Home > 3D Printing Service > Polycarbonate 3D Printing
Polycarbonate 3D Printing
Polycarbonate (PC) material for 3D printing is a high-performance thermoplastic material that has gained significant popularity in the field of 3D printing. Known for its excellent strength, impact resistance, and heat resistance.
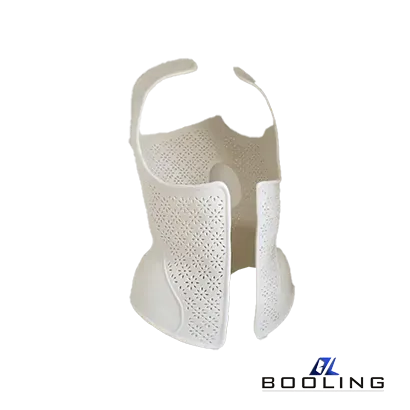
Polycarbonate 3D Printing
Polycarbonate 3D printing involves the use of polycarbonate filaments or powders to create parts through additive manufacturing processes.
Polycarbonate (PC)
Carbon Fiber Composites
FR Blends
- ABS Blends
Polycarbonate 3D Printing Capabilities
Polycarbonate 3D printing provides a unique combination of performance, making it an ideal choice for widespread applications
·
US
Metric
Polycarbonate
47.2in. x 31.4 in. x 23.6 in.
1200mm x 800mm x600mm
*Polycarbonate is more durable and sturdy than many other common thermoplastic materials.
Polycarbonate 3D Printing Material
Polycarbonate has excellent impact resistance, making it ideal for parts that will experience wear and tear, such as gears and pulley sheaves.
Material
- Polycarbonate
The Advantages & Disadvantages of Polycarbonate 3D Printing
Compared to other materials and traditional printing methods, polycarbonate 3D printing has the following key advantages and disadvantages.
Advantages
Disadvantages
Impact Resistance
Material aging
Flexibility
Limited heat resistance
Abrasion
Limited materials
Chemical Resistance
Weak stiffness
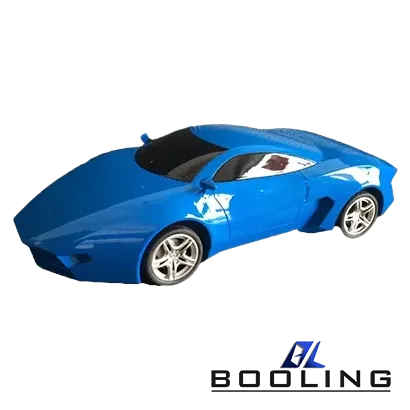
Application of Polycarbonate 3D Printing
Polycarbonate 3D printing is widely used in many industries, such as automotive, construction, and aerospace, due to its excellent performance.
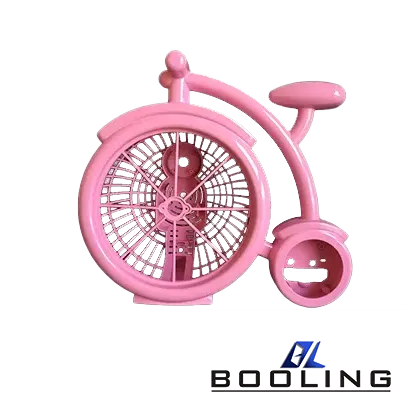
Guidelines for Polycarbonate 3D Printing
Polycarbonate 3D Printing is a unique printing technology.
Polycarbonate 3D Printing
Polycarbonate 3D Printing
Polycarbonate (PC) is a high-performance thermoplastic material that has gained significant popularity in the world of 3D printing. Known for its exceptional strength, impact resistance, and heat tolerance, polycarbonate offers a unique combination of properties that make it an ideal choice for a wide range of applications.
Polycarbonate 3D printing involves the use of polycarbonate filaments or powders to create parts through additive manufacturing processes. The two primary methods for 3D printing with polycarbonate are Fused Deposition Modeling (FDM) and Selective Laser Sintering (SLS).
