Home > Types of Custom Stamping Dies by Processing Methods
Custom stamping dies are widely used by manufacturers in the manufacturing of metal parts, becoming an ideal solution for metal part manufacturing. Manufacturers need to control the characteristics, thickness, and specific shape of materials.
Advantages of Custom Stamping Die:
- Low cost
- High automation
- High accuracy
- Cost-Effectiveness
- High efficiency
- Tight tolerances
Custom Stamping dies are essential tools in the manufacturing industry, used to shape and cut materials into desired forms. These dies are classified based on their processing methods, each serving a specific purpose in the production process.
Shearing Dies
Definition and Function
Shearing dies, also known as cutting dies, are used to cut materials into specific shapes and sizes. The primary function of shearing stamping die is to separate a piece of material from a larger sheet by applying a shearing force. This process involves two main components: the punch and the die. The punch presses the material against the die, causing it to shear along a predetermined line.
- Types of Shearing Dies
- Blanking Dies: The custom stamping die is used to cut out a flat piece of material, known as a blank, from a larger sheet. Blanking is often the first step in the manufacturing process, providing the raw material for subsequent operations.
- Piercing Dies: Piercing dies create holes or cutouts in a material. This process is commonly used in the production of components that require precise holes for assembly or functionality.
- Trimming Dies: Trimming dies remove excess material from a part, ensuring it meets the desired dimensions and shape. This process is often used in the final stages of production to achieve a clean, finished edge.
- Applications
Shearing dies are widely used in various industries, including automotive, aerospace, electronics, and consumer goods. They are essential for producing components such as brackets, frames, panels, and enclosures.
- Design Considerations
Designing shearing dies requires careful consideration of factors such as material properties, thickness, and the desired shape of the cut. The clearance between the punch and die is critical to achieving a clean cut and minimizing material deformation. Additionally, the die material and coating must be selected to withstand the wear and tear of the shearing process.
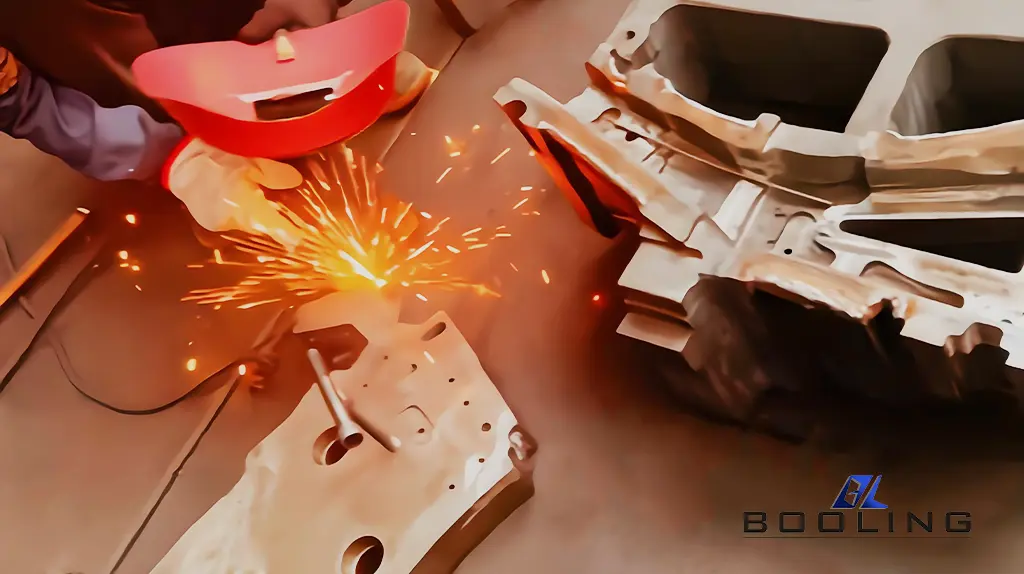
Bending Dies
- Definition and Function
Bending dies are used to deform a material to a specific angle or shape by applying a bending force. The primary function of bending dies is to create bends, folds, or curves in a material without causing it to fracture. This process involves two main components: the punch and the die. The punch presses the material into the die, causing it to bend along a predetermined line.
- Types of Bending Dies
- V-Bending Dies: V-bending dies are the most common type of bending dies, used to create V-shaped bends in a material. The die has a V-shaped groove, and the punch presses the material into the groove to form the bend.
- U-Bending Dies: U-bending dies are used to create U-shaped bends in a material. The die has a U-shaped groove, and the punch presses the material into the groove to form the bend.
- Edge Bending Dies: Edge bending dies are used to bend the edges of a material to a specific angle. This process is commonly used in the production of components that require flanges or lips.
- Applications
Bending dies are widely used in various industries, including automotive, aerospace, construction, and consumer goods. They are essential for producing components such as brackets, frames, enclosures, and structural elements.
- Design Considerations
Designing bending dies requires careful consideration of factors such as material properties, thickness, and the desired bend angle. The radius of the bend, the clearance between the punch and die, and the material’s spring back must be taken into account to achieve the desired bend. Additionally, the die material and coating must be selected to withstand the wear and tear of the bending process.
