Home > Injection Molding > PVC Injection Molding
Booling’s designers have better control over the flow of the melt through the design of the point gate for PVC injection molding, avoiding weld marks and providing pipe manufacturers with injection molding products with good surface quality. Booling uses advanced precision grinding technology and CNC machining technology to obtain higher quality molds, achieve rapid delivery of PVC injection molding products, and meet users’ quality requirements.
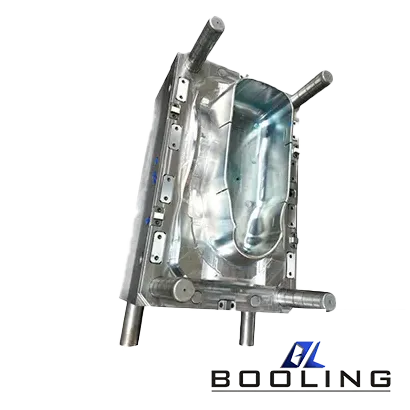
PVC injection molding is to press molten PVC particles or powder into the mold through the die head and cool it to form a product. This technology can be used to obtain parts with complex internal structures.
- Mould design
- Prepare raw materials
- Injection molding
- Subsequent processing
PVC Injection Molding Capabilities
Booling achieves high-quality molding by strictly controlling the quality of the PVC injection molding process.
·
US
Metric
Hard PVC
59 in. x 51.2 in. x 17.7 in.
1500mm x 1300mm x 450mm
Soft PVC
59 in. x 51.2 in. x 17.7 in.
1500mm x 1300mm x 450mm
*In addition, the tolerance and accuracy of PVC injection molded products are very strict.
PVC Injection Molding Material
Booling offers rigid PVC and soft PVC for injection molding, with significant differences in hardness and flexibility.
Material
- Hard PVC
- Soft PVC
The Advantage & Disadvantage of PVC Injection Molding
- The PVC injection molding process has high processing efficiency, achieving the production of large quantities of products in a short time, and is cost-effective
- It can easily create complex shapes and details, and adapt to changes in modifications
- It has durability and strength, can withstand extreme environments, and always ensures the consistency of product production
- The product surface is smooth and shiny, suitable for the production of parts with high surface requirements
- It has good corrosion resistance and electrical insulation properties
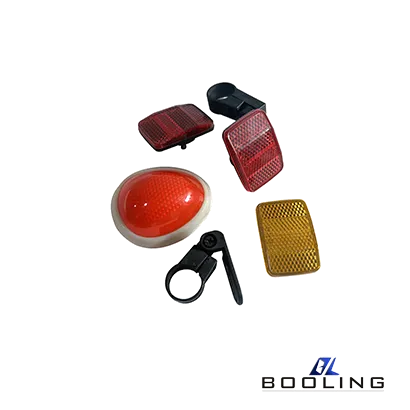
Application of PVC Injection Molding
PVC injection molding technology is widely used in many industries, including construction, automobiles, electronics and electrical appliances, medical care, agriculture, pipelines, etc.
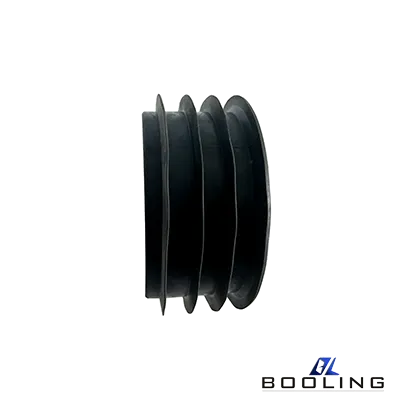
Guidelines for PVC Injection Molding
PVC is molded with molds and injection molding machines to achieve highly consistent parts production.
PVC injection molding technology products have excellent physical and chemical properties. It mainly injects molten PVC material into the mold cavity through the injection molding machine head, cools and solidifies to form products, with high production efficiency and fast delivery.
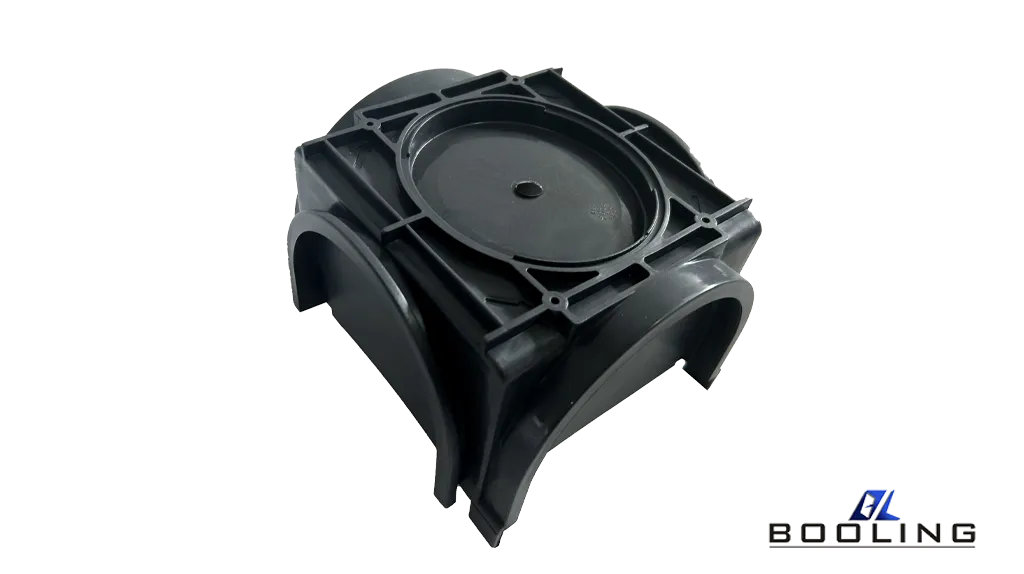
PVC Injection Molding Materials
Booling provides hard, soft, and foamed PVC to achieve rapid molding and meet the processing needs of different products.
- Hard PVC: It has high strength and impact resistance, and is often used in the processing of pipes, accessories, window and door frames
- Soft PVC: This type of PVC has high toughness, is soft and easy to process, and is often used in the processing of hoses, gaskets, and seals
- Foamed PVC: This is a lightweight material that is supported by introducing bubbles into PVC during the injection molding process. It is used in applications that require insulation or weight reduction, such as foam boards and some packaging materials
PVC Injection Molding Process
PVC injection molding involves multiple processing steps, and each step needs to ensure a certain degree of precision.
- Mold design: Booling uses CAD technology to design 3D models, which are reviewed by technicians, and steel and standard parts are purchased. CNC machine tools and EDM technology are used to precisely process the mold and depict the core and cavity of the mold
- Heat treatment: Heat treatment of the mold to improve the surface hardness and mechanical properties of the mold and extend its service life
- Material pretreatment: Drying and impurity screening of PVC
- Feeding: PVC particles are fed into the hopper of the injection molding machine and then conveyed into the barrel
- Heating and melting: When PVC passes through the barrel, it is melted under the shear force, friction, and heating of the screw, and enters the mold cavity through the nozzle. The molten plastic is evenly dispersed to every corner of the mold cavity to avoid short-shot defects
- Cooling and curing: The setting of the cooling water channel must ensure a uniform cooling effect to avoid shrinkage and deformation of plastic parts caused by temperature differences. The setting of the cooling water channel should be as close to the mold cavity as possible. Booling provides vertical and inclined cooling water channel settings.
- Demolding: Before demolding, it is necessary to ensure that the mold has a good exhaust system to avoid defects such as surface bubbles.