Home > Injection Molding > LSR Injection Molding
LSR Injection Molding
The characteristics of silicone rubber (LSR) raw materials are combined with injection molding technology, and the products produced are widely exported to countries such as the United States, Vietnam, and India.
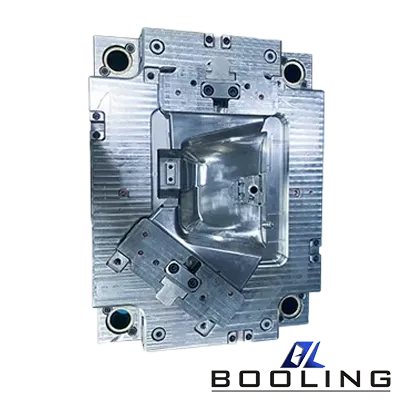
LSR Injection Molding
- Mold Making
- Selection of Silicone Rubber Materials
- Injection Molding Equipment and Process Selection
- Parameter Debugging
- Quality Control
LSR Injection Molding Capabilities
Liquid silicone rubber(LSR) has strong injection molding ability and can produce customized products very well.
·
US
Metric
Silicone
59 in. x 51.2 in. x 17.7 in.
1500mm x 1300mm x 450mm
Rubber
59 in. x 51.2 in. x 17.7 in.
1500mm x 1300mm x 450mm
*LSR injection molding can provide strict tolerances and airtightness performance.
LSR Injection Molding Material
When injecting liquid silicone rubber(LSR), the selection of materials should be determined based on the product and usage environment.
Material
- silicon Rubber
- silicone Oil
- Silicone Resin
- silane
The Advantage of LSR Injection Molding
Liquid silicone rubber(LSR) injection molding has outstanding advantages, with performance that conventional injection molding does not have.
Advantage:
- High Elasticity
- Environment Protection
- Good Insulation Performance
- Excellent Mechanical Performance
- Easy to Process
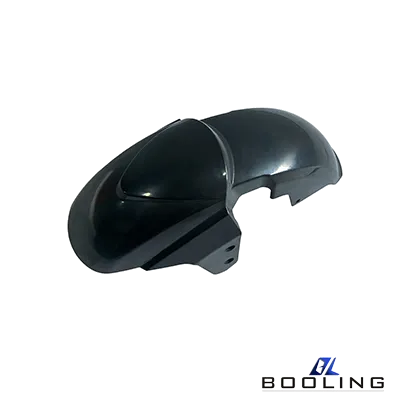
Application of LSR Injection Molding
The application of liquid silicone rubber(LSR) injection molding is very extensive, and it can be used to manufacture medical hoses, artificial organs, etc. in medicine; In the electronics industry, it is possible to manufacture cable insulation layers, protective sleeves, etc; In the automotive industry, it is possible to manufacture wiper blades, engine seals, etc; In furniture products, it can be used to manufacture kitchenware, baby products, etc.
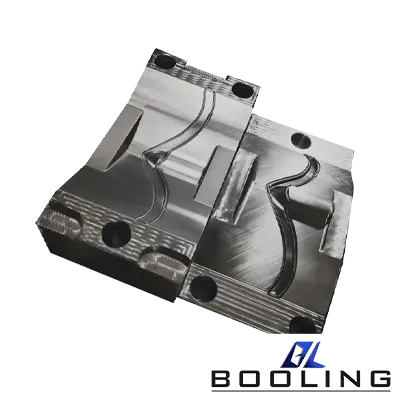
Guidelines for LSR Injection Molding
LSR injection molding plays a crucial role in the field of injection molding.
LSR Injection Molding
LSR Injection Molding
The characteristics of silicone rubber (LSR) raw materials are combined with injection molding technology, and the products produced are widely exported to countries such as the United States, Vietnam, and India. Manufacturers widely use this process to manufacture high-quality, durable, and precise silicone components with special properties, which are widely used in various industries.
In LSR injection molding, the manufacturer needs to thoroughly mix the two-component liquid silicone rubber material and then inject it into the heated mold cavity under high pressure. Liquid silicone rubber (LSR) is a material with unique properties, composed of a base polymer and a curing agent. When these two components are mixed and heated, a chemical reaction occurs, which can convert the liquid into a solid elastomer product with significant flexibility, heat resistance, and chemical stability.