1. Fused Deposition Modeling (FDM)
FDM is one of the most common 3D printing technologies used for polycarbonate, a polycarbonate filament is extruded through a heated nozzle and deposited layer by layer to build the part. FDM is suitable for producing strong, lightweight parts with good dimensional accuracy.
2. Selective Laser Sintering (SLS)
SLS uses a laser to sinter powdered polycarbonate material layer by layer to create the final part. This technology can produce parts with complex geometries and excellent mechanical properties. SLS is particularly effective for creating moving and interlocking parts, eliminating the need for the assembly of individual components.
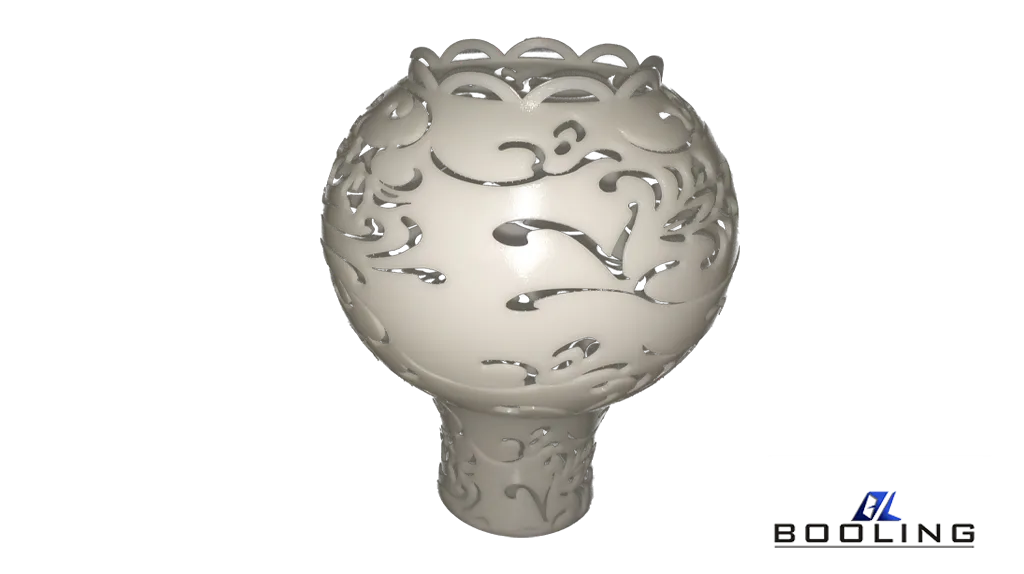
Advantages of Polycarbonate 3D Printing
Polycarbonate 3D printing offers several key advantages over other materials and traditional manufacturing methods:
1.Strength and Durability
Polycarbonate is stronger and more durable than many other common thermoplastics, such as ABS and PLA. This makes it suitable for functional parts that need to withstand mechanical stress.
2.Impact Resistance
Polycarbonate has excellent impact resistance, making it ideal for parts that will experience wear and tear, such as gears and pulley sheaves.
3.Heat Resistance
Polycarbonate can withstand high temperatures without deforming, making it perfect for parts that will be exposed to heat.
4.Transparency
Polycarbonate’s transparent nature and light transmittance allow for several unique applications in the creation of high-quality clear or translucent objects with beautiful looks.
5.Flexibility
Polycarbonate offers a great rigidity-to-flexibility ratio. Parts printed with thin walls are flexible, while those with thicker walls are rigid. This property is ideal for producing components like living hinges and snap-fit parts.
6.Chemical Resistance
Polycarbonate is resistant to many chemicals, including oils and fuels, which makes it suitable for automotive and industrial applications.
Types of Polycarbonate 3D Printing
Polycarbonate 3D printing offers a range of material options beyond pure polycarbonate, each with its unique properties and applications:
1.Polycarbonate (PC)
Pure polycarbonate is the primary material for polycarbonate 3D printing, chosen for its exceptional strength, impact resistance, and heat tolerance.
