Home > Stamping Die | Metal Stamping Tools
Metal Stamping Die
The production process of metal stamping die has extremely high precision. Metal materials typically have high strength and wear resistance, allowing stamping dies to withstand high-intensity impacts and pressures, and have a longer service life.
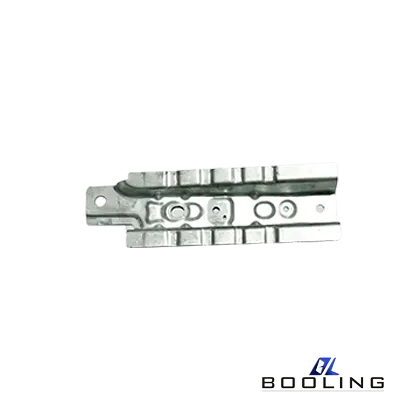
A stamping die is a special tool used for metal stamping processing. It puts a metal sheet into the die and uses the pressure of the press to deform the metal to obtain the desired shape and size. The design and manufacture of carbide stamping die are crucial to production efficiency, product quality, and cost control. They are widely used in automobiles, home appliances, aerospace, construction, electronics and other fields.
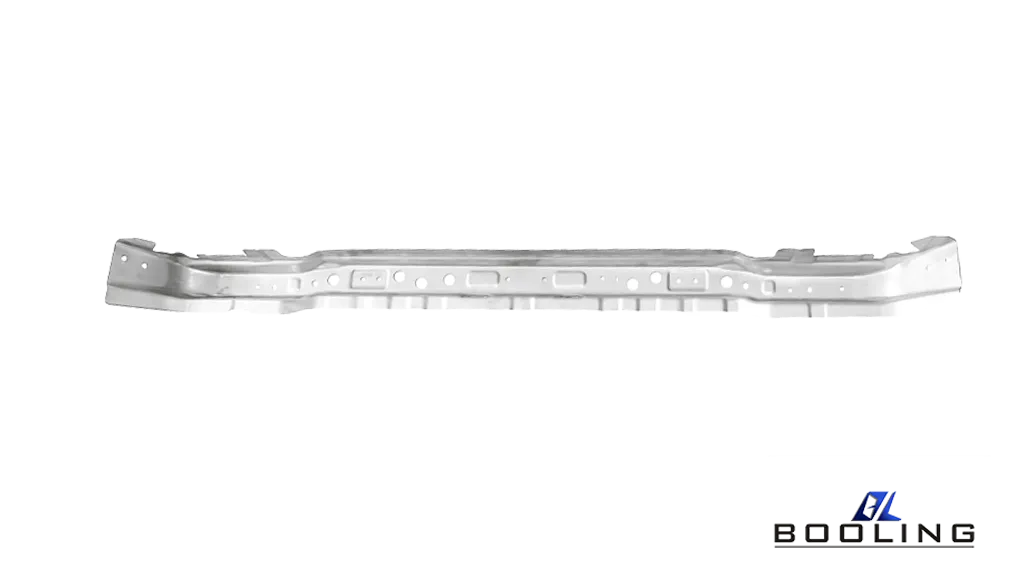
Overview of Stamping Die
At room temperature, put metal or non-metallic sheets into the metal stamping die, and apply pressure to the sheet through the press and the die installed on the press, so that the sheet separates or deforms to form the required parts. This type of part is called a stamping die.
Drawing die The most important equipment to ensure the production of qualified cover parts. Its function is to make the flat sheet into the main space workpiece through the drawing process. It is divided into two forms: positive and inverted.
- Trimming Die
It is used to cut off the process supplement part and the excess part of the pressing flange of the drawn part to prepare the conditions for flanging and shaping. In small batch production, it can be replaced by manual or other simple equipment. The trimming dies often have a punching function.
- Punching Die
A die that separates waste material along a closed contour on a blank or sheet to obtain a part with a hole.
- Flanging Die
A part that flips a part of the semi-finished workpiece relative to another part of the material.
- Shaping Die
A die that adjusts the size contour of the semi-finished product to improve dimensional accuracy and surface finish.
Structural Composition of Stamping Dies:
- Upper Die: The upper die is installed on the slide of the press and cooperates with the lower die to complete the stamping process.
- Lower Die: The lower die is installed on the workbench of the press and cooperates with the upper die to complete the stamping process.
