Home > Silicone Injection molding: A Combination of High Temperature Resistance & High Elasticity
Details
Details:
Model
Material
Brand
Origin
Application
Booling-Injection Mold-1
P20, 718, S136, 2738 etc
Booling
China
Home Appliance parts
Booling uses self-developed silicone injection mold molding technology, which can accurately control the size and precision of the terminal product, achieve a combination of high temperature resistance and high elasticity, and meet the needs of users in different environments. Our technical director emphasized: “Through the ‘multi-stage temperature control system’ and ‘dynamic pressure compensation technology’, we control the dimensional tolerance of silicone products within ±0.05mm, which is particularly critical in medical-grade silicone products.” Silicone injection molding utilizes polymer silicone rubber materials, which are injected into the mold by an injection molding machine and formed into a specific shape product after cooling and curing. Booling uses self-developed mold technology, which can accurately control the size and precision of the terminal product, achieve a combination of high temperature resistance and high elasticity, and meet the needs of users in different environments.
Advantages of silicone injection molding:
- High temperature resistance
- Flexibility and high elasticity
- Non-toxic and hygienic, FDA certified
- Chemical resistance
Related Hot Products
In terms of silicone injection molding technology innovation, Booling has always adhered to the core concept of “precise control, value creation”. Different from traditional molding processes, Booling’s silicone injection molding can use micron-level correction algorithms for mold cavity dimensions based on the shrinkage characteristics of silicone rubber materials, and control the dimensional tolerance of the end product within ±0.02mm, far exceeding the industry average standard.
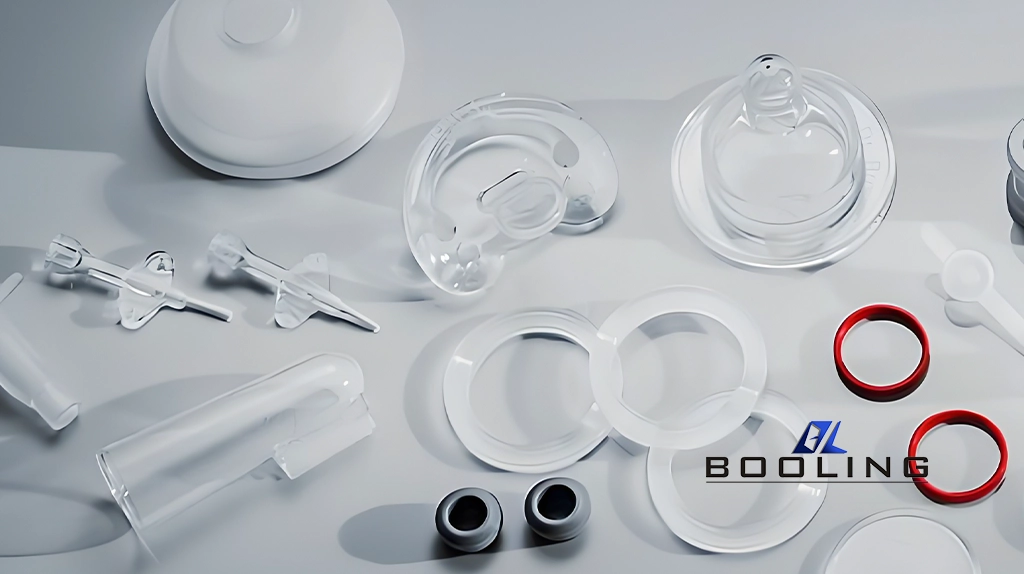
High Elastic Physical Structure Mechanism of Silicone Injection Molding
In the field of polymer materials, Booling has conducted in-depth exploration and innovative application of silicone materials with advanced cutting-edge technology. Engineers pointed out that the high elasticity of silicone injection molding materials comes from its unique lightly cross-linked network molecular structure and amorphous molecular arrangement characteristics.
Booling engineers use a self-developed precision vulcanization process to accurately control the ratio and reaction conditions of vulcanizers such as peroxides to form a highly optimized lightly cross-linked network structure of silicone molecular chains. This structure can balance the force exerted on the product, effectively limit the excessive slippage of the molecular chain when subjected to force, and ensure the stability of the entire structure.
Silicone products present a unique amorphous arrangement morphology, with the molecular chains in a completely amorphous arrangement and no crystalline area. In a low-temperature environment, the molecular chain will not lose elasticity due to crystallization and hardening.
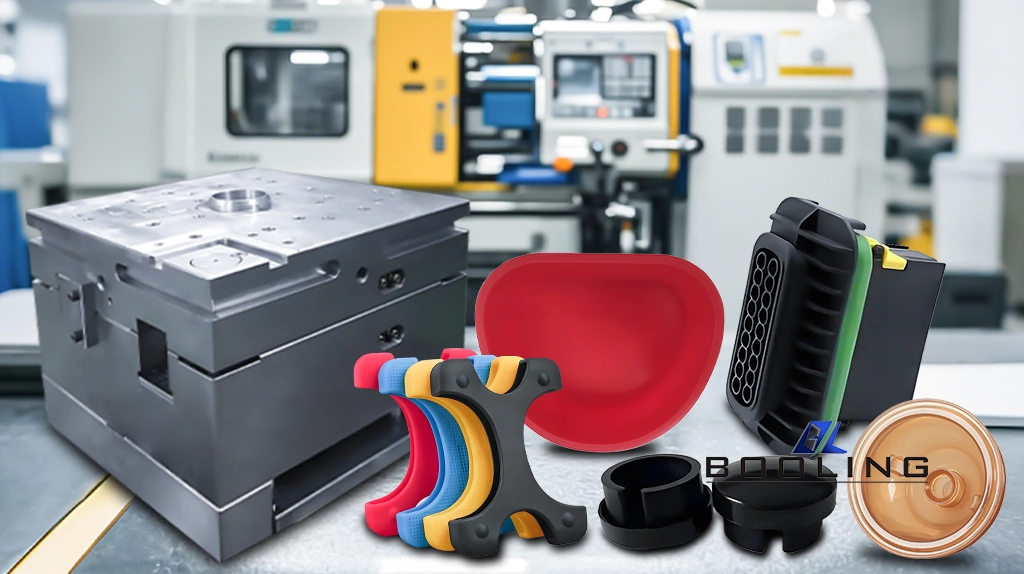
Silicone Injection Molding Process Parameters
Booling designs silicone injection molding molds and sets different parameters according to different requirements of customers to meet users’ customized needs.
