Home > Injection Molding > Thermoplastic Injection Molding
Booling has extensive experience in thermoplastic injection molding and key process technologies such as material preparation, plasticization, injection, pressure holding, cooling, and curing. Our engineers can accurately depict complex details in a short cycle time by precisely controlling parameters such as temperature, pressure, and time during the processing. With the wide applicability of thermoplastic injection molding technology, Booling has provided rapid manufacturing services for plastic products and molds to countries such as the United States, Argentina, India, and Russia.
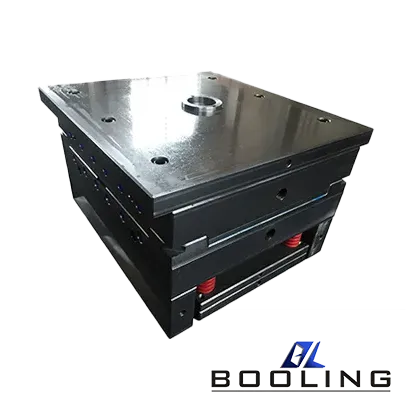
Injection molding is the most commonly used solution for thermoplastic processing. Booling provides single-cavity, multi-cavity, cold-runner, and hot-runner molds to meet the processing needs of different products.
- Single Cavity
- Multi-Cavity
- Hot Runner
- Cold Runner
- Two-Plate
- Three-Plate
Thermoplastic Injection Molding Capabilities
Thermoplastic injection molding has excellent processing performance and allows the use of a variety of materials and additives to improve the overall performance of the product.
·
US
Metric
PVC
59 in. x 51.2 in. x 17.7 in.
1500mm x 1300mm x 450mm
PS
59 in. x 51.2 in. x 17.7 in.
1500mm x 1300mm x 450mm
PP
59 in. x 51.2 in. x 17.7 in.
1500mm x 1300mm x 450mm
PE
59 in. x 51.2 in. x 17.7 in.
1500mm x 1300mm x 450mm
*The products provided by thermoplastic injection molding are recyclable, greatly reducing costs.
Thermoplastic Injection Molding Material
Thermoplastic injection molding has a wide range of applications. Booling offers both general-purpose plastics and engineering plastics for processing.
Material
- Polyethylene (PE)
- Polypropylene (PP)
- Polyvinyl chloride (PVC)
- Polystyrene (PS)
- Polyoxymethylene (POM)
- Polycarbonate (PC)
- Polyamide (PA)
- Methyl methacrylate (PMMA)
- Polyurethane Elastomer (TPEE)
- Thermoplastic polyurethane (TPU)
- Styrene based thermoplastic elastomers (TPR/TPE)
The Advantage & Disadvantage of Thermoplastic Injection Molding
- Rich material selection, high flexibility and adaptability
- Ability to form various complex geometric shapes with strict tolerance standards
- The most prominent advantage of thermoplastics is their excellent processability, low viscosity, and high product qualification rate
- Cost-effective, able to create a large number of complex shapes in a short time
- Thermoplastics are recyclable, and their plasticization and melting produce physical changes, and the solidified waste can be used again
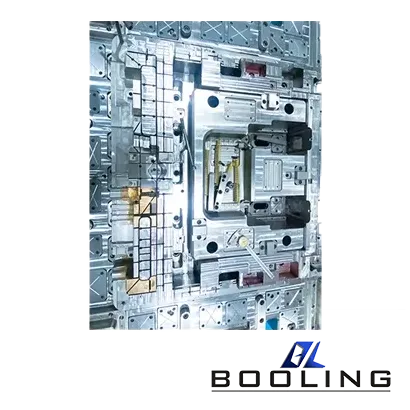
Application of Thermoplastic Injection Molding
Thermoplastic injection molding technology is widely used in the processing of high-precision products, especially in the automotive and smart home industries. These products include fuel tanks, front and rear lampshades, bumpers, and most interior decorations, as well as TVs, refrigerators, air conditioner shells, and structural components.
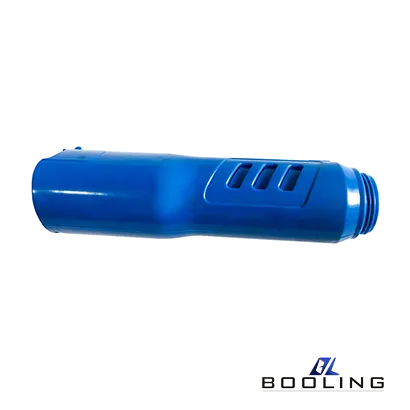
Guidelines for Thermoplastic Injection Molding
Thermoplastic injection molding technology has excellent performance and is an ideal choice for large-scale product production.
