Home > Stamping Die > Metal Stamping Die
Booling provides solutions for customized production and processing of the metal stamping die, including the processing of single-process dies, composite, and continuous dies, which are suitable for precision processing and production of large quantities of sheet metal parts. At the same time, Booling develops and designs dies with a high degree of automation, which can be produced with the help of punching machines and manipulators to improve the production efficiency of parts.
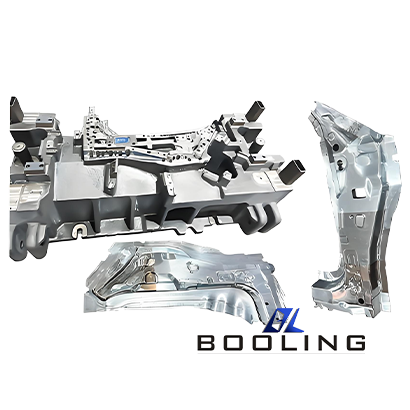
Metal stamping die is used for cutting, punching, forming, and deforming metal sheets to obtain the required shape and contour, which is suitable for large-scale customized parts production.
Key Points of Metal Stamping Die:
- Die Construction
- Two-part Design
- Press Operation
- Material Placement
- Shaping Process
- Multiple Operations
- High-speed Production
Metal Stamping Die Capabilities
Metal stamping die uses pressure to change the shape of metal sheets, so, during the production process, the setting of parameters determines the quality of the final product.
·
US
Metric
Aluminium Alloy
68.9in. x 27.6 in. x17.7in.
1750mm x 700mm x450mm
Magnesium Alloy
68.9in. x 27.6 in. x17.7in.
1750mm x 700mm x450mm
Copper Alloy
68.9in. x 27.6 in. x17.7in.
1750mm x 700mm x450mm
*Proper material selection is crucial for achieving the desired die performance, longevity, and cost-effectiveness in metal stamping operations.
Metal Stamping Die Material
Booling provides raw materials such as alloy steel, high-speed steel, cemented carbide, carbon tool steel, low-alloy tool steel, aluminum alloy, zinc-based alloy, etc. for mold processing and production, and provides mold material selection suggestions based on product types and manufacturer requirements.
Material
- Aluminium Alloy
- Magnesium Alloy
- Copper Alloy
The Advantages of Metal Stamping Die
- The production and maintenance costs of the metal stamping die islow
- The stamping process can be highly automated, reducing labor costs and errors
- The products have good dimensional accuracy and consistency
- The dies have the same characteristics, stable quality, and good interchangeability of parts
- It can produce more complex shapes, thin-walled, light-weight, and high-rigidity parts, with faster production speeds
- Booling can guarantee higher accuracy and strict tolerances
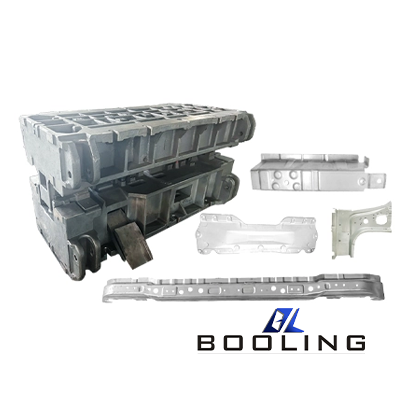
Application of Metal Stamping Die
Metal stamping die is widely used in industries such as automotive, aerospace, automobile, consumer goods, and medical to achieve high-quality production of metal parts.
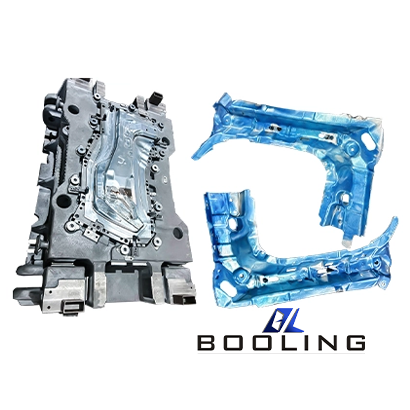
Guidelines for Metal Stamping Die
Metal stamping die provides equipment support and high-speed manufacturing capabilities for sheet metal production in various industries.
