Home > Metal Stamping Die Design
Metal Stamping Die
Metal stamping molds can stamp a large number of parts and also meet the requirements of stamping small batches of high-precision parts. This customized stamping mold achieves automation, realizing automatic feeding, output, and stacking.
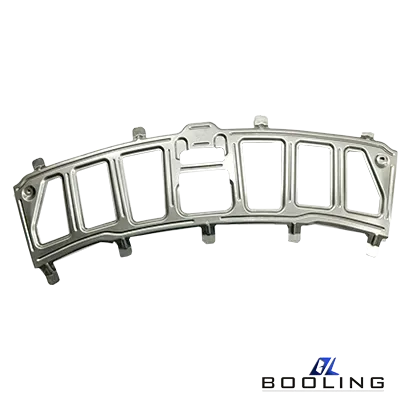
Metal stamping die design plays a very important role. A die is a component produced through design to produce a workpiece that meets the requirements. In the process of stamping, operators generally choose dies with specialized characteristics. When encountering a complex part, requires several sets of dies to be manufactured and formed. Not only are the steps very complex, but the metal stamping die design produced also requires extremely high precision and quality, making it a technology-intensive product. If a large number of processed parts are produced, it will further expand the advantages of metal stamping die design. Having good die manufacturing equipment is the most crucial step in becoming an advanced die manufacturing technology.
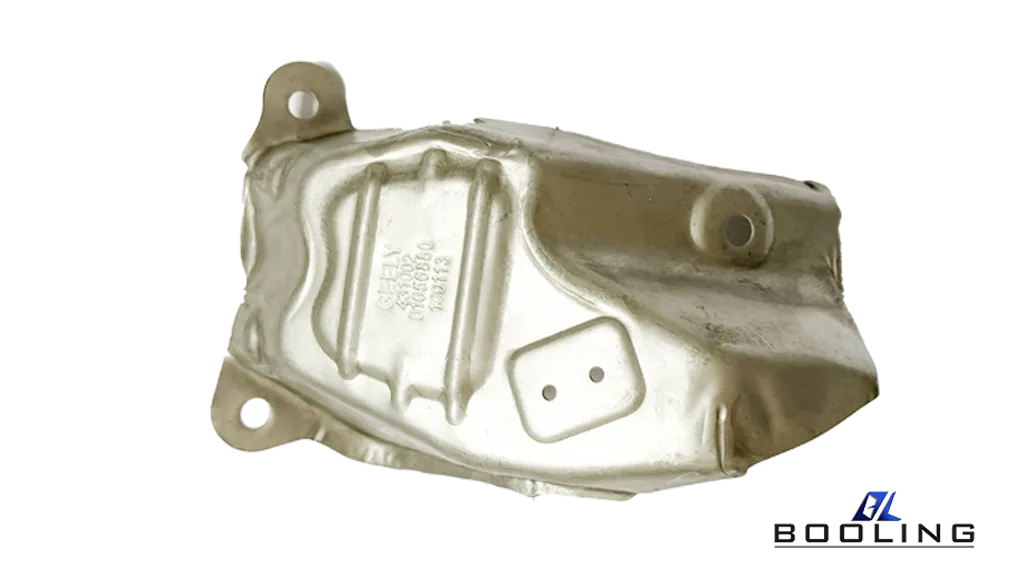
Deep Drawing Design of Metal Stamping Die
A deep drawing die, also known as a drawing die, is a commonly used stamping method that uses a metal stamping die to cut a flat blank into a specified shape and extend it into an open and hollow workpiece under the action of equipment. It can also change the shape of a workpiece that has already been made. The drawing die has five structures, mainly composed of a fixed seat, a pressing edge ring, an ejector, a concave die, and a convex die. Molybdenum vanadium cast iron can be used to cast convex dies, concave dies, and pressure rings. Then, after processing, the edges, concave dies, and rounded corners will be subjected to surface flame quenching. Using gray cast iron to cast fixed seats, an annealing treatment is used after drawing die casting to reduce casting stress.
Design principles for deep drawing convex and concave dies:The radius of the concave die corner has a significant impact on the design of deep drawing, especially if the radius of the concave die corner is too small. If the radius is too small, the tensile force will be too large, the effective pressing area will also increase, and the product is prone to cracking. If the radius is too large, the tensile force will be reduced, and the effective pressing area will be reduced. Increase the radius as much as possible without cracking. The fillet radius of the deep drawing convex die also has an impact on the deep drawing work, but it is not as obvious as the fillet radius of the concave die. In general, except for the last deep drawing, which is equal to making the bottom fillet, the fillet radius of the intermediate process is smaller than the corresponding concave die fillet radius. Calculate the fillet radius of the metal stamping die according to an empirical formula.