- Punch: The punch is the active part in the upper die, which is used to extrude the metal sheet into the desired shape.
- Die: The die is the fixed part in the lower die, which cooperates with the punch to form the internal shape of the metal sheet.
- Guide pillars: The guide pillars are used to ensure the correct alignment of the upper and lower dies to prevent deviation.
- Springs: Springs are used to keep the die closed during the stamping process and to reset after the stamping is completed.
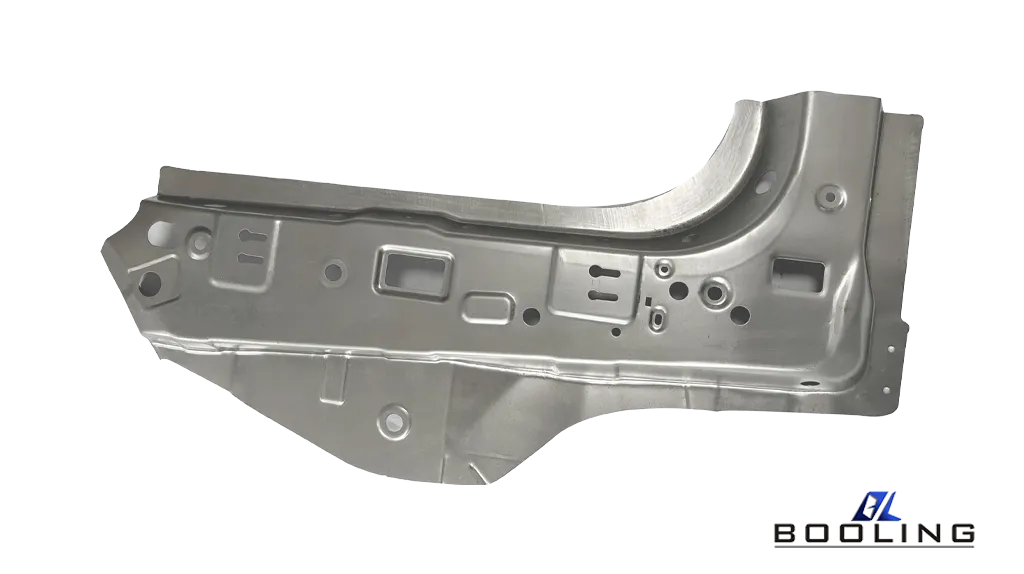
Stamping Dies Work
When the slide of the press moves downward, the punch contacts the die and clamps the metal sheet in the middle.
The press continues to apply pressure, causing the metal sheet to undergo plastic deformation under the action of the punch and die.
When the pressure reaches the predetermined value, the press stops moving and the metal sheet completes the stamping process.
Subsequently, the slide of the press moves upward, the punch and die separate, and the metal sheet is removed.
Key Points of Stamping Die Design
Accuracy: The design of the stamping die must be very precise to ensure that the size and shape of the metal sheet meet the design requirements. Any deviation may lead to product quality problems.
Material Selection: The choice of die material has an important impact on the life of the die and the quality of the product. Commonly used die materials include carbon steel, alloy steel, cemented carbide, etc.
Lubrication System: To reduce friction and wear, stamping dies usually need to be equipped with a lubrication system.
Cooling System: During long-term operation, the cooling system can help the die maintain a suitable temperature and prevent overheating.
Ejection System: The ejection system is used to eject the metal sheet from the die after stamping is completed.
- Manufacturing Process:
Design: Use CAD software to design the die according to product requirements and production needs.
Material Preparation: Select suitable die steel and perform preliminary processing such as cutting and milling.
Processing: Use CNC machine tools for precision processing to manufacture die components such as upper die, lower die, punch, and concave die.
Assembly: Assemble all die components to ensure the matching accuracy between the components.
Trial mold: Perform a trial mold on the press to check product quality and die performance. Adjust and optimize the mold according to the trial mold results.
