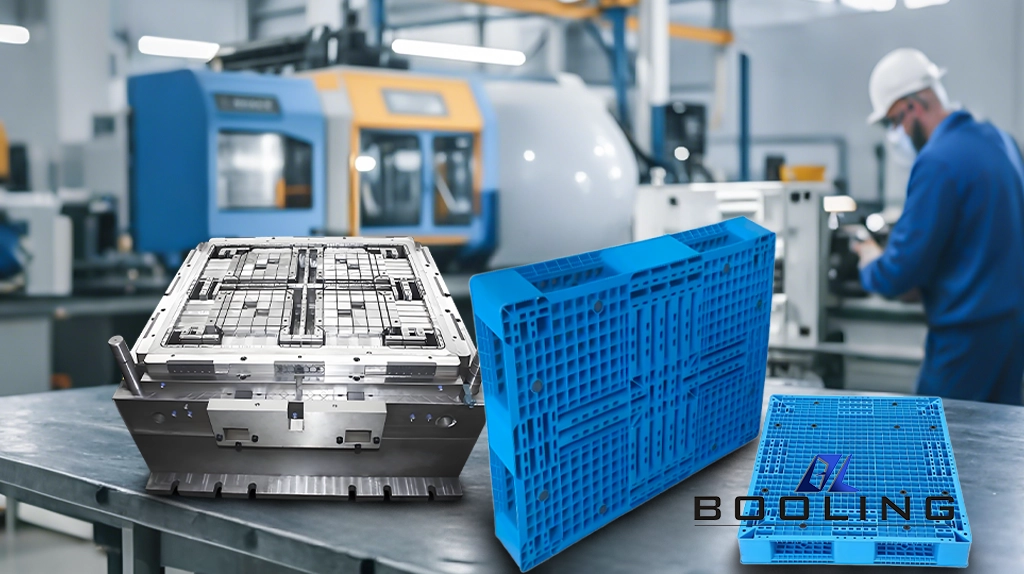
Double-Sided Integrated Pallet Mold Manufacturing Technology
The design and processing of double-sided integrated pallet molds are relatively complex, requiring the use of various high-precision instruments.
Using CNC machining techniques such as CNC milling, electrical discharge machining, wire cutting, etc., to ensure the machining accuracy of all parts of the mold and meet the requirements of complex shapes and sizes.
Nitriding or chrome plating treatment on the surface of molds can improve their hardness, wear resistance, and corrosion resistance, resulting in molds with higher surface quality and longer service life, which is beneficial for demolding products and plastics.
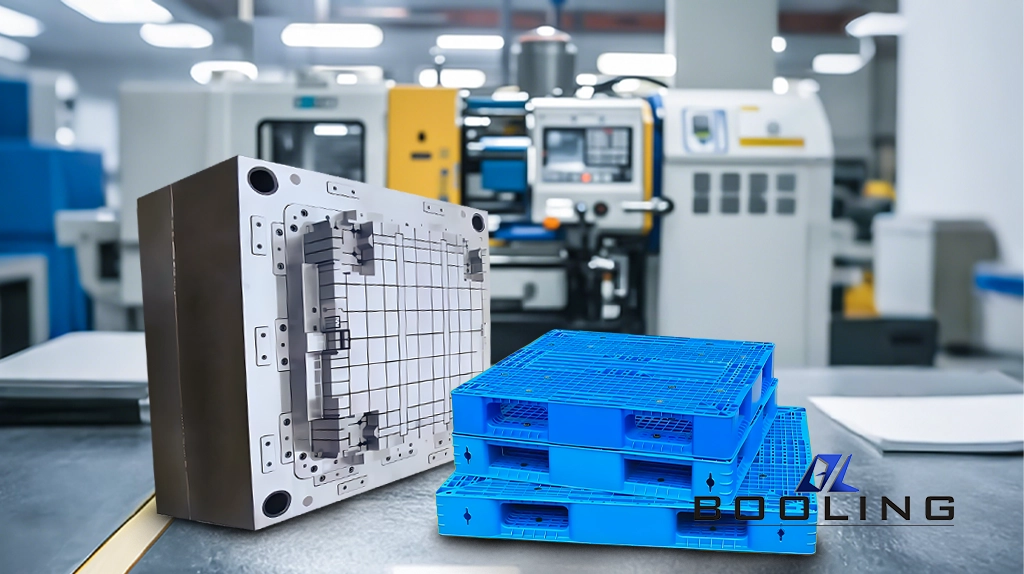
Post Treatment Of Double-Sided Integrated Pallet Mold
The double-sided integrated pallet mold belongs to large-scale products, and the post-processing process is cumbersome.
Annealing treatment
-Reason: Uneven plasticization or uneven cooling can lead to uneven shrinkage defects in various parts of plastic products. There are some internal stresses in the product, which can cause deformation or cracking defects during demolding or use. Annealing treatment is needed to eliminate internal stresses.
-Solution: Place the product in an oven or liquid medium at a certain temperature, such as water, glycerin, mineral oil, ethylene glycol, etc. After some time, slowly cool it to room temperature, use the heat during annealing to accelerate the relaxation of large molecules in the plastic product, and eliminate or reduce the stress after molding.
-Attention: The annealing temperature is generally 10-20 ℃ higher than the product’s operating temperature or 10-20 ℃ lower than the plastic’s thermal deformation temperature, otherwise defects such as warping and deformation may occur.
Automotive Mold Related Content
Applied’s expertise in modifying materials at atomic levels and on an ihdustrial scaleenables our customers to transform possibilities into reality.