The design principles of convex and concave dies refer to some basic rules and principles that need to be followed in the process of designing convex and concave dies. Convex-concave dies are usually used to manufacture parts with cavity structures or convex-concave shapes, such as plastic parts, metal parts, etc. Following the design principles of convex and concave dies can ensure the manufacturing quality and service life of the dies, and improve production efficiency and product quality.
Here are several important design principles for convex and concave dies:
1.Simplify Structure: Design a simple convex and concave die structure as much as possible, reduce the number of parts, and reduce time. When designing the die structure, attention should be paid to die manufacturing and convenient operation that is beneficial to operators, while improving the quality of components.
2.Determine the Die Material: Based on the requirements of the convex and concave die design and the requirements of the parts, select the corresponding die material, determine that the die has strong strength and hardness, and ensure that it can meet the production requirements.
3.Reasonable Design: The layout of the convex and concave dies should be reasonable, and the positional relationships between various parts should be reasonable to ensure the maintainability and ease of processing of the metal stamping die. At the same time, designers should pay attention to the process requirements of part manufacturing and arrange the position and size of the metal stamping die cavity and core reasonably.
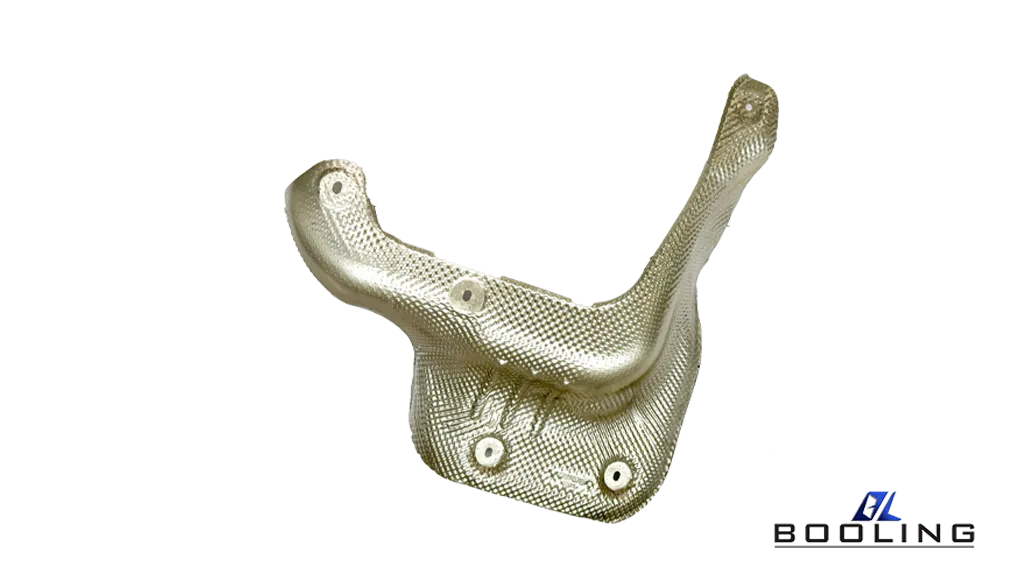
Metal Stamping Die Stamping Design
Blanking is a process of separating materials through the concave and convex dies inside the die. Metal stamping die technology is a commonly used processing method in the manufacturing industry, used to manufacture complex metal parts. The following are the designs of several components for punching:
- Die Base
The die frame mainly consists of four parts, such as upper die seat, lower die seat, guide pillar, and guide sleeve. The most commonly used type of metal stamping die design is a four-pillar die frame, which is usually made of steel plate material to form the upper and lower die seats.
Due to the different materials of the upper and lower die seats, they are generally divided into two types. The first type is cast iron formwork, and the second type is steel plate formwork.
The die frame can also be divided into two types according to the different guiding devices in the die frame. One type is a sliding guide die frame, and another type is a rolling guide die frame.
According to the installation position and number of guide pillars, there are several types of die bases, such as diagonal guide pillar die bases, four guide pillar die bases, middle guide pillar die bases, and rear guide pillar die bases.
- Design of Non-standard Die Bases
In most cases, non-standard die seat designs are commonly used when there is no standard die base selection for multi-station progressive dies. There are many types of materials used to make the die seat, such as cast iron or steel. However, the guide pillar and guide sleeve of the guiding device will still be selected as standard parts.
The shape of non-standard die seats generally takes a rectangular shape, and the length of the concave die should be the same or slightly shorter. The commonly used formula is: the length of the upper and lower die seats=the length of the concave template+the added value.