2.ABS Blends
Blending polycarbonate with ABS (acrylonitrile butadiene styrene) can provide a balance between polycarbonate’s strength and ABS’s affordability and printability.
3.Carbon Fiber Composites
Incorporating carbon fiber into polycarbonate can enhance the material’s strength and stiffness while maintaining its heat resistance.
4.FR Blends
“FR” stands for “flame retardant.” Blending polycarbonate with flame-retardant additives makes the material suitable for applications where fire safety is a concern.
5.Polyethylene Glycol (PEG) Blends
Adding polyethylene glycol to polycarbonate can improve its printability and reduce warping, making it advantageous for complex geometries or large parts.
Methods of Polycarbonate 3D Printing
The methods used in polycarbonate 3D printing can be broadly categorized into two main approaches: direct 3D printing and the use of 3D printed molds for traditional polycarbonate fabrication.
- Direct 3D Printing
Direct 3D printing involves the use of polycarbonate filaments or powders to create parts directly from a digital model. This method is suitable for producing functional prototypes, custom tools, and end-use parts with high strength and durability.
Polycarbonate 3D printing typically involves several key steps:
1.Design
The process begins with creating a digital 3D model of the desired object using computer-aided design (CAD) software. This model serves as the blueprint for the subsequent printing process.
2.Preprocessing
Once the design is complete, the 3D model is prepared for printing. This involves tasks like scaling, orienting, and positioning the model within the build volume, as well as generating support structures for overhangs and intricate features.
3.Printer Setup
Before printing, the 3D printer must be calibrated and prepared. This includes ensuring that the print bed is perfectly level, the nozzle is clean, and the appropriate printing parameters are selected. For polycarbonate, precise temperature settings for both the extruder and the build chamber are crucial to prevent warping and ensure proper layer bonding.
4.Printing
The actual printing process involves the layer-by-layer deposition of the polycarbonate material, following the instructions generated by the slicing software.
5.Post-Processing
After printing, the part may require post-processing steps such as support removal, sanding, or surface finishing to achieve the desired appearance and functionality.
Maintenance of Polycarbonate 3D Printing Equipment
Proper maintenance of polycarbonate 3D printing equipment is essential to ensure consistent part quality and extend the lifespan of the machinery. Here are some key maintenance practices:
1.Regular Cleaning
Keep the printer’s build platform, nozzles, and other components clean to prevent material buildup and ensure smooth operation. Use appropriate cleaning tools and solvents recommended by the printer manufacturer.
2.Nozzle Maintenance
Polycarbonate’s tendency to absorb moisture and its abrasive nature can cause wear on the printer’s nozzle. Regularly inspect and replace the nozzle as needed to maintain print quality.
3.Calibration
Periodically calibrate the printer to ensure accurate layer deposition and dimensional accuracy. This includes bed leveling, extruder calibration, and checking the alignment of the print head.
4.Lubrication
Lubricate moving parts, such as rails and bearings, to reduce friction and wear. Use lubricants recommended by the printer manufacturer.
5.Software Updates
Keep the printer’s firmware and software up to date to benefit from the latest features, improvements, and bug fixes.
6.Material Storage
Store polycarbonate filaments and powders in a dry, cool environment to prevent moisture absorption, which can affect print quality. Use airtight containers with desiccants to maintain optimal material conditions.
Applications of Polycarbonate 3D Printing
Polycarbonate 3D printing is used in a wide range of applications across various industries due to its exceptional properties and versatility:
1.Aerospace
-Structural Components
-Prototyping
2. Automotive
– Performance Parts
– Customization
3.Defense
– Lightweight Armor
– Unmanned Systems
4. Consumer Goods
– Sporting Equipment
– Electronics
5. Manufacturing
– Tooling and Fixtures
– Replacement Parts
6.Medical
– Prosthetics and Orthotics
– Surgical Instruments
– Educational Models