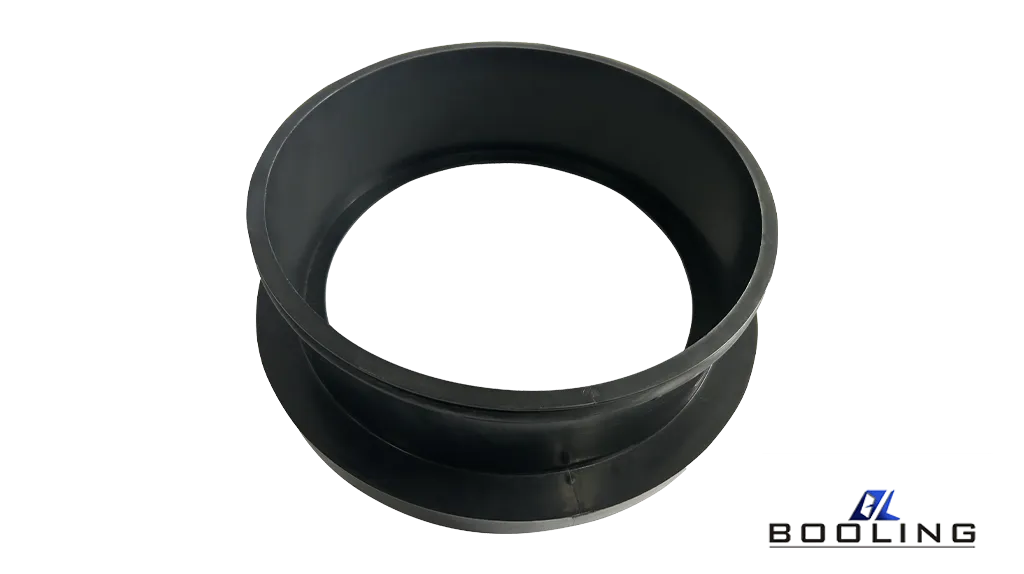
What is Liquid Silicone Rubber?
Liquid silicone rubber, abbreviated as LSR, is a highly elastic solid material that is widely used. It is a type of silicone rubber known for its excellent performance and diverse applications, and its unique processing methods enable it to stand out and become a leader in the industry.
LSR is a two-part system consisting of a vinyl-terminated polydimethylsiloxane polymer and a catalyst or curing agent. When these components are mixed, a chemical reaction occurs, transforming the liquid into a solid, yet flexible, silicone rubber. This curing process can be accelerated by applying heat, allowing for efficient manufacturing processes.
One of the most remarkable features of LSR is its ability to maintain its properties over a wide temperature range, from extremely low to high temperatures. It exhibits excellent thermal stability, making it suitable for applications where temperature fluctuations are a concern. Additionally, LSR boasts outstanding resistance to weathering, ozone, and ultraviolet radiation, ensuring long-lasting performance in outdoor environments.
The unique properties of LSR have led to its widespread adoption across numerous industries. In the medical field, LSR is highly valued for its biocompatibility, making it an ideal material for medical devices, implants, and healthcare products. Its non-toxic nature and resistance to bacterial growth make it a safe choice for applications that require frequent contact with the human body.
The automotive industry also benefits greatly from the use of LSR. Its excellent resistance to extreme temperatures, chemicals, and aging makes it a preferred material for gaskets, seals, and other components that must withstand harsh environmental conditions. LSR’s flexibility and durability ensure reliable performance and extended service life for these critical components.
In the electronics industry, LSR plays a crucial role in the manufacturing of various components, including keypads, gaskets, and protective coatings. Its excellent electrical insulation properties, coupled with its resistance to moisture and chemicals, make it an ideal choice for protecting sensitive electronic components from environmental factors.
The Advantage of LSR Injection Molding
LSR injection molding provides a unique performance combination for manufacturers to produce products, which is highly attractive to them. The most famous feature of the liquid silicone rubber used in this process is its extraordinary flexibility, durability, and resistance to extreme temperatures, chemicals, and environmental factors. These characteristics enable LSR injection molding to be applied in automotive, medical, and consumer goods industries with extremely high-performance requirements.
