Home > Injection Molding > Polyurethane Injection Molding
Booling’s mature polyurethane injection molding technology provides many manufacturers with high-quality parts that are lightweight, highly elastic, heat-insulating, sound-insulating, and shock-proof. Our engineers select the most suitable materials for heating and mixing to form a uniform melt, use the screw injection molding technology of the injection molding machine to ensure uniform flow, inject it into the polyurethane mold through the nozzle, fill the mold cavity, and form precise polyurethane parts after cooling and curing. Provide complete production solutions for factories in the automotive, furniture, packaging, and other industries.
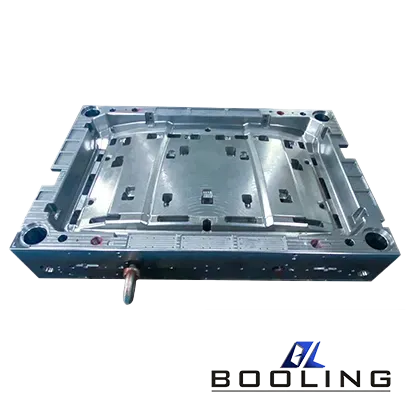
Polyurethane materials integrate seamlessly with injection molding technology, enabling precision manufacturing of large-volume parts.
- Raw Material Preparation
- Preprocessing
- Measurement & Mixing
- Injection Molding
- Cooling and Shaping
- Demolding
Polyurethane Injection Molding Capabilities
Engineers analyze the product’s size, geometry, and precision requirements and are able to produce thin-walled polyurethane products that meet tight tolerance requirements.
·
US
Metric
Polyurethane(PU)
59 in. x 51.2 in. x 17.7 in.
1500mm x 1300mm x 450mm
*In addition, polyurethane injection molding also provides customized services for complex products.
Polyurethane Injection Molding Material
Polyurethane is a widely used material in the injection molding process. Booling provides processing materials such as polyurethane foam and elastomeric polyurethane.
Material
- Polyurethane(PU)
The Advantage & Disadvantage of Polyurethane Injection Molding
- It has good durability and use strength, high wear resistance and impact resistance, and extends the service life of the product
- Polyurethane has wide flexibility and versatility and can achieve flexible conversion of multiple hardnesses
- It has excellent tolerance to chemical solvents such as acids and alkalis and can withstand multiple cleaning and disinfection
- It has an excellent thermal insulation effect. The closed-cell structure inside polyurethane can provide insulation properties for the material
- As an elastomer, it can absorb and resist noise and vibration
- Polyurethane can easily realize the design and processing of complex shapes, has strong processability and plasticity, and has the characteristics of lightweight
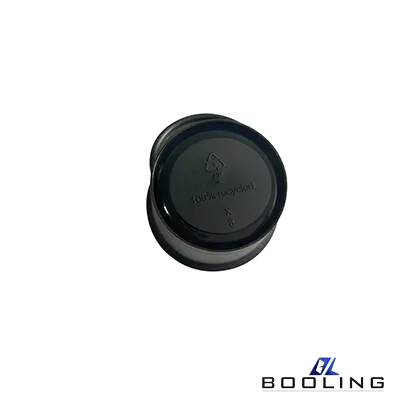
Application of Polyurethane Injection Molding
Polyurethane injection molded parts have good chemical and physical properties and are widely used in the field of precision manufacturing, including the manufacture of gaskets, seals, shock absorbers, buffers, etc.
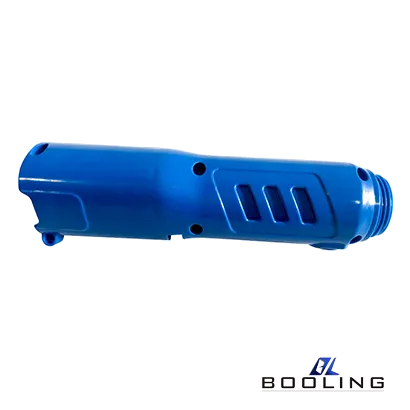
Guidelines for Polyurethane Injection Molding
Booling provides a one-stop service for precision polyurethane injection molding processing. The products have the characteristics of heat resistance, stability, and environmental protection.