Metal stamping die uses a stamping machine to apply pressure to metal sheets, causing the sheets to change shape. Booling provides design and processing of drawing dies, punching dies, bending dies, riveting dies, and other models, and provides services such as design solutions, process dimensions, material selection, and parameter settings.
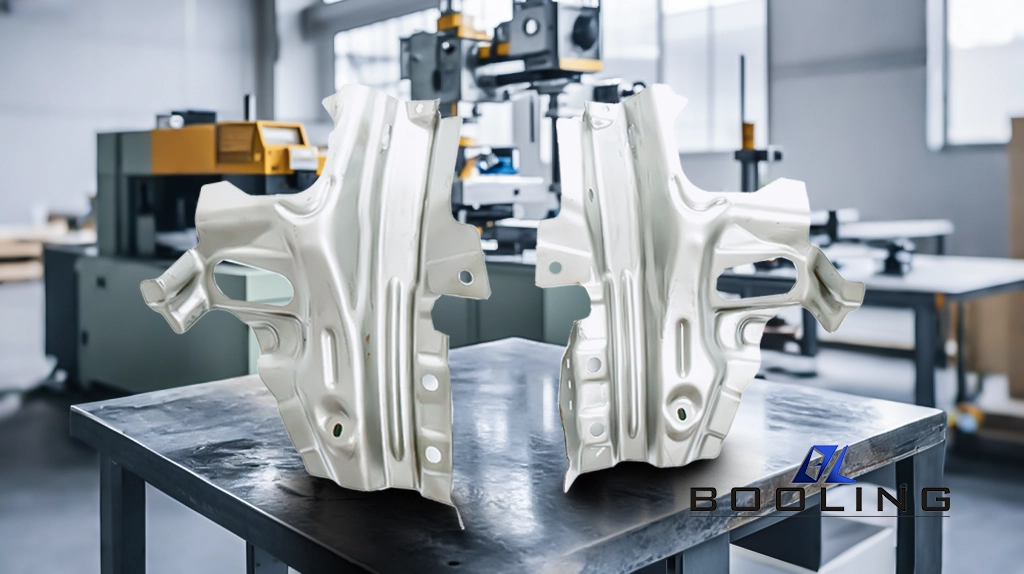
Metal Stamping Die Processing Technology
In the manufacture of the metal stamping die, Booling correctly designs the structure of the stamping die and uses advanced equipment for processing.
- Lathe Processing
Lathe processing is also called turning, which forms a specified shape by cutting the raw material. Booling’s lathe can perform six-sided milling on the blank material, accurately control the thickness, and obtain millimeter-level errors. Lathe processing requires a certain amount of processing allowance to provide dimensional accuracy for subsequent heat treatment.
- Milling Machine Processing
Engineers generally use multiple tool positions for cutting and milling cutters to cut the mold. During the milling process, it is necessary to strictly control the feed speed and feed amount, and replace the easily worn tools in time.
- Precision Punching Method
To ensure the quality of the punching section, Booling usually uses precision punching methods, such as continuous punching, laser punching, hydraulic punching, etc., which are not limited by materials and have a wide range of applications. It can obtain a vertical and clean punching surface to meet the punching needs of complex shapes and positions.
Application of Metal Stamping Die
The metal stamping die can produce precision parts in large quantities. Booling uses this technology to achieve rapid delivery of products in the fields of automobiles, home appliances, aerospace, medical, electronic equipment, etc.
- Stamping dies can realize the precision production of automotive metal parts, such as body shells, body structural parts, interior parts, car door panels, battery boxes, fuel tanks, etc.
- In the field of home appliances, the manufacture of metal parts such as TV shells, refrigerator door panels, electrical transformer cores, brackets and fixings, battery shrapnel, etc.
- In the field of aerospace, stamping dies are the key process for manufacturing load-bearing parts, aircraft frames, and bent pipe parts
- In the medical field, it is used for the processing of metal implants, medical equipment, dental orthotics, etc.
- It is suitable for the precision processing of internal metal structural parts and shells of various electronic devices such as smartwatches, phones, and computers, and has aesthetics