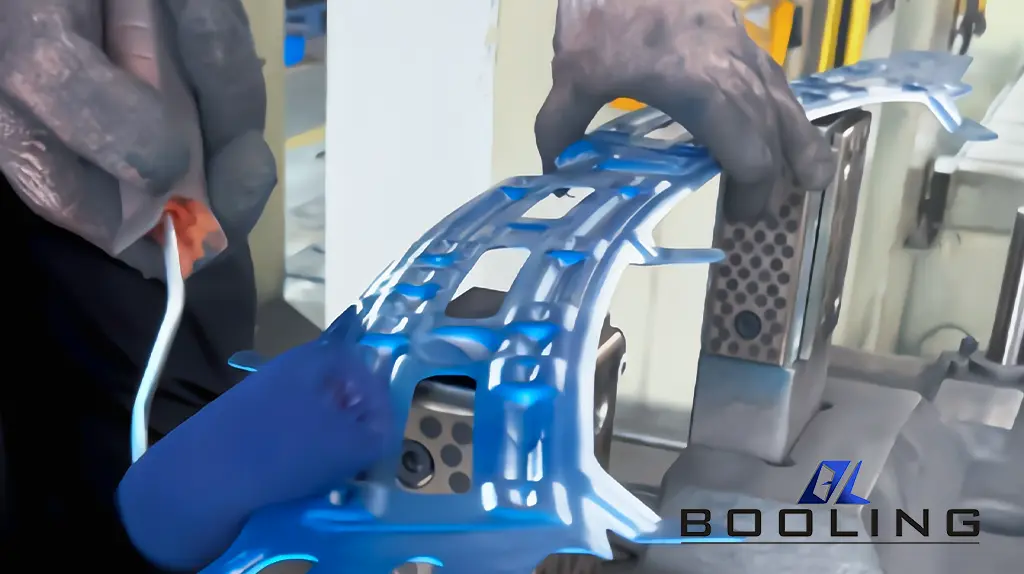
Drawing Dies
- Definition and Function
Drawing Custom metal stamping dies, also known as deep drawing dies, are used to deform a material into a specific shape by applying a drawing force. The primary function of drawing dies is to create hollow or cup-shaped parts by stretching the material into a die cavity. This process involves two main components: the punch and the die. The punch presses the material into the die cavity, causing it to stretch and form the desired shape.
- Types of Drawing Dies
- Single-Action Drawing Dies: Single-action drawing dies to perform the drawing operation in a single press stroke. These dies are used for simple shapes and shallow draws.
- Double-Action Drawing Dies: Double-action drawing dies to perform the drawing operation in two press strokes. These dies are used for more complex shapes and deeper draws.
- Progressive Drawing Dies: Progressive drawing dies to perform multiple drawing operations in a single pass. These dies are used for high-volume production of complex shapes.
- Applications
Drawing dies are widely used in various industries, including automotive, aerospace, electronics, and consumer goods. They are essential for producing components such as cups, cans, enclosures, and housings.
- Design Considerations
Designing drawing dies requires careful consideration of factors such as material properties, thickness, and the desired shape of the draw. The clearance between the punch and die, the radius of the die cavity, and the material’s durability must be taken into account to achieve the desired shape. Additionally, the die material and coating must be selected to withstand the wear and tear of the drawing process.
Forming Dies
- Definition and Function
Forming dies are used to deform a material into a specific shape by applying a forming force. The primary function of forming dies is to create complex shapes and contours in a material without causing it to fracture. This process involves two main components: the punch and the die. The punch presses the material into the die, causing it to deform along a predetermined path.
Types of Forming Dies
- Coining Dies: Coining dies are used to create precise, detailed shapes and patterns in a material. This process involves pressing the material into a die cavity with high force, causing it to flow and fill the cavity.
- Embossing Dies: Embossing dies are used to create raised or recessed designs in a material. This process involves pressing the material into a die with a patterned surface, causing it to deform and take on the pattern.
- Flanging Dies: Flanging dies are used to create flanges or lips on the edges of a material. This process involves pressing the material into a die with a flanged surface, causing it to bend and form the flange.
- Applications
Forming dies are widely used in various industries, including automotive, aerospace, electronics, and consumer goods. They are essential for producing components such as decorative panels, enclosures, housings, and structural elements.
- Design Considerations
Designing forming dies requires careful consideration of factors such as material properties, thickness, and the desired shape of the form. The clearance between the punch and die, the radius of the die cavity, and the material’s formability must be taken into account to achieve the desired shape. Additionally, the die material and coating must be selected to withstand the wear and tear of the forming process.
Compression Dies
- Definition and Function
Compression dies are used to compress a material into a specific shape by applying a compressive force. The primary function of compression dies is to create dense, solid parts by compacting the material into a die cavity. This process involves two main components: the punch and the die. The punch presses the material into the die cavity, causing it to compress and take on the desired shape.
- Types of Compression Dies
- Cold Compression Dies: Cold compression dies are used to compress materials at room temperature. This process is commonly used for materials that do not require heating to achieve the desired shape.
- Hot Compression Dies: Hot compression dies are used to compress materials at elevated temperatures. This process is commonly used for materials that require heating to achieve the desired shape.
- Isostatic Compression Dies: Isostatic compression dies are used to compress materials uniformly from all directions. This process is commonly used for materials that require uniform density and strength.
- Applications
Compression dies are widely used in various industries, including automotive, aerospace, electronics, and consumer goods. They are essential for producing components such as gears, bearings, bushings, and structural elements.
- Design Considerations
Designing compression dies requires careful consideration of factors such as material properties, thickness, and the desired shape of the compression. The clearance between the punch and die, the radius of the die cavity, and the material’s compressibility must be taken into account to achieve the desired shape. Additionally, the die material and coating must be selected to withstand the wear and tear of the compression process.
Custom Stamping dies are indispensable tools in the manufacturing industry, enabling the production of high-quality, precision components essential for various applications. The classification of custom stamping dies by processing methods—shearing dies, bending dies, drawing dies, forming dies, and compression dies—highlights the diverse functions and applications of these tools.
Stamping Die Related Content
Applied’s expertise in modifying materials at atomic levels and on an ihdustrial scaleenables our customers to transform possibilities into reality.