Polyurethane injection molding materials are composed of isocyanate and polyol, which are fully mixed for processing and injected into the mold. PU injection molding molds are generally composed of materials such as carbon steel, alloy steel, tool steel, and stainless steel, and are made through precision grinding and EDM.
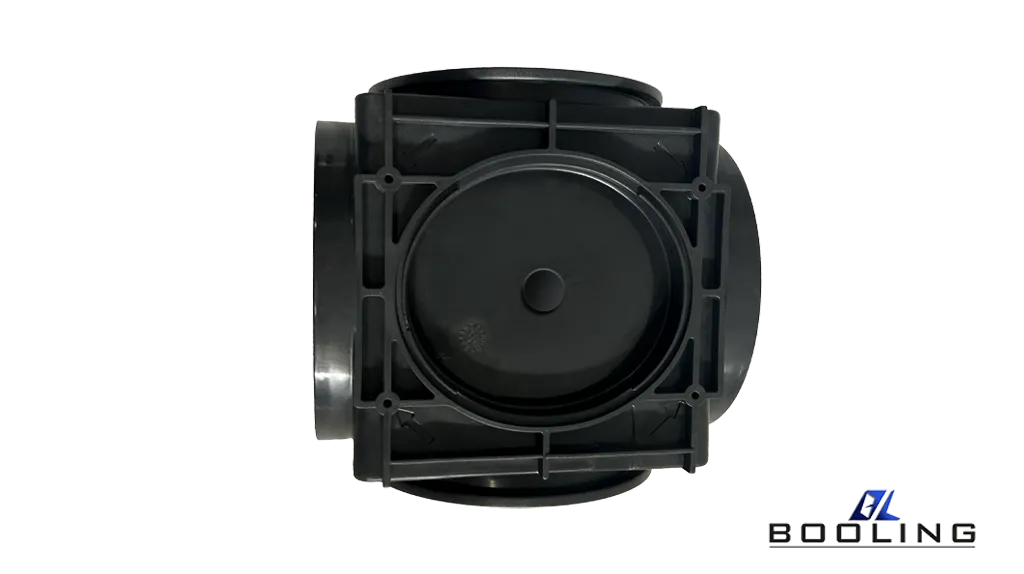
Precautions for Polyurethane Injection Molding
Polyurethane injection molding is widely used in the processing of plastic parts. Booling provides precautions for reference to ensure the quality and performance of the product.
- Material moisture content: The polyurethane particles must be fully dried before processing. Excessive moisture content in the material will cause defects on the product surface
- Shrinkage rate: The shrinkage rate of polyurethane is about 1~3%. Booling extends the holding time and increases the cavity pressure by designing point gates to reduce the shrinkage rate. In addition, the design of a reasonable cooling water channel can also avoid excessive shrinkage caused by uneven cooling.
- Precautions for mold design: The mold should have the function of promoting uniform flow and cooling of the melt, balancing the runner system, and ensuring uniform filling inside the mold cavity; involving sufficient draft angles to facilitate product demolding
- Processing parameter optimization: Polyurethane injection molding requires sufficient melt temperature, generally 120~240℃, to ensure that the mold is completely melted and plasticized; try to set a higher injection speed and pressure to overcome the higher melt viscosity of polyurethane and ensure that the mold cavity is filled; appropriate holding pressure and cooling time can ensure the shape of polyurethane and avoid excessive shrinkage
Processing of Polyurethane Injection Molding Molds
Booling polyurethane injection molding molds use CNC milling technology to achieve high-precision processing.
- The design of polyurethane injection molding molds uses CAD technology to achieve the depiction of three-dimensional models
- Submit the 3D drawings to the engineer for review, and order relevant materials such as steel, mold frames, etc. after the review is passed
- Rough processing of the core and cavity, and heat treatment to improve the overall hardness and mechanical properties of the mold
- Engineers use grinding, CNC machining, boring, and other technologies to fine-process the mold to improve the accuracy of the mold
- Our engineers can customize the cooling system, exhaust, and ejection mechanism, which fully meets the processing requirements of users and products
- The logo can be customized, and direct depiction and insert production on the cavity can be provided to improve processing flexibility
- For assembly and inspection, we have high-precision inspection equipment such as inspection fixtures and micrometers to achieve precision assembly
- We will provide a trial mold video with more than two cycles to ensure the normal processing of the mold