One of the key advantages of LSR injection molding lies in its ability to produce intricate and complex parts with exceptional precision. The injection molding process ensures consistent and repeatable results, minimizing the risk of defects and ensuring high-quality output. This level of precision is particularly valuable in industries where safety and reliability are paramount, such as the medical field, where LSR injection molding is used to create components for medical devices, implants, and surgical instruments.
Another significant benefit of LSR injection molding is its efficiency. The process allows for rapid production cycles, enabling manufacturers to meet tight deadlines and respond quickly to changing market demands. This efficiency translates into cost savings and increased competitiveness, making LSR injection molding an attractive option for businesses seeking to optimize their operations.
The versatility of LSR injection molding is also noteworthy. This technique can be used to create a wide range of products, from small, intricate components to larger, more complex assemblies. The ability to mold LSR with various colors, textures, and finishes further expands the design possibilities, allowing manufacturers to create visually appealing and functional products that meet the specific needs of their customers.
In addition to its technical advantages, LSR injection molding also offers environmental benefits. The process is relatively clean and produces minimal waste, aligning with the growing emphasis on sustainable manufacturing practices. Furthermore, the durability and longevity of LSR products can contribute to reducing the environmental impact associated with frequent replacements and disposals.
The industry and product requirements for injection molding are constantly developing and improving, and the advantages of LSR injection molding have become more apparent. From high-precision medical equipment to daily consumer goods, this technology is subtly influencing and changing our lives, permeating every aspect of our lives.
Application of LSR Injection Molding
LSR injection molding products have penetrated human life and are widely used in various industries.
The automotive industry has embraced
In the medical field, LSR injection molding plays a pivotal role in manufacturing critical components. Medical devices, such as catheters, implants, and surgical instruments, benefit from the biocompatibility and stabilizability of LSR materials. The molding process ensures precise dimensional accuracy and consistent quality, essential for patient safety and effective medical interventions.
The consumer electronics industry has embraced LSR injection molding for its ability to create sleek and ergonomic designs. From smartphone cases and wearable devices to remote controls and gaming accessories, LSR injection molding allows for the integration of tactile features and intricate details. The molded parts offer excellent grip, durability, and resistance to wear and tear, enhancing the user experience.
The food and beverage industry relies on LSR injection molding for the production of components that come into direct contact with consumables. LSR materials are FDA-approved and meet stringent hygiene standards, making them suitable for applications such as gaskets, seals, and food-handling equipment. The molding process ensures consistent quality and cleanliness, essential for maintaining food safety.
LSR injection molding has found applications in the aerospace industry, where lightweight and high-performance materials are crucial. LSR components are used in aircraft interiors, sealing systems, and various aerospace applications due to their resistance to extreme temperatures, vibrations, and environmental conditions. The molding process ensures precise tolerances and reliable performance in demanding aerospace environments.
The construction industry has embraced LSR injection molding for the production of weather-resistant seals, gaskets, and insulation components. LSR materials offer excellent thermal and moisture resistance, making them suitable for applications such as window and door seals, roofing components, and building insulation. The molding process ensures consistent quality and long-lasting performance in harsh outdoor conditions.
The energy sector has recognized the benefits of LSR injection molding for the production of components used in renewable energy systems. LSR materials are resistant to UV radiation, ozone, and extreme temperatures, making them ideal for applications such as solar panel seals, wind turbine components, and insulation for energy-efficient systems. The molding process ensures precise tolerances and reliable performance in demanding environmental conditions.
The sporting goods industry has leveraged LSR injection molding to create high-performance and durable components. From grip handles and protective gear to specialized equipment, LSR materials offer excellent shock absorption, flexibility, and resistance to wear and tear. The molding process allows for the integration of intricate designs and textures, enhancing the functionality and aesthetics of sporting goods.
The marine industry has embraced LSR injection molding for the production of components that can withstand harsh marine environments. LSR materials are resistant to saltwater, UV radiation, and extreme temperatures, making them suitable for applications such as boat seals, gaskets, and marine equipment. The molding process ensures consistent quality and reliable performance in demanding marine conditions.