Table 1: Silicone Injection Molding Process Parameters Reference
Parameter Category | Specific Parameters | Common Range |
Preprocessing Stage | Temperature | 25-35℃ |
Drying Time | 40-60℃, 1-2 hours (no need to dry unless it is damp) | |
Injection Molding Equipment Parameters | Barrel Temperature | Solid silicone: 80-120℃ Liquid silicone: 40-80℃ |
Mold Temperature | Solid silicone: 160-220℃ Liquid silicone: 120-180℃ | |
Injection Pressure | Solid silicone: 50-150MPa Liquid silicone: 10-50MPa | |
Injection Speed | Solid silicone: 5-20 cm³/s Liquid silicone: 10-30 cm³/s | |
Holding Pressure | 30%-60% of injection pressure | |
Holding Time | 5-30s | |
Vulcanization Parameters | Temperature | Same as Mold Temperature |
Vulcanization Time | Solid silicone: 10-60 seconds (in-mold vulcanization) + post-vulcanization (150-200°C, 2-4 hours) Liquid silicone: 10-30 seconds (in-mold vulcanization) + post-vulcanization (120-150°C, 1-2 hours) |
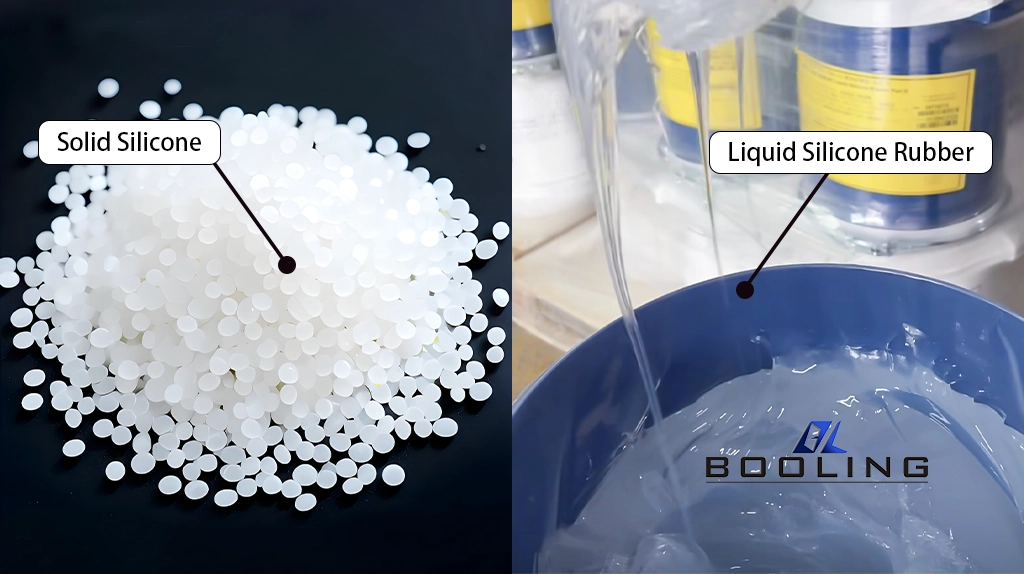
Silicone Injection Molding Precautions
Booling’s general manager said: “We not only provide silicone injection molding molds, but also provide a full-process solution from material selection, process development to mass production support. At present, Booling’s silicone injection molding technology has obtained 23 patents and serves more than 50 of the world’s top 500 companies.” Silicone injection molding is widely used in the field of polymer material processing and has become a core manufacturing technology. In the processing process, the type of silicone, the complexity of the product, the equipment and post-processing requirements are different, and the process used is also different.
- Differences in Silicone Types: Liquid silicone (LSR) has better fluidity, and the process parameters are usually lower than solid silicone (SSI), and special injection molding equipment is required.
- Product Complexity: For complex thin-walled products, our company has established a dynamic process parameter model that can effectively solve the problem of air entrapment in thin-walled structures.
- Equipment Debugging: When replacing new materials or new molds, it is necessary to optimize the parameters through trial molds to avoid defects caused by mass production.
- Post-Processing: After post-vulcanization treatment, the aging resistance, electrical properties and mechanical strength of silicone products can be effectively improved.
Contact Booling now to get exclusive silicone injection molding solutions! Contact us now to enjoy a 5% discount on your first order.
Our silicone injection molding service commitment:
Delivery guarantee: mold delivery within 15-25 days
Quality assurance: 12-month quality warranty
Ongoing support: regular process optimization service
Automotive Mold Related Content
Applied’s expertise in modifying materials at atomic levels and on an ihdustrial scaleenables our customers to transform possibilities into reality.