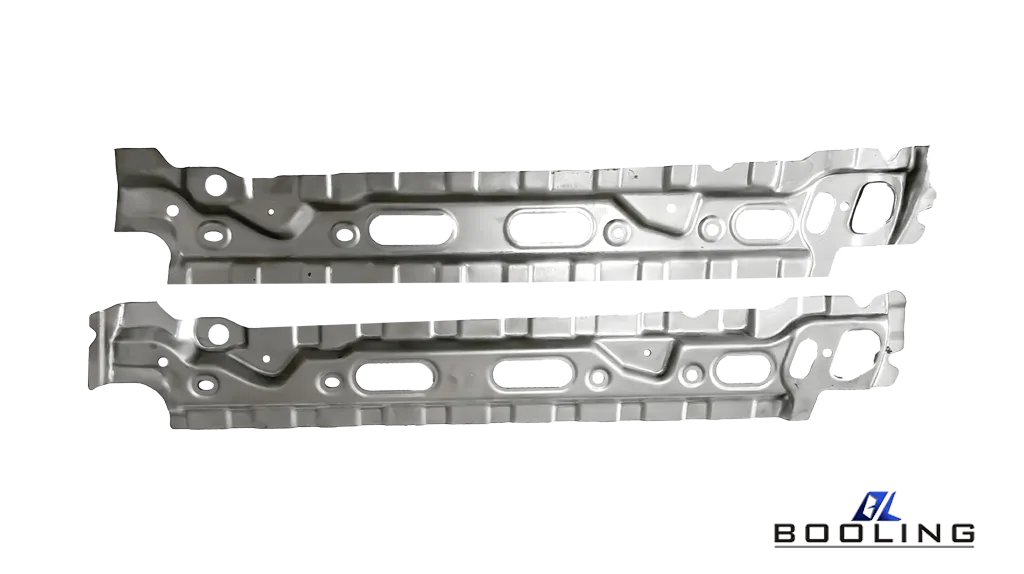
Key Points of Stamping Die Design
- Check whether the press model, mold number, and process number are consistent with the mold installation card.
- Check whether the press is operating normally and whether the air cushion height is the same.
- Check whether the length, quantity, and position of the support rod meet the requirements according to the mold installation card.
- Wipe the upper and lower bottom surfaces of the press table and the mold clean, remove foreign matter, and install after confirmation.
- Special fastening bolts and installation wrenches must be used.
- The mold is correctly placed on the movable worktable of the press through the positioning key or positioning pin.
- After the mold is driven into the press, the height between the slider and the upper mold mounting surface should be based on the installation ruler that can be placed vertically.
After the slider is opened to the lower dead center and fits the upper mold mounting surface, tighten the upper mold. Put the bolts in the lower mold plate groove and tighten them by hand; then raise the slider to the upper dead center, remove the storage limiter, and add lubricating oil to the upper and lower mold guide parts and lubricant between the male and female molds, and then run it idle for more than three times to fully and automatically guide the upper and lower molds. After confirming that there is no error, drop the slider to the lower dead center and tighten the lower mold.
Precautions in Production
- The sheet must be kept clean.
- The sheet or process parts must be correctly placed in the mold so that they are accurately positioned.
- It is strictly forbidden to drop (press) double materials.
- During the stamping process, pay attention to the falling of waste materials and remove the waste materials at any time. The waste materials in the waste box should be cleaned once every 200-400 stampings. (The specific number is determined according to different molds)
- During the operation of the press, it is strictly forbidden to readjust the position of the blank placed in the mold and clean and lubricate the mold.
- In the drawing process, it is necessary to prevent the drawing oil from not being applied or the oiling is not in place; and the entire sheet should not be oiled to prevent the drawing oil from clogging the mold vents and causing pits on the parts.
- After each work stroke, the parts should be removed from the mold in time. If the parts are found to be on the belt, the machine should be stopped and checked immediately.
- If the product is found to have quality problems or the mold is abnormal, the operation should be stopped immediately, and the inspectors and relevant technicians should be notified. Production can only be continued after the problem is solved.
- It is strictly forbidden to disassemble the mold parts and it is strictly forbidden to operate roughly.
- Wipe the oil and iron filings on the mold clean, clean the waste in the mold, and then collect the waste slide.
- Check the technical status and cleanliness of the mold.
- Put the tailpiece into the mold and put the storage limiter in place.
- Close the mold, remove the clamping bolts, put the mold into storage, and place it as required.
- Put the support rod and the clamping plate bolts into the cabinet for next use.
Related News
Applied’s expertise in modifying materials at atomic levels and on an ihdustrial scaleenables our customers to transform possibilities into reality.