Maintaining and Training Guidelines for LSR Injection Molding
A key step in the LSR injection molding process is to perform meticulous maintenance and upkeep on the relevant equipment. Regular inspections and preventive maintenance programs for molds and equipment are highly effective in preventing potential problems from becoming more severe, enabling timely resolution before they evolve into serious problems, and maintaining optimal equipment performance. The specific maintenance and repair guidelines mainly include thorough cleaning of the injection unit, mold cavity, and related components.
Effective training programs play a vital role in equipping operators with the necessary knowledge and skills to handle LSR injection molding processes effectively. Comprehensive training should cover topics such as material handling, machine operation, mold setup, and troubleshooting techniques. Hands-on training sessions and simulations can provide invaluable practical experience, enabling operators to develop a deep understanding of the intricate nuances involved in LSR injection molding.
Maintaining a clean and controlled environment is another critical aspect of LSR injection molding. Contaminants, dust particles, or moisture can significantly impact the quality of the final product, leading to defects or compromised performance. Implementing stringent housekeeping protocols, air filtration systems, and controlled humidity levels can help mitigate these risks and ensure consistent production quality.
Proper material handling and storage practices are equally important in LSR injection molding. LSR materials are sensitive to environmental conditions, and improper storage or handling can lead to degradation or contamination. Adhering to manufacturer guidelines for storage temperatures, humidity levels, and shelf life can help maintain the integrity of the materials and ensure consistent performance during the molding process.
Continuous improvement and optimization are essential for staying ahead in the competitive manufacturing landscape. Regular reviews of process parameters, such as injection pressure, temperature, and cycle times, can help identify opportunities for enhancing efficiency, reducing waste, and improving product quality. Embracing lean manufacturing principles and implementing data-driven decision-making can further streamline LSR injection molding operations.
In addition to technical aspects, effective communication and collaboration among team members are vital for successful LSR injection molding operations. Regular meetings, knowledge-sharing sessions, and cross-functional teamwork can foster a culture of continuous learning and improvement, enabling organizations to stay ahead of the curve in this dynamic field.
By fully adhering to maintenance and training guidelines, manufacturers can fully utilize the potential of LSR injection molding and provide high-quality durable products with superior accuracy and reliability. This not only ensures the normal operation of the equipment but also drives the company to continuously innovate and progress.
Quality Control in Lsr Injection Molding
The LSR injection molding process requires high specialization, and manufacturers need to pay attention to the different details of each stage. Whether it’s material preparation mold design, injection parameters, or final processing, each step is crucial in determining the final product quality. Strict quality control can ensure product consistency, minimize product scrap rates, and improve overall productivity.
One of the key aspects of quality control in LSR injection molding is material handling and preparation. LSR materials are sensitive to environmental conditions, such as temperature and humidity, which can impact their viscosity and curing properties. Strict protocols for material storage, handling, and mixing are essential to maintain consistent material properties and prevent contamination.
Mold design and maintenance are equally important in LSR injection molding. Precision-engineered molds with intricate cooling channels and venting systems are crucial for achieving accurate part dimensions and minimizing defects like flashes or short shots. Regular mold inspections, cleaning, and maintenance are necessary to ensure optimal performance and extend the mold’s lifespan.
During the injection molding process itself, various parameters, such as injection pressure, temperature, and cycle times, must be carefully monitored and controlled. Even slight deviations from the optimal settings can result in defects like air entrapment, incomplete filling, or warpage. Continuous monitoring and data logging of these parameters enable timely adjustments and facilitate root cause analysis in case of quality issues.
Post-processing operations, including deflashing, trimming, and inspection, are equally critical in LSR injection molding. Stringent visual and dimensional inspections, along with specialized testing methods like tear strength, compression set, and hardness tests, ensure that the final products meet the required specifications and performance criteria.
Quality control in LSR injection molding extends beyond the manufacturing process itself. Comprehensive documentation, traceability, and record-keeping practices are essential for maintaining compliance with industry regulations and facilitating continuous improvement initiatives. Detailed records of material batches, process parameters, and inspection results provide valuable insights for identifying trends, optimizing processes, and implementing corrective actions when necessary.