Home > Custom Stamping Die | Processing Technology Overview
Details
Details:
Model
Material
Brand
Origin
Application
Booling-Stamping Die-1
P20, 718, S136, 2738 etc
Booling
China
Home Appliance parts
The custom stamping die uses the precise matching and dynamic stamping of the upper and lower dies to form metal sheets into precision parts that meet the design requirements. This technology is suitable for mass production of automotive sheet metal parts, electronic hardware, home appliance housings, building components, and other products. It is mainly composed of a die base, a guide mechanism, a punch, a die, a material ejection device, and a quick die change system. Based on our more than ten years of technical accumulation and 800+ successful case verifications, the stamping die optimized by CAD/CAE simulation can achieve a forming accuracy of ±0.01mm. Through intelligent die surface compensation technology, it can not only meet the needs of complex surface processing but also increase the die life to more than 3 times that of ordinary molds.
Advantages of custom stamping die processing:
- Long life
- High processing accuracy
- High production efficiency
- Meet personalized customization needs
Related Hot Products
Booling provides efficient solutions for the automotive manufacturing industry through custom multi-station progressive stamping dies and other advanced manufacturing processes. Our technology significantly improves the level of automation, reduces production processes, shortens the molding cycle, and controls the single stamping cycle time to less than 0.8 seconds. With mature and successful cases, we help automotive sheet metal manufacturers achieve fast and large-scale production to meet the needs of high-precision and high-efficiency large-scale manufacturing.
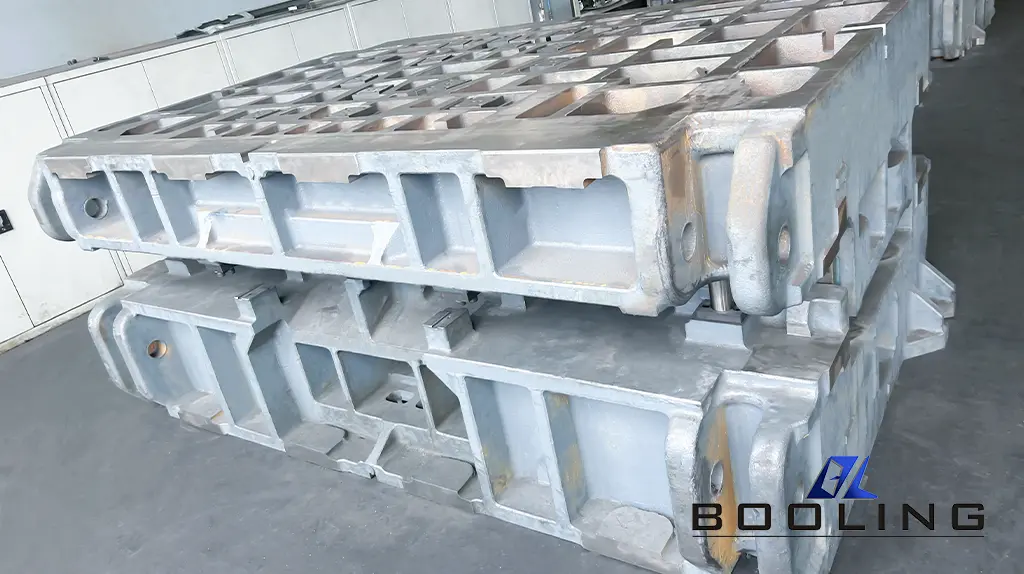
Basic Classification of Custom Stamping Die
At Booling, we provide you with a scientific classification scheme based on process requirements to ensure that each set of the custom stamping die can perfectly match the production scenario of the factory.
-Classification by process properties
- Bending die: By applying external force, the metal sheet is plastically deformed to achieve the bending effect.
- Punching die: By applying pressure, the metal sheet is separated. According to different processes, punching dies can be divided into blanking dies, punching dies, cutting dies, notching dies, trimming dies, cutting dies, and other models.
- Drawing die: Drawing dies are mainly used for processing sheet metal and thin-walled parts. They can be made into open hollow parts and can also change the shape of thin-walled hollow products.
- Riveting die: The riveting die connects the two parts through the cover and hole at one end. External force processing is required when connecting so that the two parts form a whole.
- Forming die: The raw material or semi-finished product is directly formed into a concave and convex die shape. This type of die will only deform or form the blank locally. Forming dies can be divided into bulging dies, shrinking dies expanding dies, etc., and the forming method is relatively flexible.
-Classification by process combination degree
- Single process die: In one stroke of the press, the single process die only completes one stamping process. It has a relatively simple structure and low cost.
- Compound die: In one stroke of the press, the compound die can complete two or more stamping processes. When using a compound die, the material does not need to be fed and moved, which can improve production efficiency and reduce production costs.
- Progressive die (also called multi-station progressive die or continuous die): A progressive die, is divided into several equidistant stations according to the workpiece to be processed. One or several basic stamping processes are set at each station to realize the processing of sheet metal parts. The advantage of the progressive die is that it can complete complex multiple processes in one die, reduce repeated positioning, and improve production efficiency.