If the width of the concave die is smaller than the width of the non-standard die base, it is necessary to install a guide device on the metal stamping die base and leave a pressing plate to press and fix the position. This formula can be used to calculate: the width of the upper and lower die seats=Concave template width+twice the outer diameter of the guide sleeve+added value.
The shape and size of the upper and lower die seats should be the same, and the thickness of the lower die seat should be greater than that of the upper die seat.
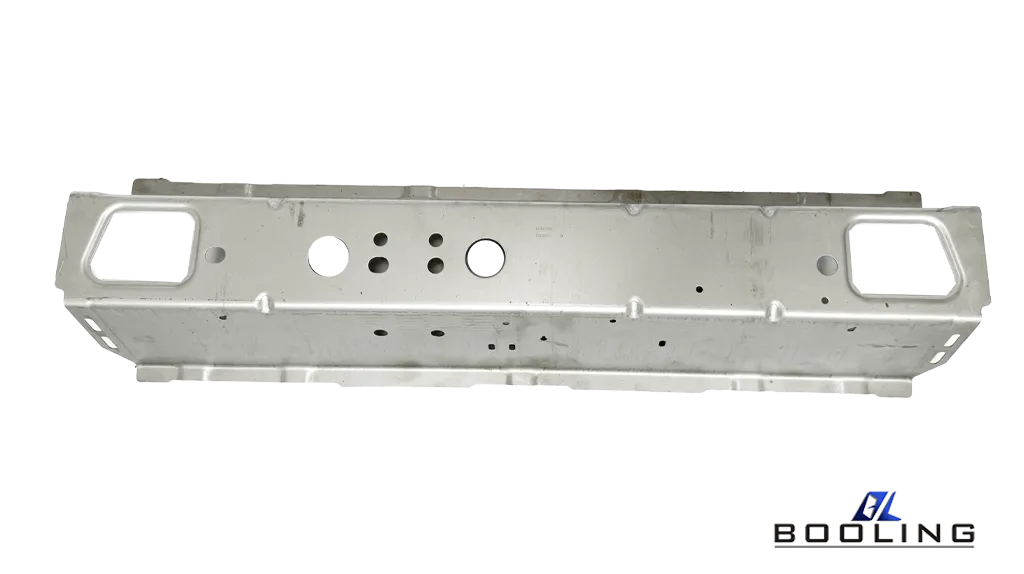
Bending Metal Stamping Die Design
The bending process of metal stamping die design is the process of stamping materials at a certain angle and shape. The size design of the bending die mainly includes the fillet radius of the convex die and the concave die, the working depth of the concave die, the gap between the concave and convex dies, the production tolerance and width dimensions between the concave and convex dies.
- Punch Fillet Radius
When the relative bending radius r/t of the bent part is small, the convex die fillet radius should be equal to or slightly smaller than the fillet radius r on the inner side of the workpiece, but not less than the minimum allowable bending radius of the material. If the relative bending radius of the workpiece is equal to the minimum relative bending radius, then the fillet radius of the punch should be greater than the minimum bending radius, and the component should reach the specified bending radius throughout the process.
- Concave Die Fillet Radius
The bending force and the quality of the components are greatly affected by the size of the concave die fillet radius. The size of the concave die fillet radius does not directly affect the fillet radius of the bent part, but a too-small concave die fillet radius increases the resistance of the material entering the concave die during bending, and then the bending force arm of the bending moment decreases, causing scratches or indentations on the surface of the component. There is also a situation where if the fillet radius of the concave die is too large, inaccurate material positioning may occur. In addition, the fillet radii on both sides of the concave die must be equal to avoid sheet metal deviation during bending. In actual production, the radius of the concave die corner is usually selected based on the material thickness. For the bending die of V-shaped parts, the bottom can have a back groove or a rounded radius can be taken.
- The Working Depth of the Concave Die
The working depth of the concave die should be designed reasonably in the design of metal stamping die, as the depth of the concave die plays an important role. One situation is that the depth is too small, which can cause the free parts at both ends of the component to be longer, the bent workpiece to rebound more, and be uneven. Another situation is that the depth of the concave die is too large, which can lead to excessive material waste, and the equipment also requires a large stroke. If the side length of the bent part of the concave die is different, the corresponding material thickness will also be different. When U-shaped bending occurs, there are also two situations. One of the situations is when the side length of the bent part is longer, but the flatness requirement is not high, then the corresponding concave die form is used. Another situation is that the height of the bending edge is not large, and it is required that both sides are straight, and the depth of the concave die cannot be less than the height of the bent part.
Related News
Applied’s expertise in modifying materials at atomic levels and on an ihdustrial scaleenables our customers to transform possibilities into reality.