Thermoplastic molding requires precise molds, and the molding process is cumbersome, involving multiple stages, such as mold design and processing, material selection and pretreatment, plasticizing and melting, injection, pressure holding, cooling, and ejection. Booling achieves precise control of each step to ensure the consistency of the final product quality.
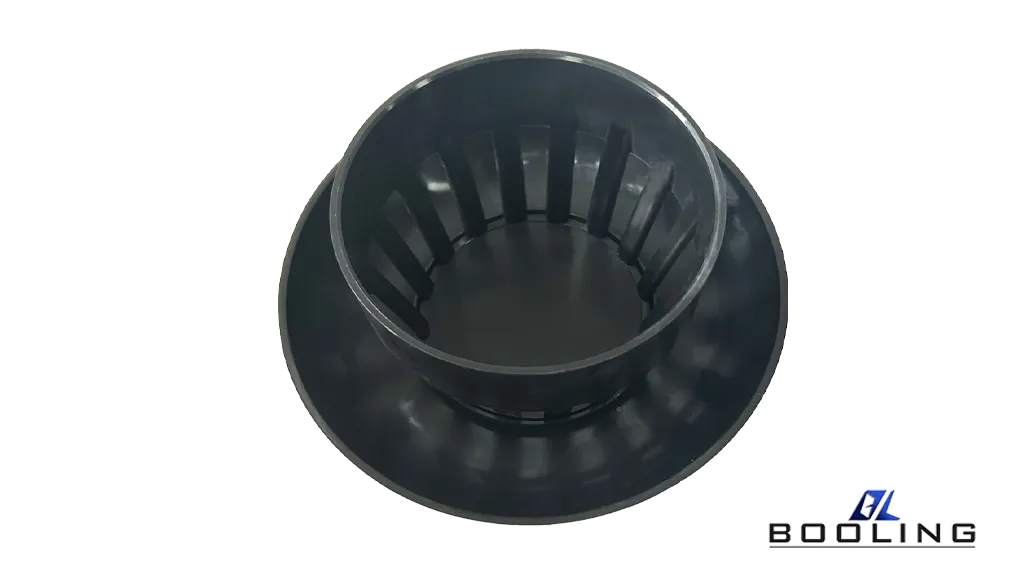
Thermoplastic Injection Molding Material Preparation
The processing of thermoplastics is reversible. After heating and melting, they can be recycled without affecting the performance.
Thermoplastics are composed of long-chain monomers, which directly affect the melting point, strength, and processability of the material. Booling can adapt to the processing of corresponding products by adjusting the molecular composition and processing technology of the material to achieve customization and versatility.
- Polyethylene (PE): Booling provides materials such as HDPE and LDPE, which have the advantages of lightweight and moisture resistance
- Polypropylene (PP): It has a high melting point and chemical resistance and can be used in the manufacture of food containers, automotive parts, daily necessities, etc.
- Polyvinyl chloride (PVC): PVC has excellent mechanical strength and chemical resistance. Common applications include building materials, pipes, cable insulation layers, etc.
- Polycarbonate (PC): Polycarbonate has excellent impact resistance and transparency. It is used in optical fields such as microscopes and eyeglasses and the production of front and rear lampshades of automobiles
- ABS: ABS material has excellent toughness, rigidity, and chemical properties. It can be used in the processing of automobile bumpers, luggage racks, electrical housings, etc.
Maintenance Program for Thermoplastic Injection Molding
Booling provides a comprehensive guide for preventive maintenance of thermoplastic injection molding molds to ensure optimal mold performance and extend service life.
- Regular inspection: Set up regular inspection times to check the mold surface, cavity, and structural components for wear, rust, or other defects. If there are any, they need to be repaired as soon as possible.
- Cleaning: Clean the plastic, debris, and contaminants left in the mold before or after each start-up, which will cause wear during the processing. Booling uses solvent and ultrasonic cleaning solutions to ensure mold accuracy while cleaning.
- Lubrication and maintenance of moving parts: Moving parts can keep the mold running smoothly, such as ejectors, core pullers, and sliders, but they are prone to wear, so lubricants need to be added or replaced regularly.
- Part replacement: For some parts such as ejectors and inserts, wear may occur and it is difficult to repair. At this time, they need to be remade for replacement to shorten downtime.