- Transfer die: The transfer die combines the characteristics of the progressive die and the single process die. When using a transfer mold, the product can be quickly transferred in the mold by a robot, which can reduce the transfer and processing time. Transfer molds are often used in production lines with a high level of automation and are suitable for the mass production of complex parts.
“We not only provide molds but also provide the most optimized process combination solutions.” ——Booling Engineering Team
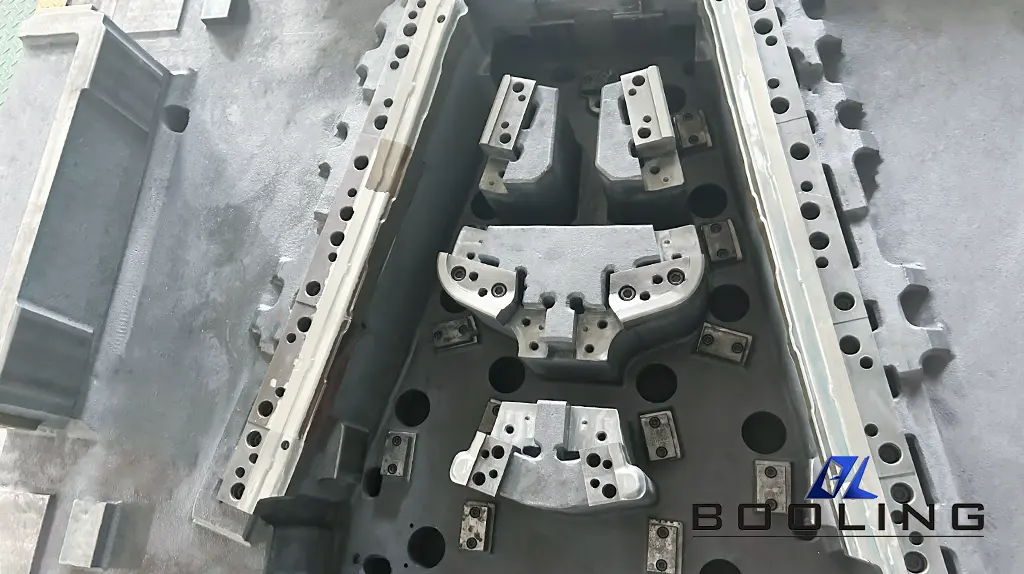
Core Performance of Custom Stamping Die
At Booling, we know that the hardness, wear resistance, and life of the die are directly related to the production benefits of customers, so we use dynamic simulation technology to achieve the best material configuration.
- Ultra-high hardness: The hardness requirement depends on the working conditions of the die, the characteristics of the material, and the production batch of the product. Custom stamping dies are often subjected to high pressure during use, and the selected material needs to have sufficient hardness to ensure that there will be no deformation during use.
- Excellent wear resistance: The wear resistance of steel determines the service life of the custom stamping die. Dies made of steel with good wear resistance have a longer service life. If the steel has poor wear resistance, the die will become rough due to the inability to withstand greater stress and friction during use, resulting in the die being unusable before the end of its service life.
- Elasticity and fatigue resistance: The custom stamping die i usually used to process sheet metal materials. During the processing process, the die will be subjected to strong and lasting impact, distortion, bending, and vibration. Therefore, the material used to make the die must have good toughness and fatigue resistance to prevent the die from cracking or breaking due to stress.
Each set of molds is strictly tested before leaving the factory. We promise not only the parameters but also the stable performance.

Special Properties of Custom Stamping Die
For special working conditions, we give the dies more excellent performance through material science and process innovation:
- Red hardness: Red hardness is also called thermal stability, which is used to evaluate the ability of stamping dies to maintain material stability in high-speed and high-temperature working environments. Mold steel with good red hardness can keep the sharp edge from deforming at high temperatures and maintain good hardness and strength.
- Low adhesion: Low adhesion and high fluidity can prevent two metal atoms from diffusing with each other on the mold surface, thereby avoiding the generation of metal adhesion, affecting the use of custom stamping dies and the quality of the final metal parts. Especially for deep drawing dies, the requirements for this special property are relatively high.
- Excellent anti-bite force: Good anti-bite force can prevent cold welding of processed metals. Manufacturers mainly adjust the anti-bite force according to the actual working conditions and performance of the mold.
We build a complete quality traceability system to ensure the quality of custom stamping dies, and the material utilization rate can reach 93.5% or above. While saving materials, the qualified rate is ensured, and the needs of customers are responded to and met quickly.
Booling’s commitment: smarter and more reliable stamping die solutions
From design to delivery, we insist on:
24-hour rapid response to technical consultation
1-on-1 expert team to follow up throughout the process
Lifelong maintenance service commitment
Choose Booling, choose a reliable partner for custom stamping dies!
Whether it is automotive parts, electronic precision parts or home appliance components, we can provide you with cost-effective custom solutions. Contact us now to get exclusive solutions!
Automotive Mold Related Content
Applied’s expertise in modifying materials at atomic levels and on an ihdustrial scaleenables our customers to transform possibilities into reality.